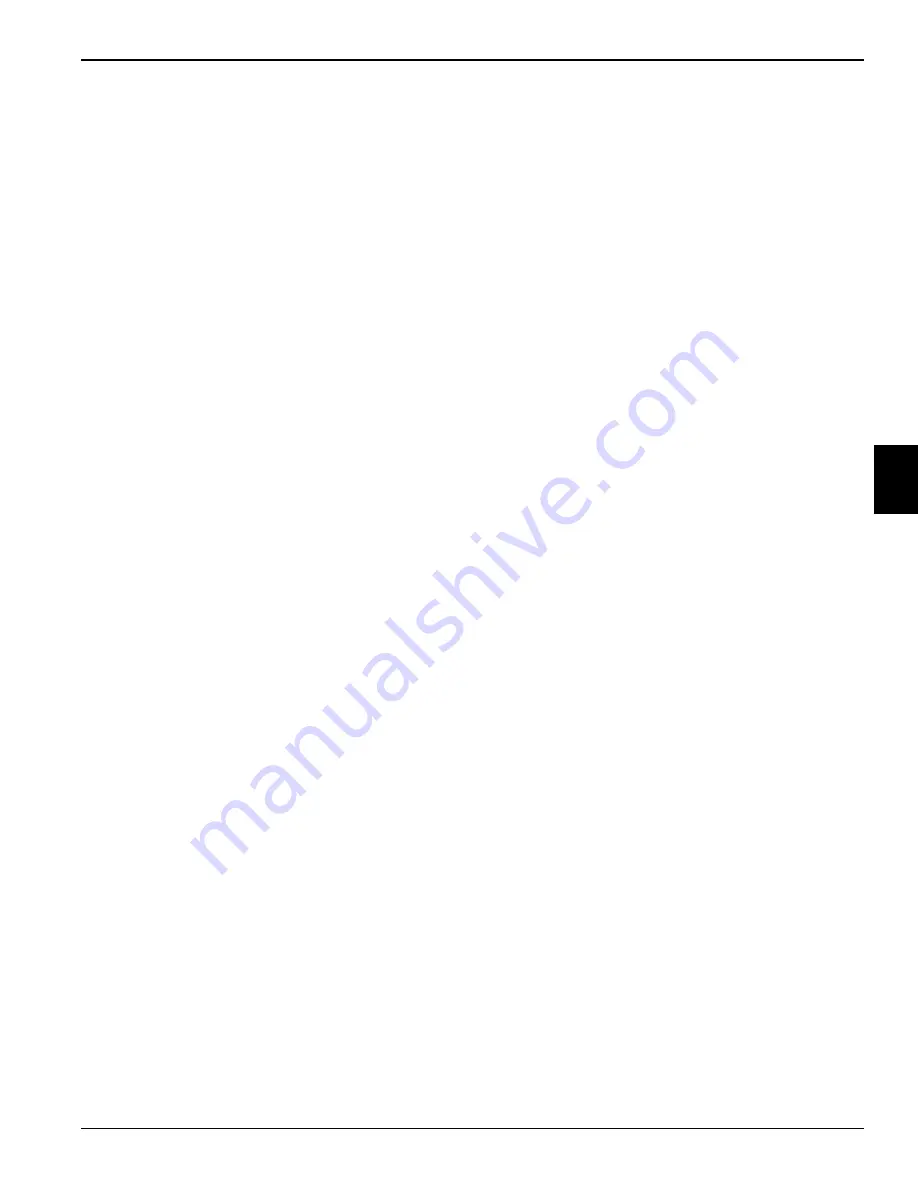
ELECTRICAL
673831-Rev A
4-29
4
Mow/Backlap Circuit—Theory of
Operation
Unswitched Power Circuit
Unswitched power is available from the battery positive
terminal to the 3-way distribution block.
Unswitched power is available from the 3-way distribution
block to the following:
• 30-amp fuse (F3)
• 15-amp fuse (F4)
• 20-amp fuse (F6)
• 20-amp fuse (F7)
Unswitched power is available from 30-amp fuse (F3)
output terminal to the ignition relay (K1) terminal 30.
Unswitched power is available from 15-amp fuse (F4)
output terminal to the following components:
• Ignition switch terminal 6
• LDU Display terminal 1-01
Unswitched power is available from 20-amp fuse (F6)
output terminal to the MCU (U1) terminals 6-06 and 6-07.
Unswitched power is available from 20-amp fuse (F7)
output terminal to the MCU (U1) terminals 1-01 and 1-01.
Switched Power Circuit (Green)
When the key switch (SW1) is turned to the run position,
voltage is provided from key switch terminal 4 to ignition
relay (K1) terminal
8
6, energizing the relay and to MCU
(U1) terminal 1-02.
With the ignition relay (K1) energized, switched power is
provided from ignition relay terminal
8
7 to the following
components:
• Mow Switch (SW2) terminal 2
• Lift proximity switch (SW
8
) terminal 1
• LDU display terminal 1-03
With switched power provided to the MCU, the MCU will
energize.
With switched power provided to the LDU, the LDU
display will energize and will display vehicle status.
Interlock Circuit
The operator must be on the seat before moving the
parking brake switch to the off position or placing the
mow switch in the on position. (See “Run Circuit—Theory
of Operation” on page 4-21.)
Mow Circuit
When the mow switch (SW2) is placed in the on position,
voltage is provided from terminal 3 to the following:
• Mow speed switch (SW12) terminal 1
• Mow switch terminal
8
, the LED will turn ON
When the mow speed lever is placed in the MOW
position, the mow speed proximity switch (SW12) is
activated. With the switch activated, voltage is provided
to MCU terminal 4-09.
When the reels are lowered, the center lift arm is brought
near the magnetic target zone of the lift proximity switch
(SW
8
), activating the switch. With the switch activated,
voltage is provided from the proximity switch to MCU (U1)
terminal 4-02. With the signal detected at terminal 4-02,
the MCU will provide power from terminal 5-02 to the
front (SOL1) and rear (SOL2) mow solenoids, energizing
the solenoids. With the solenoids energized, the cutting
units will rotate in the forward direction.
Note: The mow speed and lift proximity switches are solid
state switches and will have approximately a 2 to 3 volt
drop across the switch when activated.
Backlap Circuit
The backlap circuit is activated using the menus on the
LDU. Backlap operation is communicated to the MCU by
the CAN circuit.
Start the engine and activate the backlap through the
LDU. Move the mow switch (SW2) to the on position,
voltage is provided from terminal 3 to the following:
• Mow speed switch (SW12) terminal 1
• Mow switch terminal
8
, the LED will turn ON
When the mow speed lever is placed in the MOW
position, the mow speed proximity switch is activated.
With the switch activated, voltage is provided to MCU
terminal 4-09.
When the reels are lowered, the center lift arm is brought
near the magnetic target zone of the lift proximity switch
(SW
8
), activating the switch. With the switch activated,
voltage is provided from the proximity switch to MCU (U1)
terminal 4-02. With the signal detected at terminal 4-02,
the MCU will provide power from terminal 6-03 to the
front (SOL3) and rear (SOL4) backlap solenoids,
energizing the solenoids. With the solenoids energized,
the cutting units will rotate in the reverse direction.
Note: The mow speed and lift proximity switches are solid
state switches and will have approximately a 2 to 3 volt
drop across the switch when activated.
Summary of Contents for Jacobsen SLF530
Page 2: ......
Page 6: ......
Page 9: ...SAFETY 673831 Rev A 1 3 1 Figure 1 1 MAR0230 1 2 2 3 4 5 6 7 8 9 10 10 10 11 12 13 14 15 ...
Page 44: ...3 18 673831 Rev A ENGINE 3 Page Intentionally Blank ...
Page 60: ...4 16 673831 Rev A ELECTRICAL 4 Page Intentionally Blank ...
Page 64: ...4 20 673831 Rev A ELECTRICAL 4 Page Intentionally Blank ...
Page 72: ...4 28 673831 Rev A ELECTRICAL 4 Page Intentionally Blank ...
Page 76: ...4 32 673831 Rev A ELECTRICAL 4 Page Intentionally Blank ...
Page 80: ...4 36 673831 Rev A ELECTRICAL 4 Page Intentionally Blank ...
Page 84: ...4 40 673831 Rev A ELECTRICAL 4 Page Intentionally Blank ...
Page 126: ...4 82 673831 Rev A ELECTRICAL 4 Page Intentionally Blank ...
Page 239: ...HYDRAULICS 673831 Rev A 6 45 6 Page Intentionally Blank ...
Page 258: ...6 64 673831 Rev A HYDRAULICS 6 Page Intentionally Blank ...
Page 286: ...7 28 673831 Rev A STEERING 7 Page Intentionally Blank ...
Page 350: ...IX IX 12 673831 Rev A INDEX ...
Page 351: ......