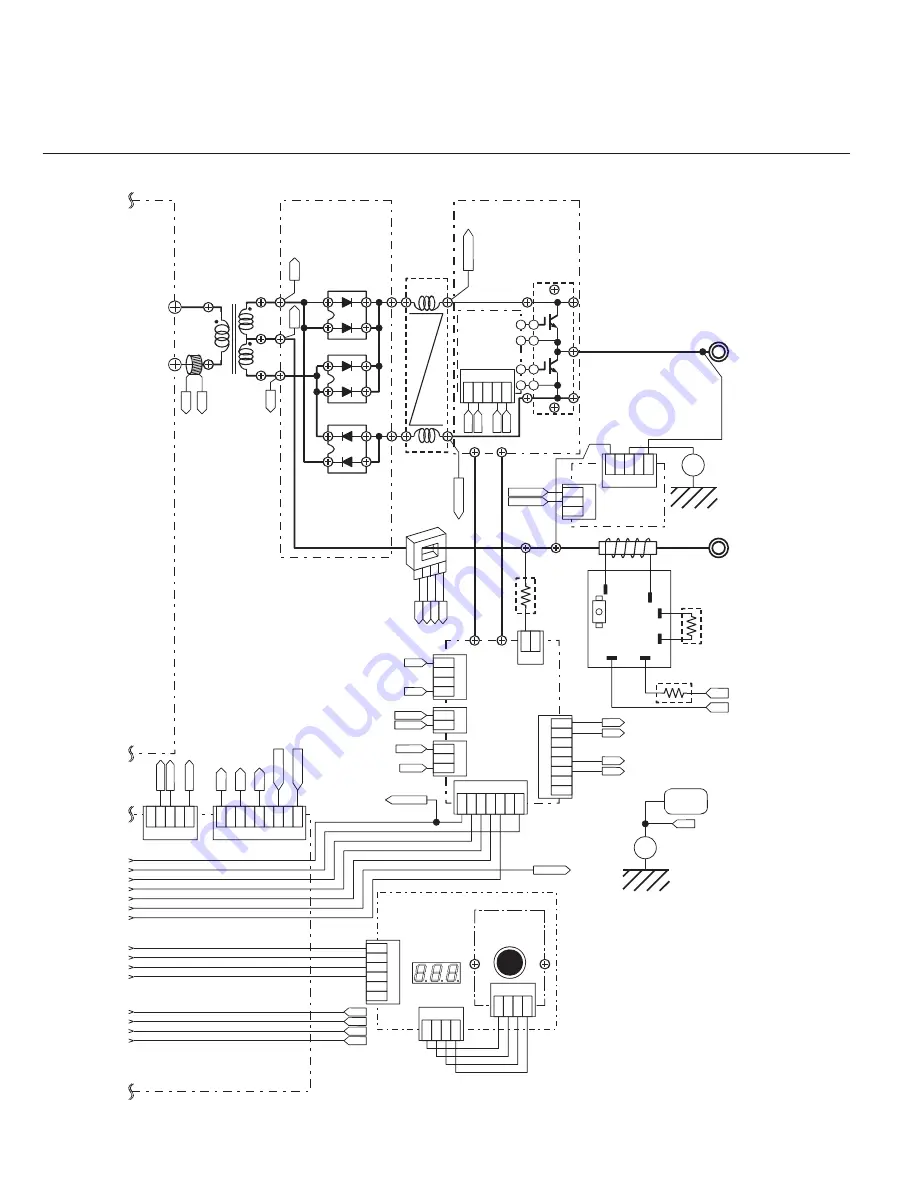
185ACDC / 200ACDC INTERCONNECT DIAGRAM
A10
TB7
TB12
TB21
TB22
TB20
CT2
-Output
Terminal
TO2
PCB12
DIODE Snubber
Circuit Board
[WK-5615]
PCB10
Panel
Circuit Board
[WK-5527]
PCB11
Board
Encoder
[WK-5528]
1 2 3 4
1
2
CN2
3
4
5
6
CN1
1 2 3 4
CN1
-15
+15
IS
GND
EB
AC2
A
C1
AC4
AC2
SH.DET-
SH.DET+
SH.DET-
SIDE CHASSIS 2
FRONT
PANEL
EA
Ground
+
D5
D2
CT2
CT1
CN9
1 2 3 4 5 6 7 8 9
CN8
1 2 3 4 5
HF.UNIT1
CC2
CC1
R1
R2
AC1
AC3
CC1
AC1
AC3
R2
R6
TB1
TB2
CN1
1
2
3
4
P
N
CN2
1
2
P+21V
PGND
CN3
1
2
3
S+15V
SG
CN4
1 2 3 4 5 6 7
1
2
CN6
3
4
5
6
7
8
G7
E7
G8
E8
/RY_ON
R3
PCB13
Super Inpose
Circuit Board
[WK-5569]
HCT1
+Output
Terminal
TO1
FCH1
PCB15
IGBT Gate
Circuit Board
[WK-3367]
G1
E1
E2
G2
G1
E1
G2
E2
PCB14
IGBT Snubber
Circuit Board
[WK-5570]
TB1
TB2
SH.DET+
CN1
1 2 3 4 5
G7
E7
G8
E8
Q13
PCB16
Filter Circuit
Board
[WK-5499]
CN1
1 2 3 4 5
/RY_ON
RY+15V
SIDE CHASSIS 3
CN3
1
2
3
Ground
+
1 2
CN5
D4
AC3
SG
S+15V
RY+15V
AC4
T1
1 2
3 4
-15
+15
IS
GND
Summary of Contents for 185 AC
Page 2: ......
Page 20: ...2 6 May 22 2006 ARCMASTER 185 ACDC 200 ACDC...
Page 26: ...3 6 May 22 2006 ARCMASTER 185 ACDC 200 ACDC...
Page 34: ...5 2 May 22 2006 ARCMASTER 185 ACDC 200 ACDC...
Page 50: ...9 4 May 22 2006 ARCMASTER 185 ACDC 200 ACDC...
Page 105: ......
Page 117: ......
Page 120: ......