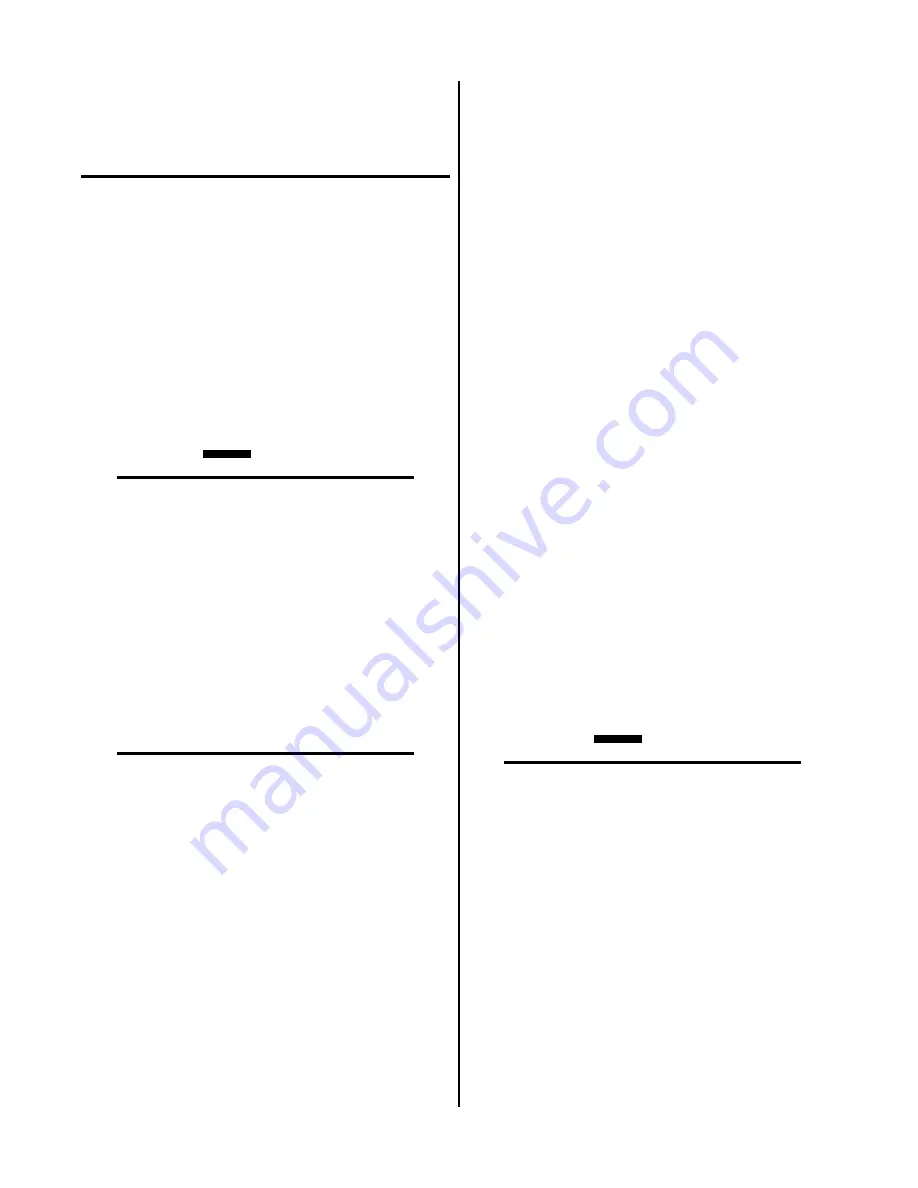
Manual 0-2729
11
SECTION 3: INSTALLATION PROCEDURES
SECTION 3:
INSTALLATION
PROCEDURES
3.01 Introduction
This section describes installation of the DRAG-GUN 38
Plasma Cutting System. These instructions apply to the
Power Supply, Torch and Leads Assemblies only; instal-
lation procedures for any Options or Accessories are given
in manuals specifically provided for those components.
3.02 Site Location
Select a clean, dry location with good ventilation and ad-
equate working space around all components.
CAUTIONS
Operation without proper air flow will inhibit
proper cooling and reduce duty cycle.
To prevent entry of cutting or other metal debris,
the power supply must not be operated in the hori-
zontal position. Operate the power supply in the
vertical position only with the handle in the up-
right position.
The power supply is cooled by air flow through the end
and side panels. Air flow must not be obstructed. Provide
at least 12 inches (300 mm) clearance on each side. Pro-
vide sufficient clearance above unit to allow access to top
panel controls (minimum 12 inches or 300 mm).
NOTE
Review the safety precautions in the front of this
manual to be sure that the location meets all safety
requirements.
3.03 Unpacking
The system is packaged with a carton and packing mate-
rial to prevent damage during shipping.
A. System Components
Included with each system is the following:
(1) Power Supply with the following installed:
• PCH-25/38 Torch and Leads (1 each)
• Work Cable with Clamp attached (1 each)
• Input Power Cable
(1) Instruction Manual
(1) Handle - including hex head bolts (4).
(1) Spare Parts Kit - includes:
• Tips (5 each)
• Electrodes (3 each)
• Gas Distributor (1 each)
B. Unpacking Procedure
1. Unpack each item and remove all packing material.
2. Locate the packing list(s) and use the list to identify
and account for each item.
3. Inspect each item for possible shipping damage. If
damage is evident, contact your distributor and/or
shipping company before proceeding with system
installation.
C. Removing Skid
The base of the power supply is secured to the skid with
lag screws. Remove the power supply from the skid per
the following procedure:
1. Remove the screws securing the base assembly of
the power supply to the skid.
2. Lift unit from skid and place in proper location.
3.04 Electrical Connection
A. Power Requirements
The unit will operate on single phase 220VAC
±10%, 50/60 Hz. The service must be fused for at
least 25 amps.
CAUTION
The primary power source, power cable, and plug
all must conform to local electrical codes and recom-
mended circuit protection and wiring requirements.
3.05 Handle Installation
1. Connect the handle to the rear panel of the power sup-
ply using four (4) hex head bolts, two on each side.
Tighten securely.
Summary of Contents for DRAG-GUN 38
Page 2: ......
Page 6: ......
Page 18: ...SECTION 3 INSTALLATION PROCEDURES 12 Manual 0 2729...
Page 24: ...SECTION 4 OPERATION 18 Manual 0 2729...
Page 50: ...SECTION 5 SERVICE 44 Manual 0 2729...
Page 58: ...APPENDICES 52 Manual 0 2699 APPENDIX II SYSYTEM SCHEMATIC A 02576...