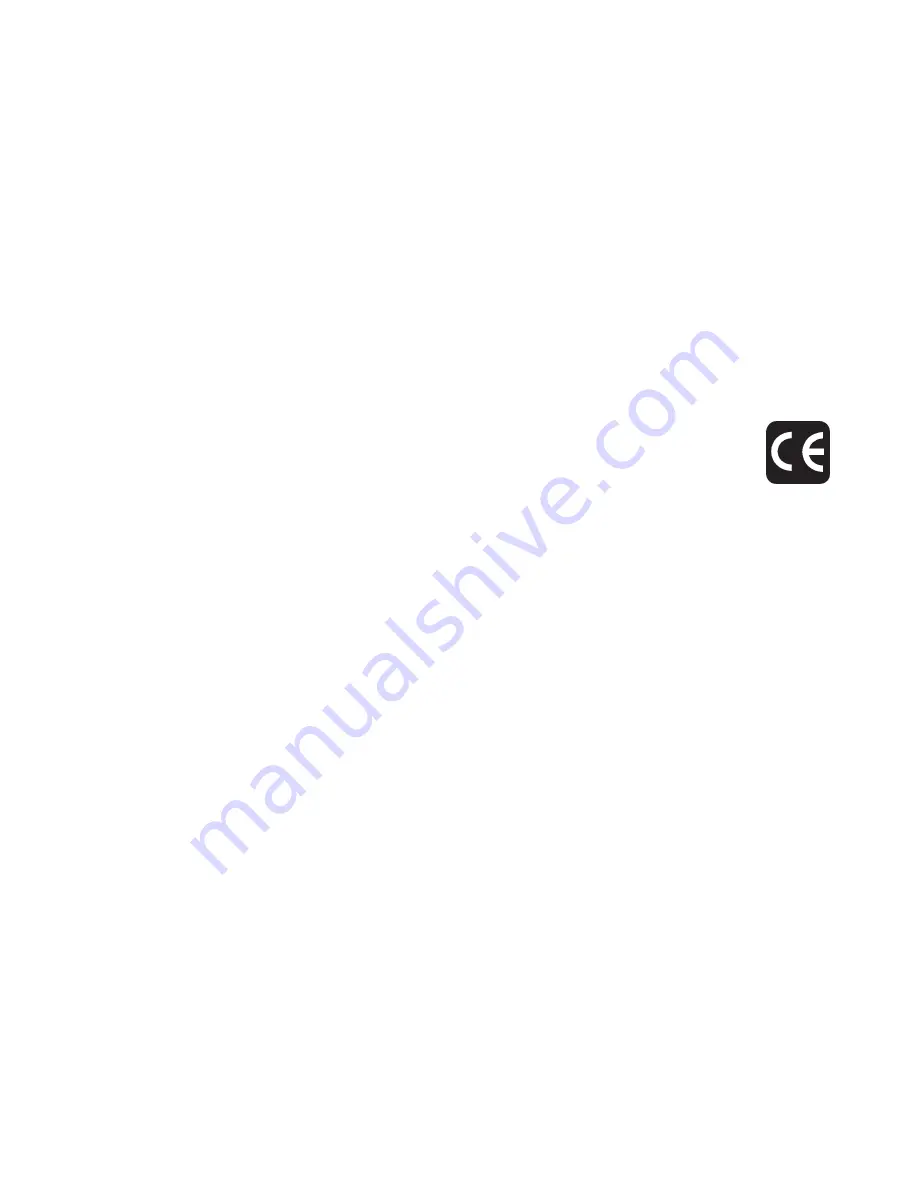
Visit our Web site at:
http://www.thermo.com/tc
http://www.thermo.com/tc
http://www.thermo.com/tc
http://www.thermo.com/tc
http://www.thermo.com/tc
Product Service Information, Applications
Notes, MSDS Forms, e-mail.
Voice Info: (800) 258-0830
NESLAB
NESLAB
NESLAB
NESLAB
NESLAB
S
S
S
S
System III
ystem III
ystem III
ystem III
ystem III
Heat Exchanger
Heat Exchanger
Heat Exchanger
Heat Exchanger
Heat Exchanger
Thermo Manual P/N U00678 Rev. 08/19/05
Installation-Operation-
Installation-Operation-
Installation-Operation-
Installation-Operation-
Installation-Operation-
Basic Service
Basic Service
Basic Service
Basic Service
Basic Service
Summary of Contents for NESLAB System III
Page 23: ... 21 TU Pump Flow Diagram Optional ...
Page 25: ... 23 Large Volume Units ...
Page 26: ...Blank page ...