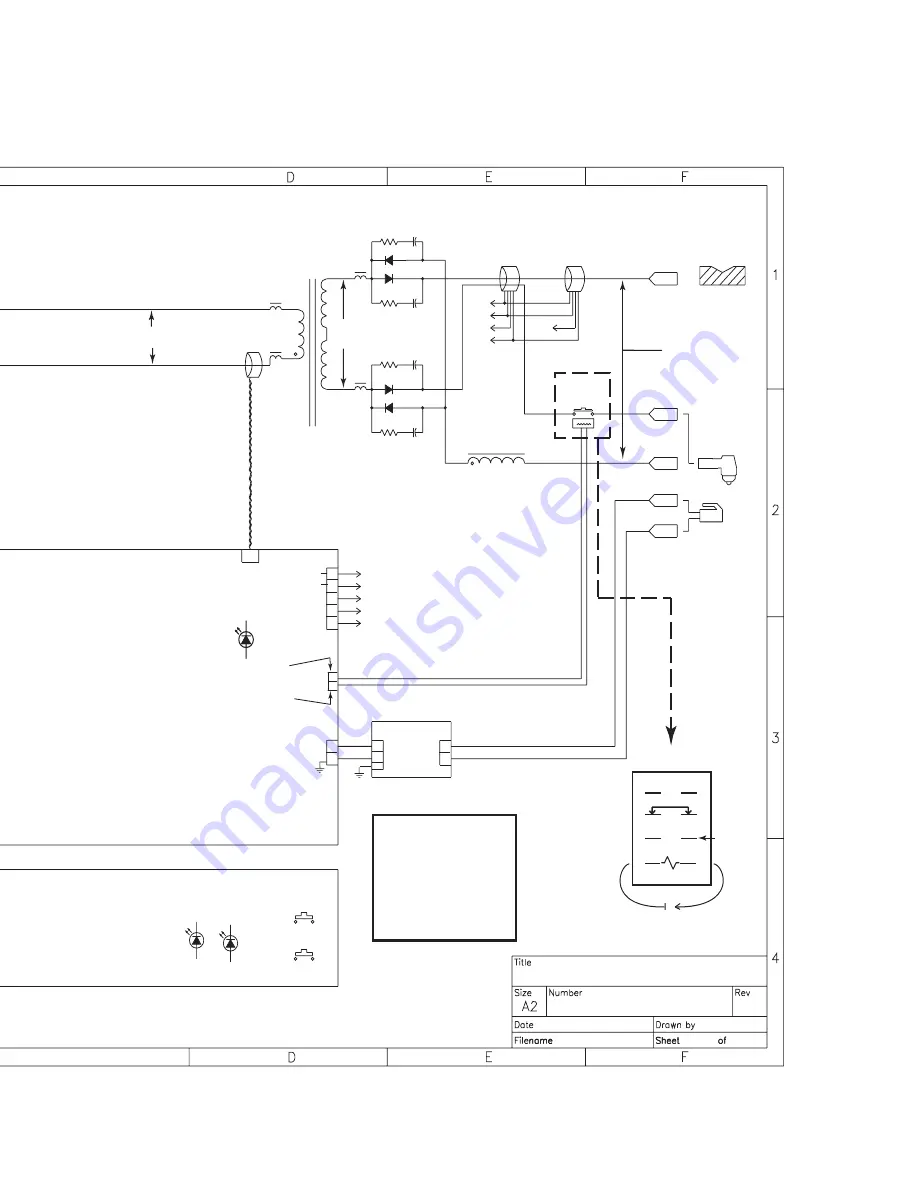
Manual 0-4697
A-5
APPENDIX
A
HOLD
HOLD
CN9
OU_1
VD_1
OU_2
S/W
S/W
TORCH
WORK
AIR
ERROR
AIR
CHECK
C5
C4
C3
REACTOR
GN_1
VC_1
PILOT
C6
CN3
GN_1
VD_1
VC_1
Current Sensor
CN10
OU_1
VC_2
Pilot
Relay
R4
R3
R2
C/T 1
R5
2005 / 01 / 12
POWWEL ELECTRONIC IND.CO., LTD.
Air Plasma 20A
Main Transformer
Art # A-05555
LD2
Enable
14VDC
1
2
O.C.V.
Ω
Jumper
Pilot
To Current
Sensor
77
Y
Y
PCR
10.3 MF
630V
239VAC at 115VAC input
210VAC at 220VAC input
207VAC at 115VAC input
182VAC at 220VAC input
335VAC at 115VAC input
291VAC at 220VAC input
Pilot 90
Cutting 110
(Power Supply)
NOTE:
Do Not attempt to
adjust the POTs!
CN12
1
2
+20VDC
to engage
Pilot Relay
-12VDC
+12VDC
W
W
W
W
Y
G
Y
Y
1
R
O
BR
2
3
4
5
W
W
Summary of Contents for C-20A Cutskill
Page 2: ......
Page 4: ......
Page 6: ......
Page 14: ...Installation 3 2 Manual 0 4697 This Page Left Blank ...
Page 18: ...Operation 4 4 Manual 0 4697 This Page Left Blank ...
Page 33: ...Manual 0 4697 7 5 Parts List 5 6 3 4 2 7 7 A 07060 1 8 ...
Page 34: ...Parts List 7 6 Maual 0 4697 This Page Left Blank ...
Page 40: ...APPENDIX A 6 Manual 0 4697 This Page Left Blank ...