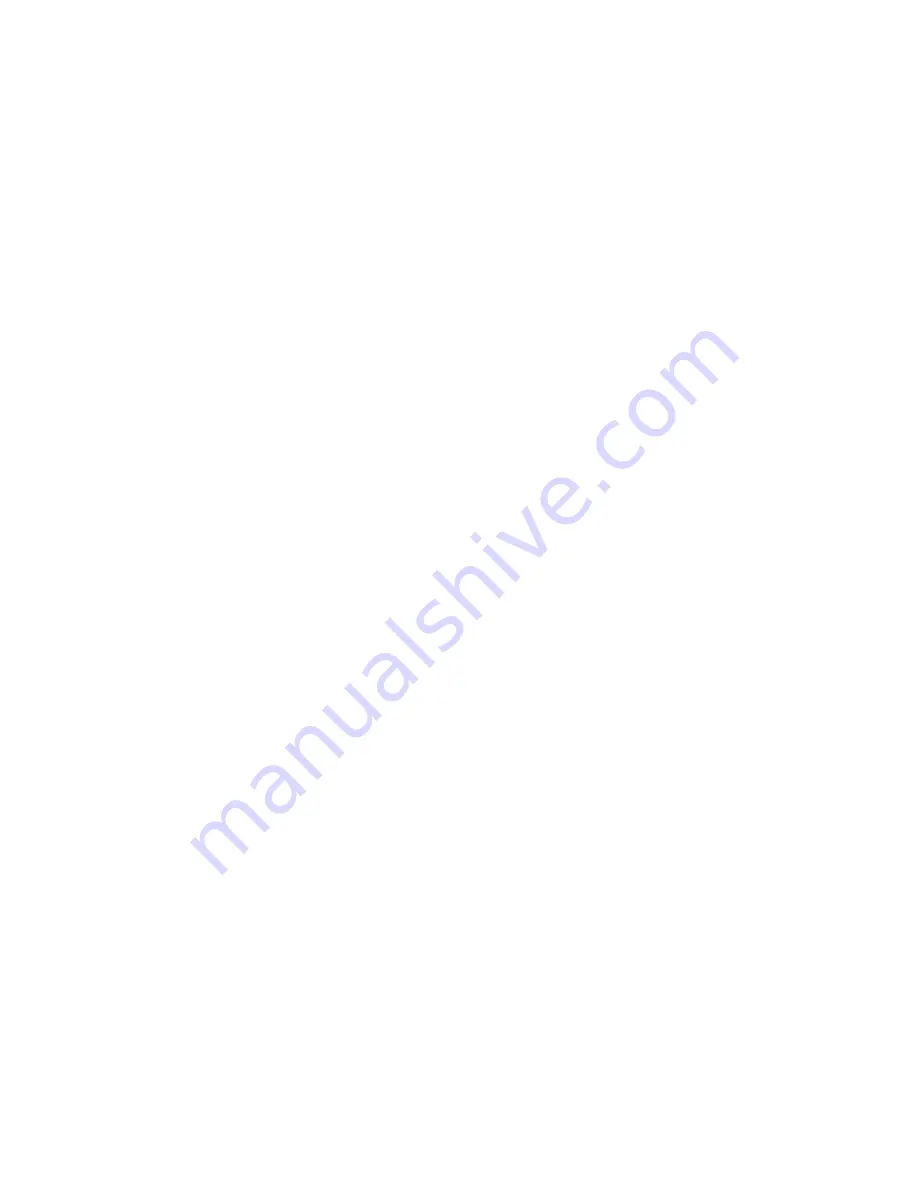
Certifications
Declaration of Conformity is available from the factory
Safety Specifications
Indoor Use Only
Altitude - up to 2,000 meters
Temperature - 5°C to 40°C
Humidity - Maximum RH 80% for temperatures up to 31°C, decreasing linearly to 50% RH at 40°C
Mains Supply Fluctuations - Mains supply voltage fluctuations not to exceed ±10% of the nominal voltage
Installation Category II
1
Pollution Degree 2
2
Class of Equipment I
____________________________________________________________________________________________________
1 Installation category (overvoltage category) defines the level of transient overvoltage which the instrument is designed to withstand safely. It
depends on the nature of the electricity supply and its overvoltage protection means. For example, in CAT II which is the category used for instru-
ments in installations supplied from a supply comparable to public mains such as hospital and research laboratories and most industrial laboratories,
the expected transient overvoltage is 2500V for a 230V supply and 1500V for a 120V supply.
2 Pollution degree describes the amount of conductive pollution present in the operating environment. Pollution degree 2 assumes that normally
only non-conductive pollution such as dust occurs with the exception of occasional conductivity caused by condensation.
Model 900 Series _____________________________________________________________________Specifications
6 -2
Summary of Contents for 900 Series
Page 1: ...900 Series Forma 86C ULT Freezer Operating and Maintenance Manual Manual No 7010902 Rev 8 ...
Page 62: ......
Page 63: ......
Page 64: ......
Page 65: ......