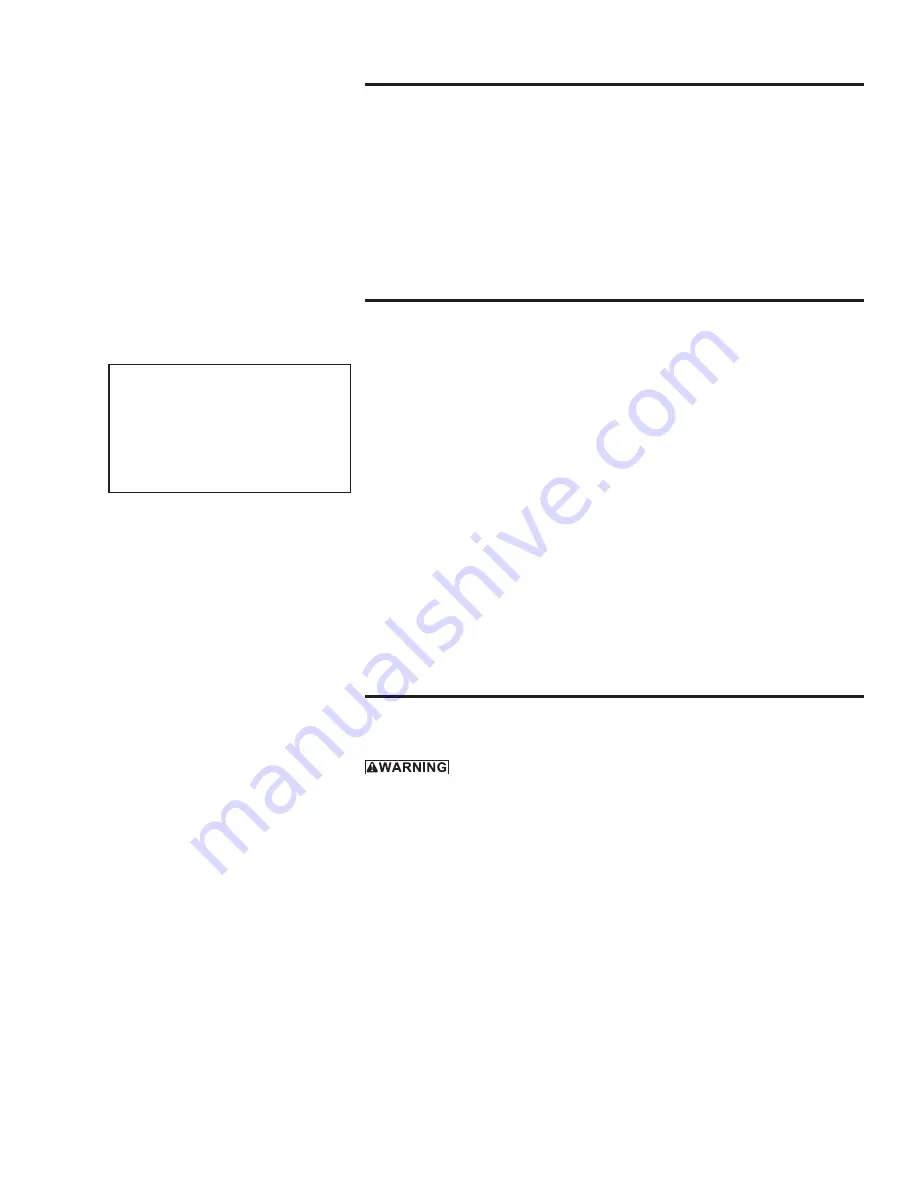
Owner's Manual for Thern DW1M1-S4 Capstan
page 9
SA9895A-0316
2.2
Breaking-In the Unit
2.2.1
BREAK-IN OCCURS
during the first few hours of normal operation. During
break-in, mating surfaces become polished, and clearances increase. This is
desired for efficient operation of bearings and gears.
2.2.2
INSPECT THE UNIT following break-in according to the Instructions for
Periodic Inspection. See section 3.3 - Inspecting the Equipment.
2.3
Preparing for Operation
2.3.1
CONSIDER THE OPERATION. Do not begin until you are sure you can
perform the entire operation without hazard.
2.3.2
INSPECT ALL COMPONENTS of the system.
a
INSPECT THE UNIT and other equipment according to the Instructions for
Frequent Inspection.
b
OPERATORS must be in good health, alert, thoroughly trained in operating
the equipment, and properly clothed (hard hat, safety shoes and safety
glasses, no loose clothing).
c
THE LOAD must be clear of other objects and free to move. Make sure the
load will not tip, spin, roll away, or in any way move uncontrollably.
2.3.3
KNOW YOUR LOAD and make sure you do not exceed the load rating of
the unit or any other equipment in the system.
2.4
Attaching the Load
Do not wrap the synthetic fiber rope around the arbor. This damages the
synthetic fiber rope and could cause the load to escape. Use an approved
lifting device.
2.4.1
CLEAR OBJECTS from the path of the load so you can move it freely and
observe it at all times during the operation.
2.4.2
ROLL CAPSTAN
into space adjacent to the floor block of the desired
lineset until the reaction bar anchor is fully engaged to the reaction bar.
See Figure 3.
2.4.3
ATTACH THE FIBER ROPE TO THE LOAD using a rated lifting shackle,
or other approved lifting device. Follow the recommendations of the shackle
manufacturer.
2.4.4
DO NOT ATTEMPT to move an arbor that is not directly above the capstan
lead sheave. Reposition the capstan to achieve the least amount of fleet angle
between the lead sheave and the arbor.
Important!
• When determining whether the
load will exceed the load rating,
consider the total force required
to move the load.