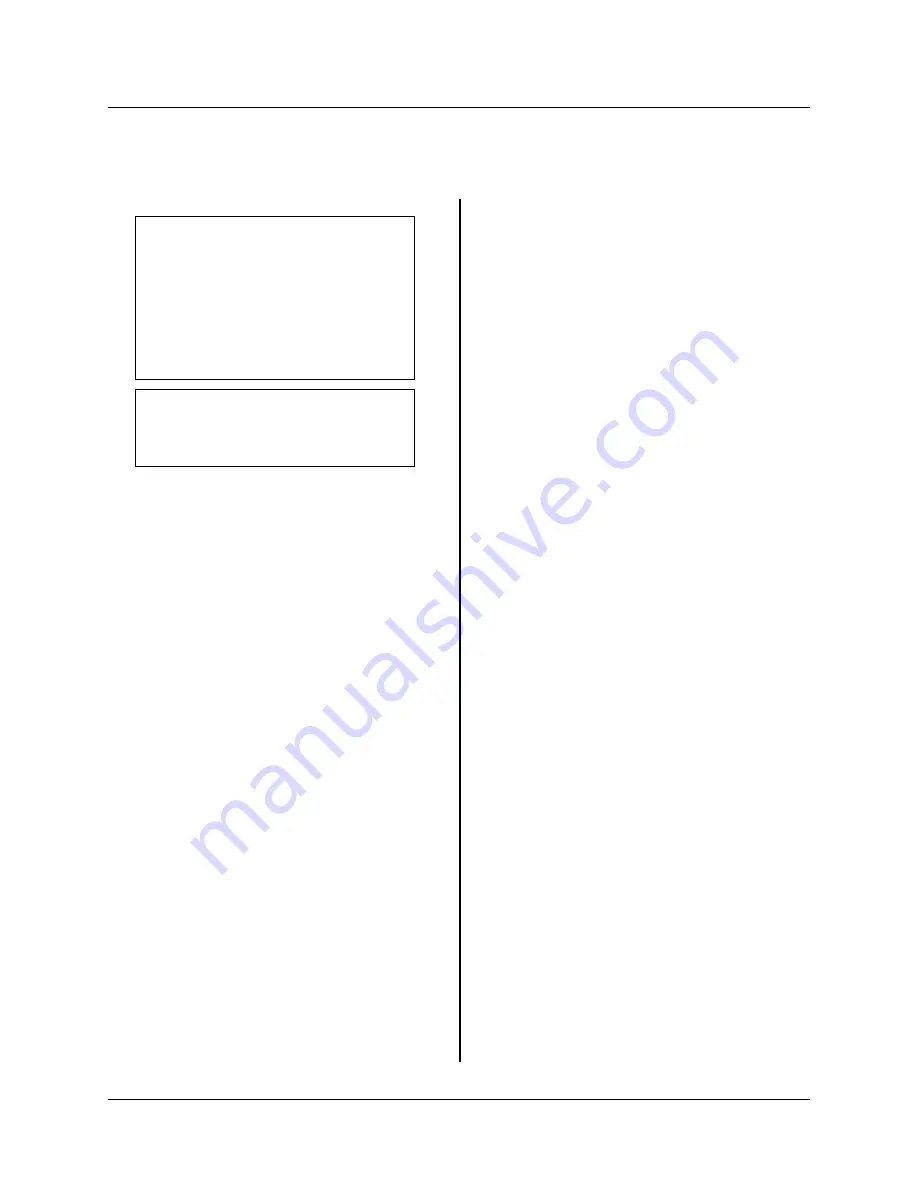
TROUBLESHOOTING
W A R N I N G : D i s c o n n e c t th e
power source from the input
power source before carrying
out any service or repair work.
Hazardous voltages can be pre-
sent in the machine whenever
input power is connected.
W A R N I N G :
A L L
S E R V I C E
SHOULD BE PERFORMED BY
TRAINED PERSONNEL ONLY.
General
1. Safety Practices, Precautions,
and Warnings.
Caution should be used when troubleshooting and
working inside inverter power supplies. Many cir-
cuits inside the machine handle high voltages or
currents. Some circuits will retain their charge for
several seconds after power to the machine has
been turned off. Before touching, diagnosing, or
servicing the machine or its subsystems, measure
the circuit in question for decaying voltage levels.
Do not touch, service, or attempt to diagnose any
part of the machine unless you are certain of the
function of the circuit and the voltage level present
in the circuit.
During certain machine failures, abnormally high
voltage levels may be present in circuits that usually
contain low voltage levels. Check the voltage level
in the circuit before touching or servicing the circuit.
2. Wiring.
Prior to disassembly or servicing of the machine,
note the wiring and connections in the machine.
Reassembling should place the wires in the same
location and routing as received from the factory.
Keep wires and leads away from hot parts and sharp
edges. Keep the primary side of the machine (input
power side) away from the secondary side (welding
and control circuits).
Examine connections for proper assembly and
contact. Lugs should be in tight contact with the
lead’s conductor and should be crimped to the
lead’s insulation. The mating surfaces of the con-
nection should be clean and free of oxidation or
debris.
Do not pull on leads or cables to disassemble
connections. Firmly grasp each lug or connector.
Use appropriate tools to enhance leverage if
needed. Pulling on leads and cables for disassem-
bly can damage the integrity of the connection and
cause future malfunctions.
3. PC Board Handling and Checking.
Most of the PC boards in the machine contain
static sensitive components. Use a grounding strap
or other suitable grounding means before attempt-
ing to service PC boards. When a PC board is
removed from the machine, it should be immedi-
ately placed on a grounded anti-static mat for ex-
amination or placed in an anti-static bag for
transportation or further handling.
Before replacing a suspect PC board, disconnect
all wires and cables from the board. Firmly recon-
nect the board and retest the machine to determine
if the problem persists. Faulty connections or wiring
problems are often the source of poor PC board
performance.
If a PC board replacement has appeared to correct
a problem, the machine should be retested with the
old PC board to recreate the problem. If the original
symptoms reappear, then the original PC board
created the problem. If the original symptoms do
not reappear, then it is likely that the wiring or
connections were the source of the problem and
these, or other sources, should be examined to
insure that the problem doesn’t reappear later.
4. Optional Equipment or
Accessories.
Disconnect any optional or compatible equipment
to verify that the power source is creating the prob-
lem. Disconnect any wire feeders from the machine
and trigger the power source on from the back
Amphenol or use the SMAW mode to verify proper
power source triggering.
Disconnect optional
equipment or accessories to determine if they are
placing excessive demands on the power source’s
auxiliary supplies.
430429-465
TROUBLESHOOTING
February 28, 2000
7-1
Summary of Contents for ULTRA FLEX 350
Page 4: ...This page intentionally left blank 430429 465 INTRODUCTION 1 2 February 28 2000...
Page 15: ...Figure 3 2 Volt Ampere Curves 430429 465 DESCRIPTION OF EQUIPMENT February 28 2000 3 3...
Page 22: ...This page intentionally left blank 430429 465 INSTALLATION 4 4 February 28 2000...
Page 34: ...This page intentionally left blank 430429 465 OPERATION 5 12 February 28 2000...
Page 36: ...This page intentionally left blank 430429 465 MAINTENANCE 6 2 February 28 2000...
Page 40: ...This page intentionally left blank 430429 465 TROUBLESHOOTING 7 4 February 28 2000...
Page 42: ...Figure 8 1 Ultra Flex Welder Assembly 430429 465 PARTS LIST 8 2 February 28 2000...
Page 44: ...Figure 8 2 430429 465 PARTS LIST 8 4 February 28 2000...
Page 46: ...This page intentionally left blank 430429 465 PARTS LIST 8 6 February 28 2000...
Page 47: ......
Page 48: ......
Page 49: ......