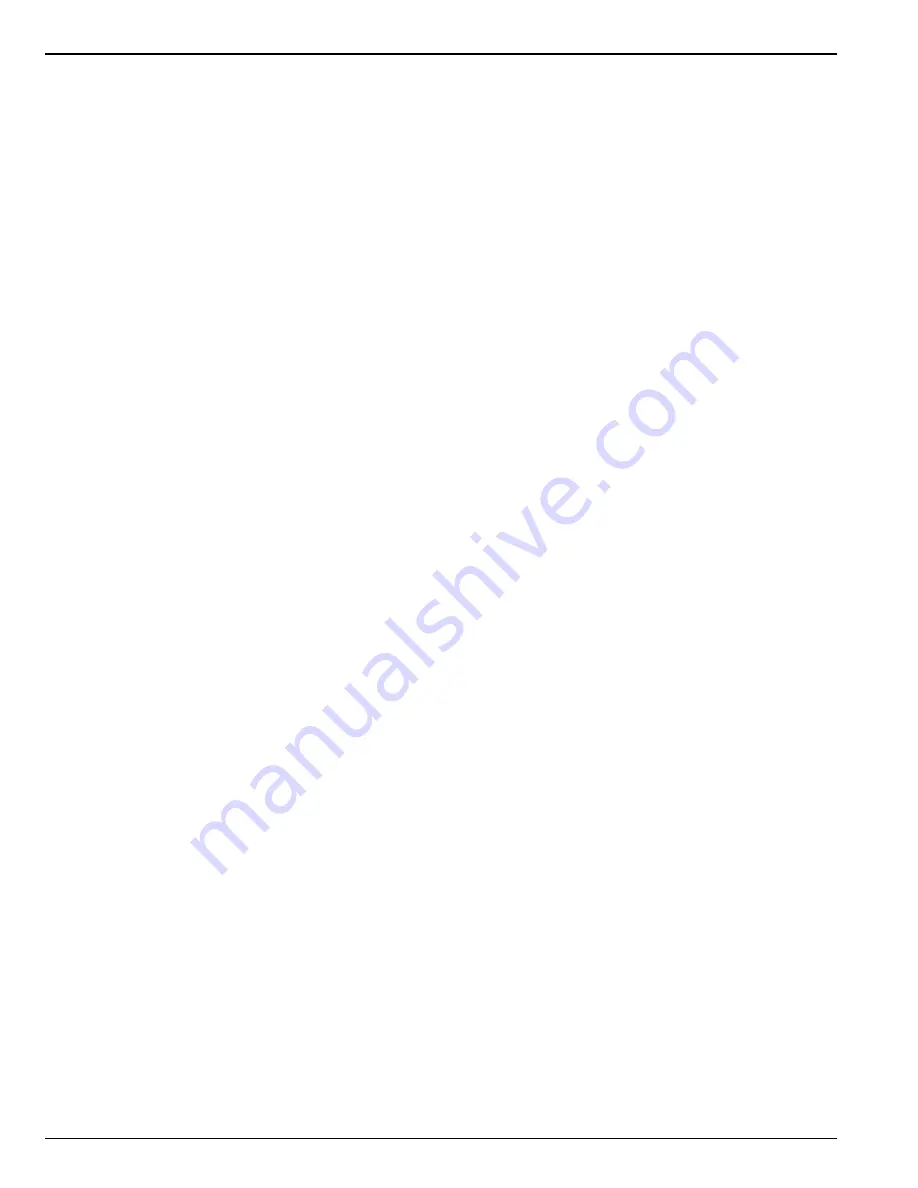
4-10
General Theory of Operation
µ
P-D Controller
CRR-20 & CRR-40, September 1999
Sensor Check
NOTE: If a Sensor Check occurs, check the supply
air sensor position in the probe holder. The supply
air sensor MUST be inserted all the way to the bot-
tom of the probe holder to accurately record the sup-
ply air temperature.
During unit operation, the controller constantly monitors the
supply and return air temperatures. If the temperature differ-
ence is outside certain limits during cooling and no alarms are
recorded, the controller performs a Sensor Check test.
“SENSR CHECK” appears in the display as the con-
troller turns all loads off except the phase contactor. “SENSR
XXX” appears in the display while the controller energizes the
high speed evaporator fan output for 5 minutes and compares
the supply and return air sensor. If the temperature difference
between the supply and return air sensor is greater than 2.2 C
(3.9 F), the controller places the unit in defrost and resets the
“SENSR XXX” display counter. When defrost is complete,
the controller repeats the sensor check test.
•
If the temperature difference between the supply and
return air sensor is less than 2.2 C (3.9 F), the controller
resumes normal operation.
•
If the temperature difference between the supply and
return air sensor is greater than 2.2 C (3.9 F) and a defrost
has occurred in the last 30 minutes, the controller attempts
to identify the defective sensor. The controller compares
the supply and return air sensor temperatures to the coil
sensor temperature:
- The controller chooses the sensor with the greatest tem-
perature difference with the coil sensor as the defective
sensor, records an alarm code and takes appropriate
action.
• If the Return Air sensor is defective and the setpoint
is -9.9 C (14.1 F) or above, the controller records
alarm code 7 and resumes normal operation.
• If the Supply Air sensor is defective and the setpoint
is -9.9 C (14.1 F) or above, the controller records
alarm code 3 and uses the return air sensor tempera-
ture plus an offset to control unit operation.
• If the Return Air sensor is defective and the setpoint
is -10.0 C (14.0 F) or below, the controller records
alarm code 7 and uses the supply air sensor temper-
ature plus an offset to control unit operation.
• If the Supply Air sensor is defective and the setpoint
is -10.0 C (14.0 F) or below, the controller records
alarm code 3 and resumes normal operation.
- If the temperature difference between both the supply
and return air sensors and the coil sensor is greater than
2.2 C (3.9 F), the controller determines both sensors are
defective, records alarm code 25 and takes appropriate
action:
• If the setpoint is -9.9 C (14.1 F) or above, a unit
shutdown occurs.
• If the setpoint is -10.0 C (14.0 F) or below, the unit
continues to operate on Cool.
Power Limit
The controller also uses current transformers to measure line
voltage as well as unit and component amperage draw.
The controller uses total unit current draw information to
provide power limit control. When the current exceeds a pre-
determined threshold, the controller limits unit power con-
sumption by sending a voltage pulse to the KVQ valve. The
KVQ valve closes to restrict the flow of refrigerant to the com-
pressor to limit the compressor drive motor current draw to the
pre-selected threshold.
Initial Unit Start-up
Power Limit is active during the compressor start-up in both
the Chill and Frozen modes, the controller partially closes the
KVQ valve to reduce the cooling capacity load on the com-
pressor. The initial power limit position of the KVQ valve is a
function of the return air temperature and ambient temperature.
If the power limit KVQ valve setting is lower than the modula-
tion cool KVQ valve setting, the Power Limit LED turns ON.
Pull-down and Normal Operation
The KVQ valve then gradually opens to increase cooling
capacity during initial pull-down. The controller then uses the
total unit current draw and the condenser coil temperature to
calculate the power limit KVQ valve setting in both the Chill
and Frozen modes. If the power limit KVQ valve setting is
lower than the modulation cool KVQ valve setting, the Power
Limit LED turns ON. The controller then sends a voltage
pulse to the KVQ valve. The KVQ valve closes to restrict the
flow of refrigerant to the compressor, thereby limiting the
compressor motor current draw to the predetermined setting.
Power Limit Management
A predetermined Power Limit can also be set from “PWRED”
feature in the Program Menu of the controller. A 10%, 20% or
30% power reduction can be selected for 8 hours of unit opera-
tion. Because the cooling capacity of the unit may be reduced
when the Power Reduction Mode is active, use of the Power
Reduction Mode should be established by the shipper.
Summary of Contents for CRR-20
Page 4: ......