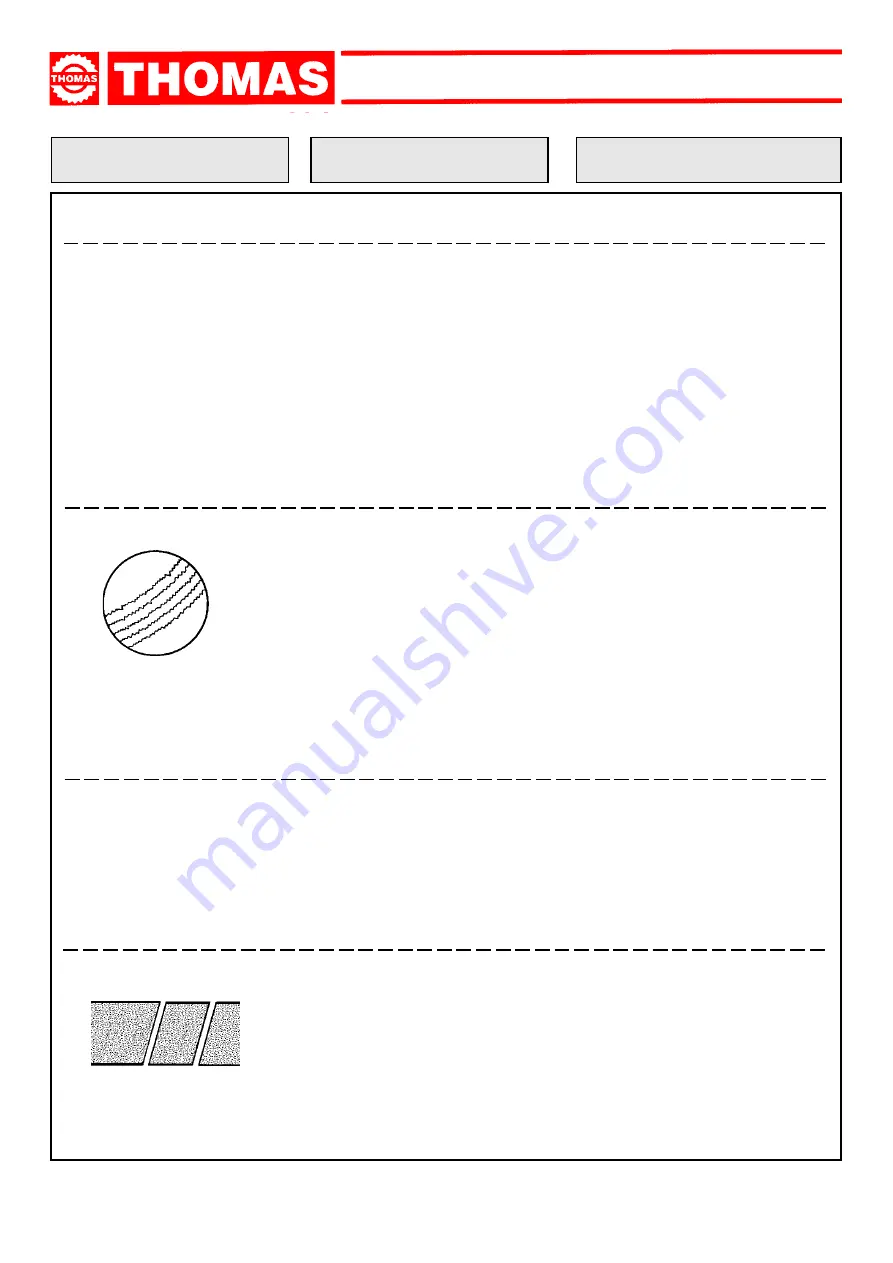
20
SUPER CUT
SUPER CUT
SUPER CUT
SUPER CUT
SUPER CUT
FAULT
PROBABLE CAUSE
REMEDY
Wrong tooth pitch
Unsuitable tooth profile
Ineffective gripping of the part in the
vice.
Dimensions of the solid section too
large with respect to the maximum
admissible cutting dimensions
Disk diameter incorrect and/or too
large
Choose a suitable disk.
See Chapter “Material classification
and choice of disks” .
Choose a suitable disk.
See Chapter
“Material classification
and choice of disks”
in the paragraph
on Type of disks.
Check the gripping of the part.
Abide by the instructions.
Decrease the disk diameter, adapting it
to the dimensions of the part to be cut;
the cutting part of the disk must not be
too large for the shape of the part to be
cut.
DISK VIBRATION
CUTS OFF THE STRAIGHT
Decrease advance, exerting less cutting
pressure.
Check the gripping of the part which may
be moving sideways.
Adjust the head.
Choose tool quality carefully in every detail
as regards type and construction cha-
racteristics.
Carefully clean the laying and contact
surfaces.
BLADE STICKS IN THE CUT
Too fast advance
Low cutting speed
Wrong tooth pitch
Sticky accumulation of material on
the disk.
Insufficient lubricating refrigerant
Decrease advance, exerting less cutting
pressure.
Increase speed.
Choose a suitable disk.
See Chapter “Material classification
and choice of disks” .
Check the blend of lubricating coolant and
choose a better quality disk.
Check the level of the liquid in the tank.
Increase the flow of lubricating refrigerant,
checking that the hole and the liquid outlet
pipe are not blocked.
Incorrect emulsion of the lubricating
refrigerant
Check the percentage of water and oil in
the emulsion.
Too fast advance
Ineffective gripping of the part in the
vice
Disk head off the straight
Disk sides differently sharpened.
Disk thinner than the commercial
standard.
Dirt on the gripping device
Disk diameter incorrect and/or too
large
Ineffective gripping of the part in the
vice.
Too fast advance
Disk teeth are worn
Insufficient lubricating refrigerant
Toothing does not unload shavings
well
RIDGES ON THE CUTTING SURFACE
Decrease the disk diameter, adapting it
to the dimensions of the part to be cut;
the cutting part of the disk must not be
too large for the shape of the part to be
cut.
Check the gripping of the part.
Decrease advance, exerting less cutting
pressure.
Sharpen the tool.
Check the level of the liquid in the tank.
Increase the flow of lubricating refrigerant,
checking that the hole and the liquid outlet
pipe are not blocked.
Choose a blade with a larger tooth pitch
that allows better unloading of shavings
and that holds more lubricating refrigerant.