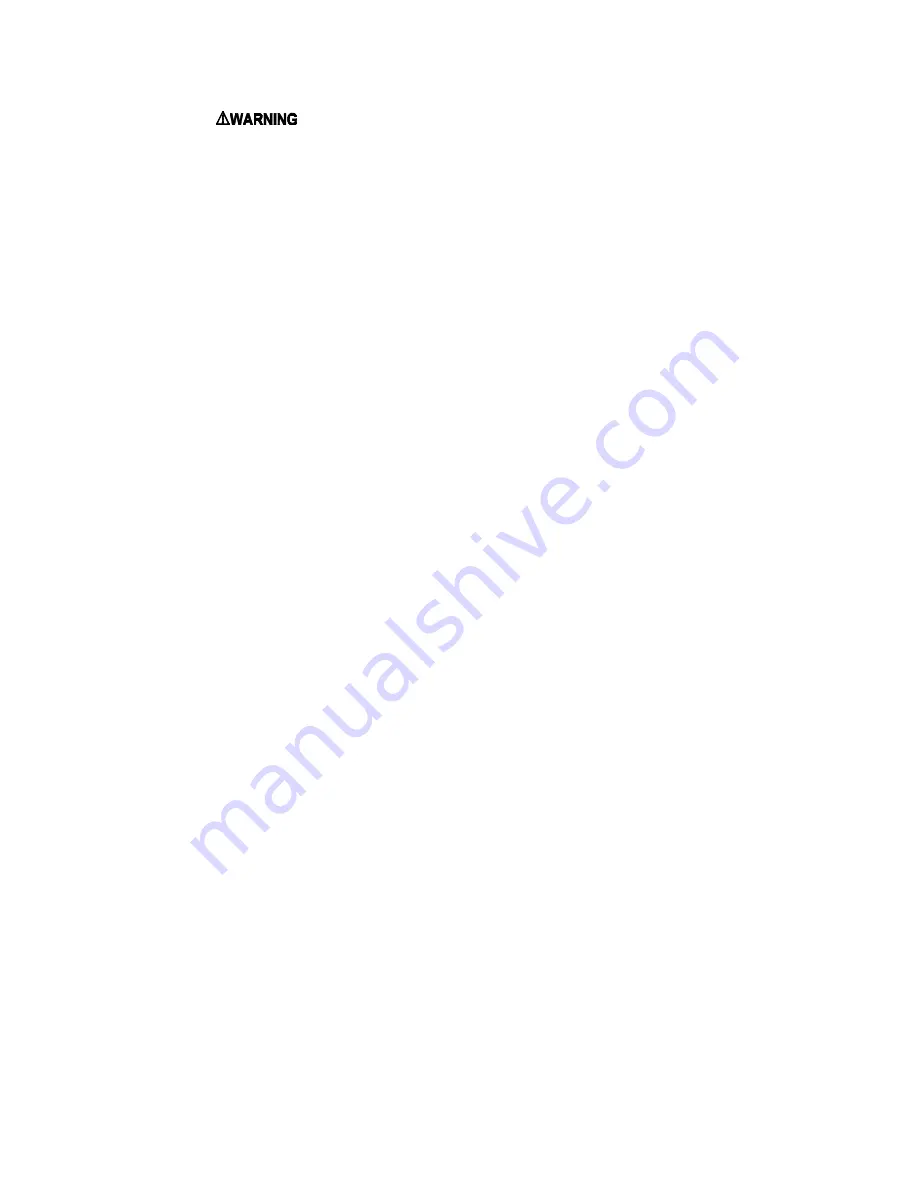
40
: TURN OFF THE ELECTRICAL POWER to the furnace
before attempting to change blower speed wiring.
The furnace is factory wired to the ignition control with standard heating
and cooling speeds. When changing motor speeds, simply switch the
needed speed to either the heating or cooling terminal as applicable on
the module to obtain the desired CFM. The unused speeds should then be
reconnected to the module in the “park” positions. (Refer to figure 15)
Refer to section II for blower speed and air flow performance for A/C
installation.
5. FIELD WIRING AND REPLACING WIRING
Field wiring between the furnace and devices not attached to the furnace shall
conform with the temperature limitation for Type T 35 C wire. If any of the original
factory supplied furnace wiring is replaced or a separate device other than the
thermostat is wired internal to the unit 105
C thermoplastic or equivalent wire
must be used.
Summary of Contents for CMA4-50D36N
Page 2: ......
Page 38: ...33 4 BLOWER MOTOR SPEED WIRING Figure 15...
Page 62: ...57 APPENDIX A REPLACEMENT PARTS...
Page 63: ...58...
Page 64: ...59...
Page 65: ...60...
Page 66: ...61 APPENDIX B WIRING DIAGRAMS...