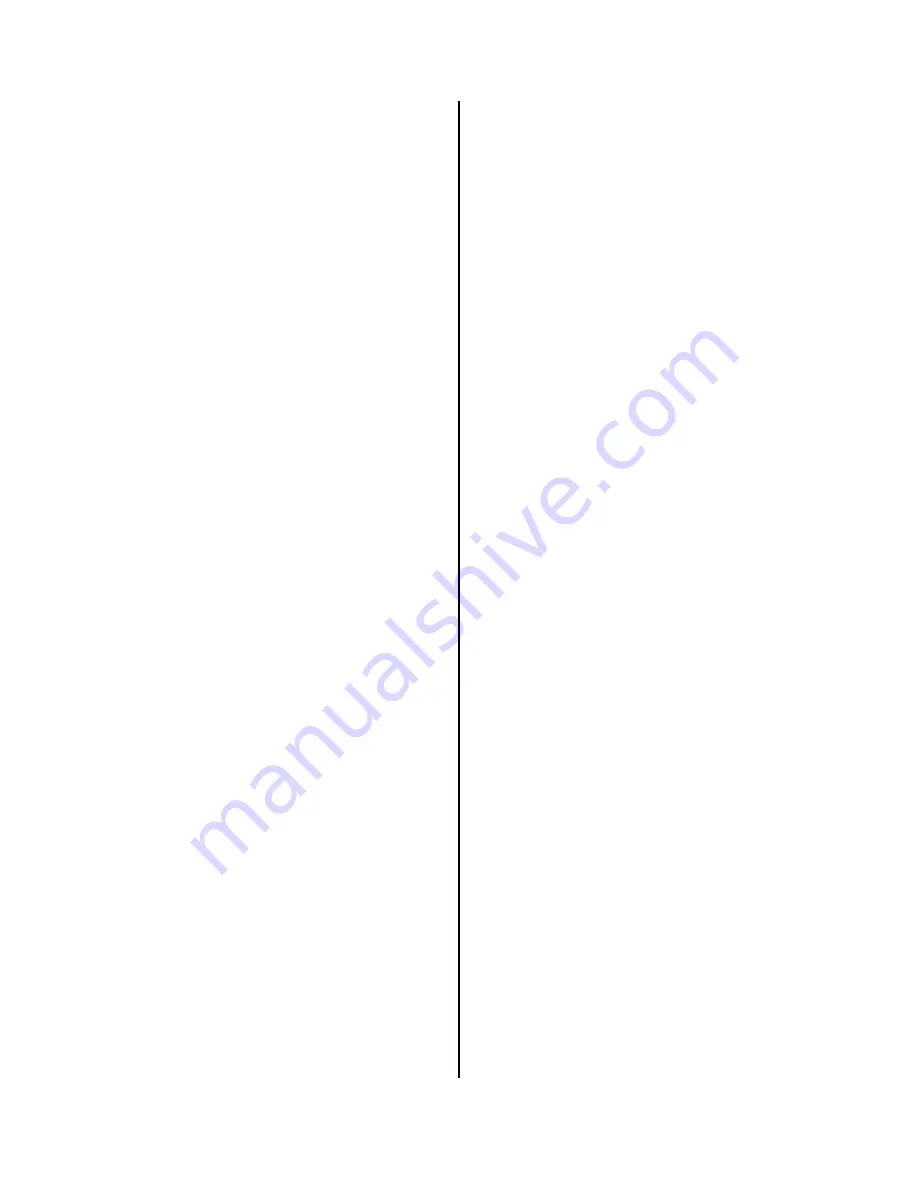
ICE RINK DEFOGGER
Allow a minimum of four feet clearance from any
obstruction on the return side of the unit.
Check that the unit will not block the view if the ice
rink has a spectator area. The unit can be moved as
long as the discharge location is not affected.
Use anti-vibration pads such as machinery cork or
rubber pads to isolate the unit from the supportive
structure. The units are normally installed on
platforms (see drawing). DO NOT mount units on
plywood sheets or similar materials, which are
prone to cause resonance.
Step 3
Condensate Drain
The unit has a 1-1/4" MPT drain connection. The
drain line and external P-TRAP must be heated if
the machine is to operate at temperature below
freezing.
Step 4
Electrical Hook-up
Provide and install a main disconnect switch within
the vicinity of the unit. Refer to the unit nameplate
for proper voltage, ampacity and maximum main
fuse protection. Wires and main disconnect switch
should be provided in accordance with local
electrical codes. Use copper conductors only.
Power leads are brought into the unit through the
top or bottom of the main control panel. Supply
voltage must not vary more than 10% of the
nameplate voltage. Unbalanced phase voltage must
not exceed 2% between phases. Ensure that the
unit is connected to the ground lug terminal, located
in the control panel.
The unit is controlled by a humidistat (factory
installed). Control voltage is 240 volts. If a remote
on/off switch (supplied by others) is installed, mount
the on/off switch in a convenient location using
wiring according to the local electrical codes. The
switch provided should be a double pole switch, so
that two units can use the same switch.
Step 5
Discharge Duct Extension
Provide a 36 inch (0.9 m) discharge duct extension
complete with horizontally and vertically adjustable
louvers.
IMPORTANT!!!
Before starting up the IRD, enclosure
temperature must be between 30°F and 80°F (-
1°C and 27°C).
Step 6
Leak test the entire unit. Abnormal transportation
and handling shocks may have caused a refrigerant
leak. In case of solder repair use an inert gas to
prevent scale formation in tubing.
Step 7
Wire connections may become dislodged or
loosened during shipment. Check screws for
tightness.
Step 8
Check drain connection. Test condensate drain by
pouring water into the drip pan. This will also fill P-
trap. The access panel must be removed for this
procedure.
Step 9
Check to see that clean filters are installed. If filters
are dirty, check coils. Dirty coils must be cleaned
and filters replaced.
Step 10
Move on/off switch on the unit to the OFF position.
Step 11
Check line voltage to match with unit nameplate.
Install line voltage disconnect switch (see field
wiring diagram). Connect power supply. Check
ground connections.
Step 12
Wire the remote manual on/off switch to the
terminals on the panel and move switch to OFF
position.
Step 13
Turn the power on. For compressors without service
valves the crankcase heater must be energised at
least one hour before start-up. The crankcase
heaters are energised as soon as power is supplied
to the unit (if so equipped).
Step 14
Move unit on/off switch to the ON position. Move the
remote on/off switch to the ON position.
Step 15
After the initial time delay, the compressor and
blower will start. Control light indicates compressor
in operation. If the compressor does not start
(locked rotor) or knocks during start-up, stop the
compressor and leave the crankcase heater on for
at least 12 hours before attempting start-up again.