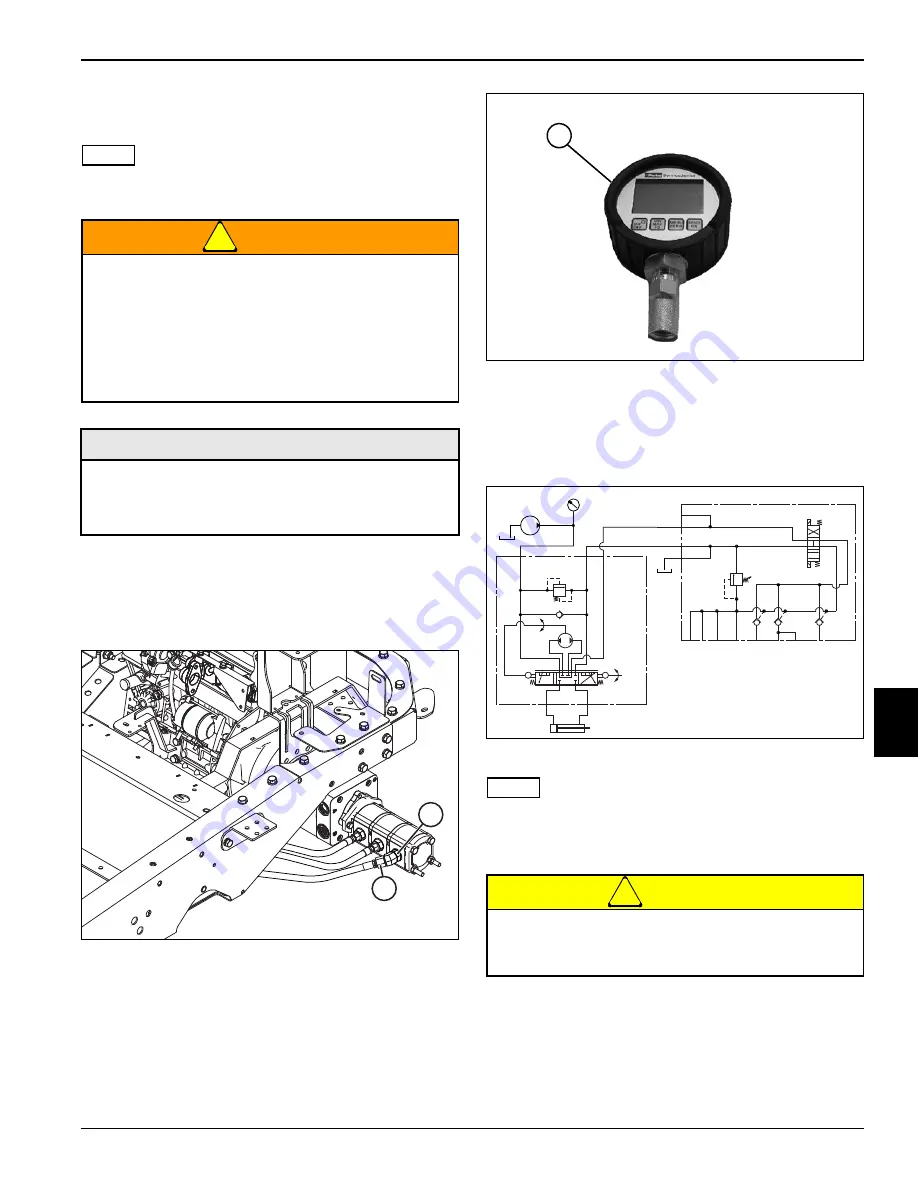
STEERING
673831-Rev A
7-5
7
Steering Relief Valve Pressure Test
NOTE
Before performing this test, perform field test procedures.
(See “Field Test Procedures” on page 6-23.)
WARNING
1.
Operate hydraulic system until oil temperature is
120–150° F (49–65° C).
2.
Park the mower safely. (See “Park Mower Safely” on
page 1-6.)
Figure 7-4
3.
Disconnect hose (2) from fitting (1).
4.
Assemble test tee fitting to fitting (1).
5.
Secure hose (2) to test tee fitting.
Figure 7-5
6.
Connect test hose and pressure gauge (3) to test tee
fitting.
7.
Bypass seat switch and engage park brake (park
brake switch in the on position).
Figure 7-6: Steering Relief Valve Pressure Test
NOTE
Verify engine rpm is within specification (3000 rpm
±
50)
to ensure accurate hydraulic test results.
8
.
Start engine and run at full throttle (3000 rpm ± 50).
CAUTION
9.
Turn the steering wheel fully right against stop.
10. Record pressure reading.
The hydraulic system is under pressure, and the
oil will be hot.
• Always relieve pressure in the hydraulic
system before performing service.
• Failure to follow appropriate safety
precautions may result in death or serious
injury.
Required Tools and Materials
• Pressure Gauge 4000 psi (276 bar)
• -6 ORFS Test Hose 4000 psi (276 bar)
• -6 ORFS Tee Fitting
2
1
MAR0175
Do not run lift/steering relief valve over relief
longer than 10 seconds, or damage may occur to
hydraulic system components.
TN1275
3
MAR0176
Summary of Contents for Jacobsen SLF530
Page 2: ......
Page 6: ......
Page 9: ...SAFETY 673831 Rev A 1 3 1 Figure 1 1 MAR0230 1 2 2 3 4 5 6 7 8 9 10 10 10 11 12 13 14 15 ...
Page 44: ...3 18 673831 Rev A ENGINE 3 Page Intentionally Blank ...
Page 60: ...4 16 673831 Rev A ELECTRICAL 4 Page Intentionally Blank ...
Page 64: ...4 20 673831 Rev A ELECTRICAL 4 Page Intentionally Blank ...
Page 72: ...4 28 673831 Rev A ELECTRICAL 4 Page Intentionally Blank ...
Page 76: ...4 32 673831 Rev A ELECTRICAL 4 Page Intentionally Blank ...
Page 80: ...4 36 673831 Rev A ELECTRICAL 4 Page Intentionally Blank ...
Page 84: ...4 40 673831 Rev A ELECTRICAL 4 Page Intentionally Blank ...
Page 126: ...4 82 673831 Rev A ELECTRICAL 4 Page Intentionally Blank ...
Page 239: ...HYDRAULICS 673831 Rev A 6 45 6 Page Intentionally Blank ...
Page 258: ...6 64 673831 Rev A HYDRAULICS 6 Page Intentionally Blank ...
Page 286: ...7 28 673831 Rev A STEERING 7 Page Intentionally Blank ...
Page 350: ...IX IX 12 673831 Rev A INDEX ...
Page 351: ......