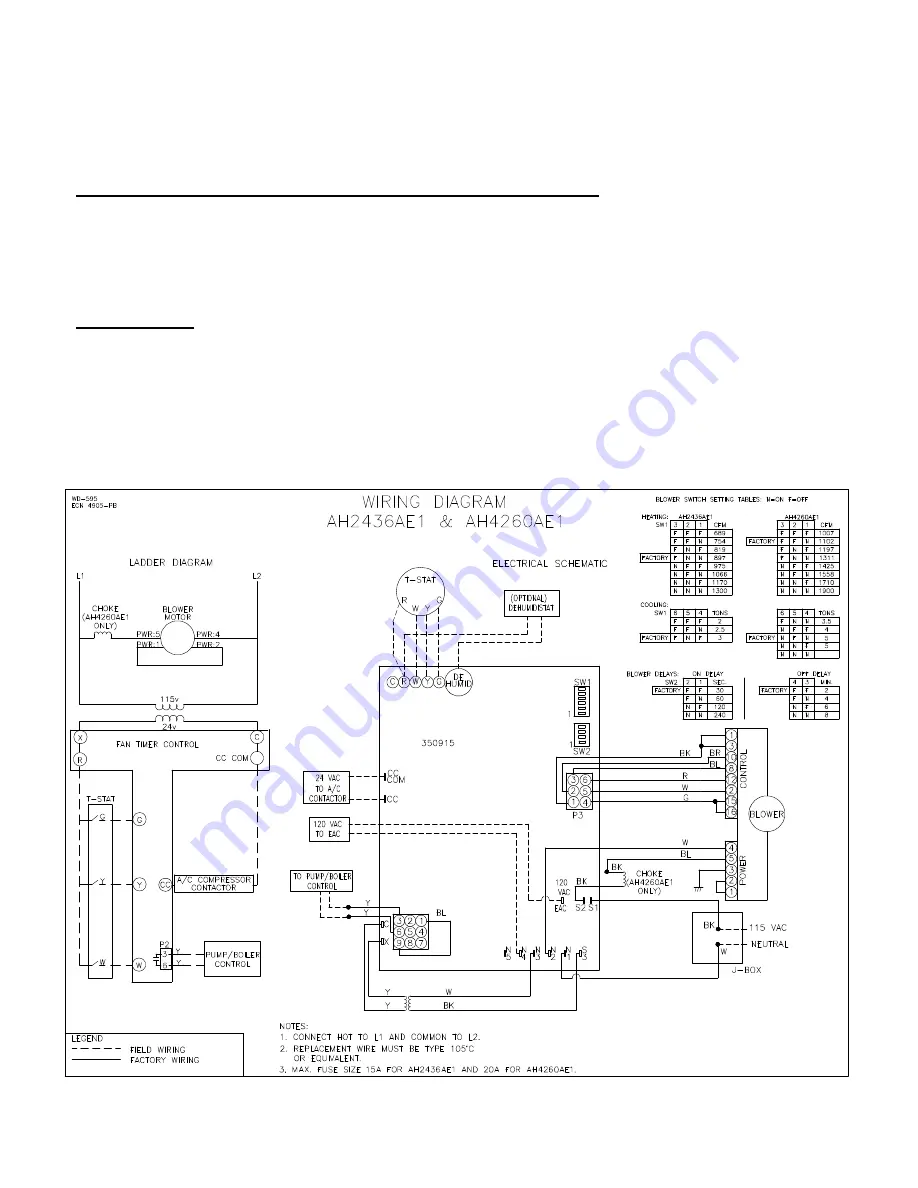
19
A liquid sub-cooling of about 10oF leaving the condenser is good over a wide range of operating
conditions for a system with a TXV in the evaporator like the AH2436A/BE1 & AH4260A/BE1.
MEASURING TEMPERATURE DROP ACROSS THE “A” COIL:
The temperature drop across the coil should be around 18oF to 23oF difference between inlet and outlet
air. This should be measured as close to the air handler as possible, to eliminate duct losses.
ELECTRICAL
All wiring must conform to the provisions of local codes or in the absence of local codes with the
provisions of the National Electrical Code, ANSI/NFPA No. 70-Latest Edition and this instruction manual.
Equivalent type wire must be used if any of the original wire supplied with the unit needs to be replaced.
NOTE:
Condensing unit is not included in above amp rating.