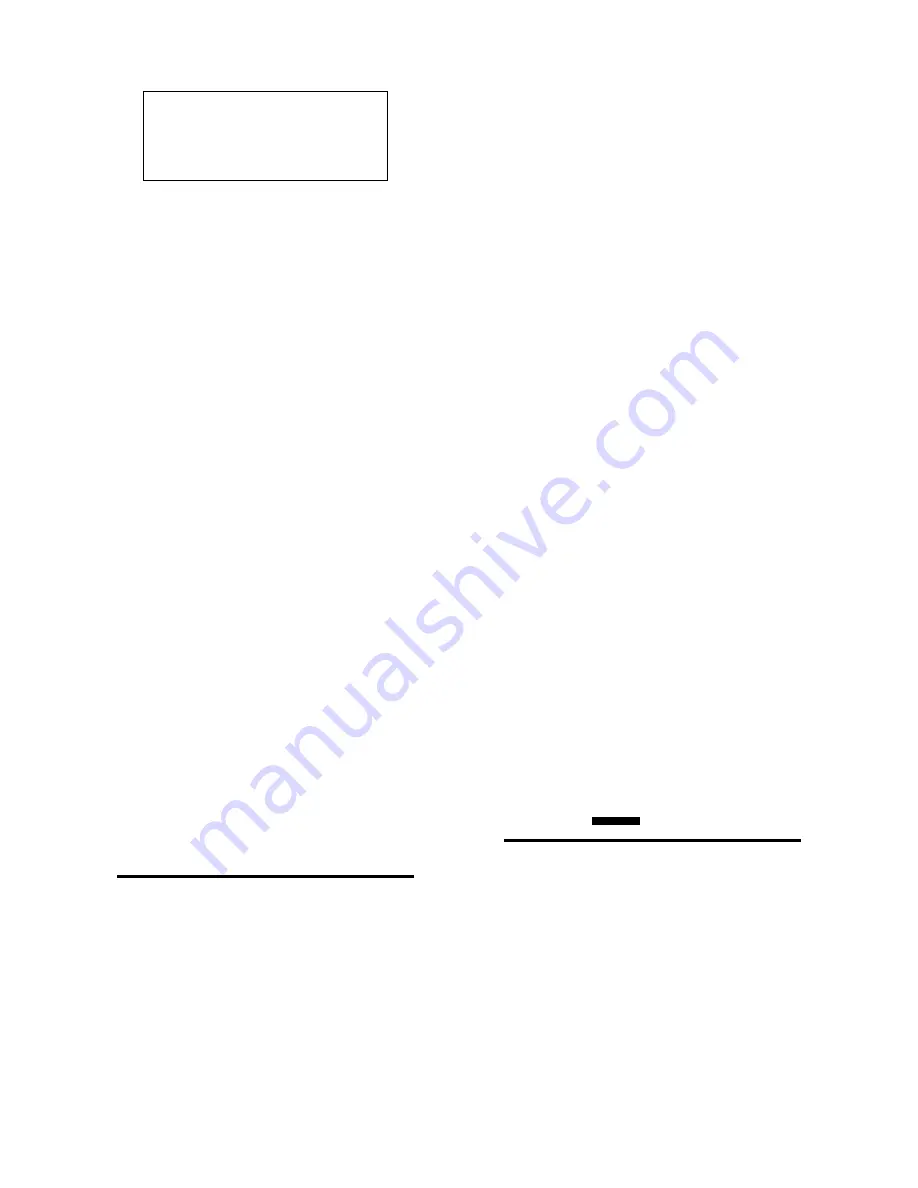
COUGAR 125 Plasma Cutter
12
Service Manual 0-2717
X. Symptom (Bold Type)
1. Cause (Italic Type)
a. Check/Remedy (Test Type)
Locate your symptom, check causes (easiest is usually
first; sometimes the order is important, if noted), then
remedies. Repair as needed being sure to verify that the
unit is fully operational after any repairs.
C. No Power, AC switch on, red (amber for
220V) indicator dark, no fan.
1. No power from wall unit.
a. Test electrical outlet with voltmeter or some
other known good load (trouble light, hand
drill, etc).
If AC line voltage is present, go to next step.
If AC line voltage is not present, replace fuse
or reset circuit breaker.
2. Damaged power cord.
a. Confirm with voltmeter if AC line voltage is
present at input to power switch.
If AC voltage is present, proceed to next step.
If AC line voltage is not present, replace power
cord.
3. Power switch faulty.
a. Confirm with voltmeter if AC line voltage is
present at main capacitor (C13) terminals when
power switch is on.
If AC line voltage is not present, replace power
switch.
D. Power OK, service circuit breaker or
fuse opens after the power switch is
switched on.
NOTE
Proceed with troubleshooting for these components
in order:
1. Faulty Fan.
a. Disconnect the Fan and insulate each of the two
wires going to the Fan with tape, then reapply
power.
If the circuit breaker or fuse opens after the
power switch is switched on, go to next step.
If the circuit breaker or fuse is okay, replace
Fan.
2. Faulty Transformer Assembly or Capacitor.
a. With the Fan still disconnected, disconnect two
leads from the Transformer that are connected
to the Capacitor (C13), then apply power.
If the circuit breaker or fuse opens after power
is applied, the Capacitor is shorted. Replace
Capacitor (C13).
If the circuit breaker or fuse is okay, replace
Transformer.
E. Power OK, fan runs, no air flow
operation or pilot when torch switch
pressed.
1. Air supply not connected or turned on.
a. Connect air supply or turn it on.
2. Shield cup loose, PIP not making contact.
a. Reseat the torch parts, tighten shield cup.
3. Unit overtemp.
a. Leave power on so fan can cool unit, test again
after 10 min.
4. Shorted torch parts.
a. Replace torch consumables.
5. Torch switch may have broken or shorted wires.
a. Refer to subsection 3.6, Torch and Leads Trouble-
shooting.
6. Shorted Bridge Rectifier (BR2)
a. If the Rectifier (upper) is hot and the Transformer
is buzzing or heating up, the rectifier is shorted.
Replace Rectifier.
7 . Faulty Control PCB or Relay
CAUTION
Be sure torch is directed away from people or haz-
ards. A pilot arc may start!
a. Push the test button on the side of the Relay. If
the Solenoid opens and the torch operates, the
PCB or Relay has most likely failed.
The PCB can be isolated by removing the push
on connectors from the Relay coil and measur-
ing the relay coil with an ohmmeter. If the coil
measures between 50 - 100ohms, the Relay is
good and the PCB should be replaced.