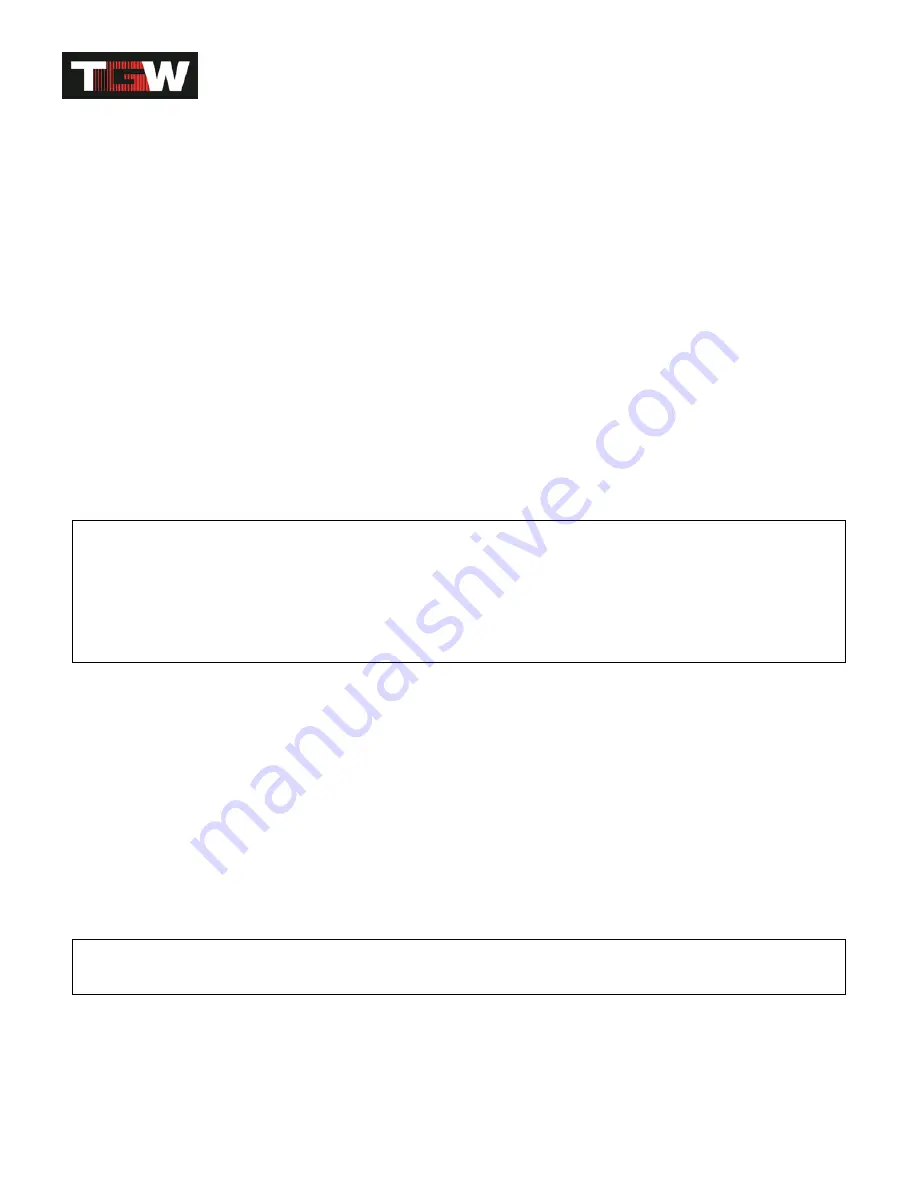
NBS IOM
30
Preventive Maintenance
GENERAL
The key to ensuring the expected return on investment is to protect against premature failure with a well-planned
program of preventive maintenance.
Preventive maintenance programs examine what may fail and then formulate action plans which will prevent
failure or downtime. This kind of maintenance includes lubrication and replacement or repair of parts before
failure but after expected life has been attained.
Preventive maintenance will save expensive downtime and wasted energy. It will increase the life of components.
Along with preventive maintenance, there should be a record-keeping system. You must know what problems
you have had in the past and when different components were serviced.
A visual and audible inspection should be taken every day. You can see if a chain is loose, oil leaking, sprocket
worn; or you can hear a faulty bearing, noisy chain or any other noise that might indicate a problem. When
something major goes wrong with some component, records should be kept to see if a pattern to the problem
occurs.
All personnel working in close proximity to the conveyor should inform maintenance or their supervisor of any
unusual noise.
WARNING
Do not perform maintenance on the conveyor until the startup controls are locked out and cannot be turned on by
any person other than the one performing the maintenance. If more than one member of a crew is working on the
conveyor, EACH CREW MEMBER MUST HAVE A LOCK ON THE POWER LOCK OUT. The air pressure must
be turned off to the work area. All pneumatic devices must be de-energized to prevent accidental cycling of the
device.
Make sure personnel are clear of all conveyor equipment before restarting the system.
GEARMOTOR
The drive unit should be checked monthly. Check the gearmotor for leaking seals. Check the gearcase for proper
oil level and add the approved oil for your particular unit. Check for overheating, vibrations and dirt buildup.
Each Nord gearmotor is supplied from the factory with the correct grade and quantity of lubricant for the specified
mounting position. Under special circumstances such as high or low ambient temperatures optional oils should
be used.
CHAINS AND SPROCKETS
Chains and sprockets should be checked monthly. Look for correct alignment. In time, set screws may loosen
and allow the sprockets to become misaligned. Use a straight edge held parallel to both sprockets to check
alignment. Shift one of the sprockets if the straight edge shows it is necessary.
WARNING
REPLACE ANY CHAIN GUARD REMOVED in order to adjust, check or lubricate chain and sprockets. Guards
are furnished and installed to prevent personal injury during operation; maintain them on the unit.
Keep the chain clean and lubricated. Chains may be cleaned by wiping with a rag soaked in nonflammable
cleaning solvent.
Lubrication of roller chains is essential to effectively minimize metal-to-metal bearing contact of pin-bushing joints
of the chain. Oil should be applied to outside plate and inside plate edges, since access to pin-bushing area is
90480005rev010614
Summary of Contents for NBS 30 Series
Page 7: ...NBS IOM 7 90480005rev010614 ...
Page 40: ...NBS IOM 40 Parts Identification NBS 90 Transfer 90480005rev010614 ...
Page 47: ...NBS IOM 47 Parts Identification NBS Drive 5 Bed 90480005rev010614 ...
Page 51: ...NBS IOM 51 Parts Identification NBS Take up 5 Bed 90480005rev010614 ...
Page 55: ...NBS IOM 55 Parts Identification NBS 30 3R Diverter Assembly 90480005rev010614 ...