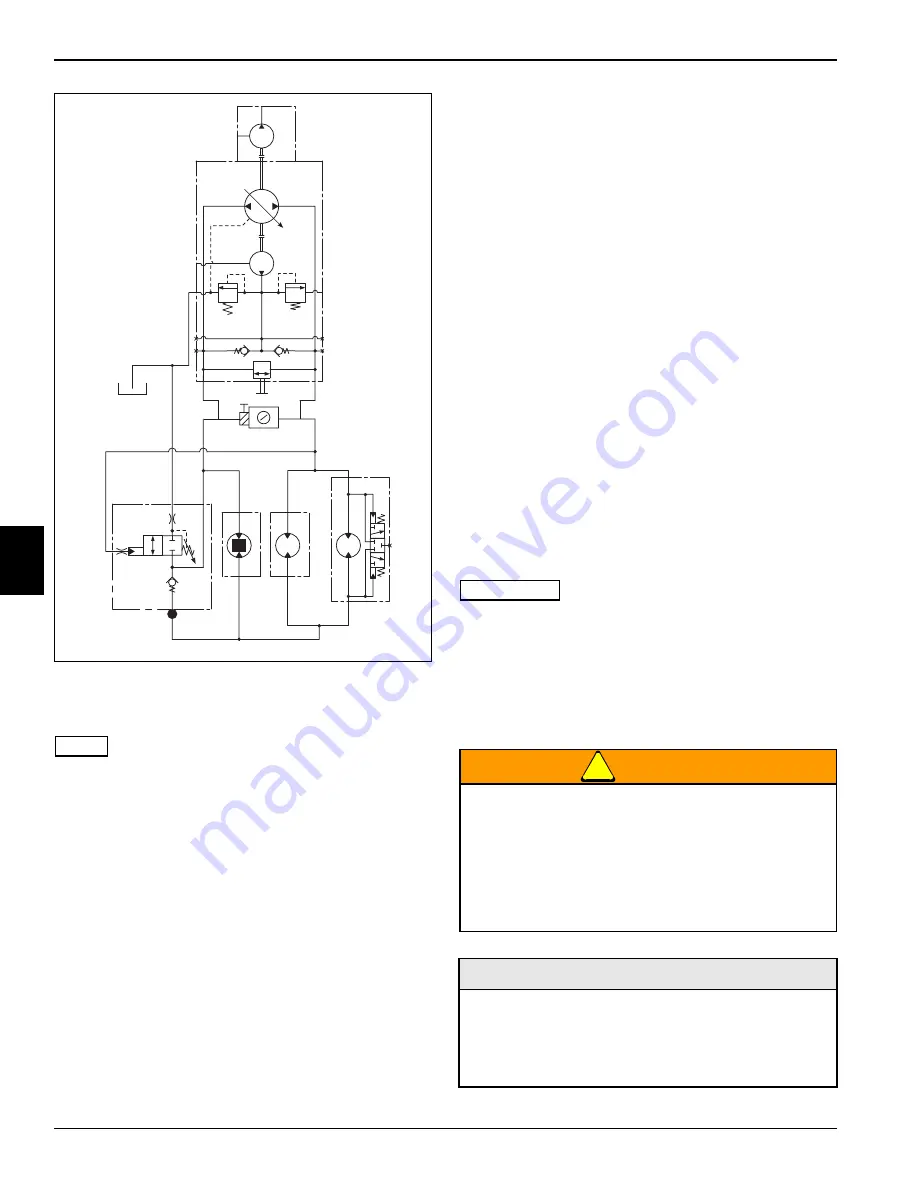
5-48
4252490-Rev A
HYDROSTATIC POWER TRAIN
5
Figure 5-45: Rear Wheel Motor Test—3WD Models—
Blocking Disk Blocking Oil to Flushing Valve Port
“RW1,” Rear Wheel Restrained
NOTE
Verify engine rpm is within specification (3400 rpm ± 50)
to ensure accurate hydraulic test results.
33. Start engine, release park brake, and run at full
throttle (3400 rpm ± 50).
34. Adjust flow lock tool (1) to allow pump to produce 7
gpm (27 lpm) in the forward direction.
35. Use the flow meter to warm the hydraulic oil. Turn
flow meter valve until a reading of 1000 psi (69 bar)
is reached. Warm the oil to 120–150° F (49–65° C);
open valve fully after operating temperature is
reached.
36. After warming the hydraulic oil, verify flow lock tool is
adjusted to allow pump to produce 7 gpm (27 lpm) in
the forward direction.
37. Slowly close flow meter valve until a reading of
2500 psi (172 bar) is reached. Read and record
loaded flow.
38. Stop engine, apply park brake, and return flow lock
tool to the neutral position.
39. Calculate rear wheel motor leakage.
(Step 21 – Step 37 / Step 21 x 100 = Leak
Percentage)
Is rear wheel motor leakage 10% or less?
YES
The rear wheel motor is good. Proceed to
“Flushing Valve Check Valve Test” on
page 5-48.
NO
Proceed to next question.
Is rear wheel motor leakage 11–20%?
YES
The rear wheel motor is marginal. Additional
testing is required. Proceed to “Flushing
Valve Check Valve Test” on page 5-48.
NO
Proceed to next question.
Is rear wheel motor leakage 21% or more?
YES
Repair or replace rear wheel motor. See
“Wheel Motors” on page 5-57, then proceed
to “Flushing Valve Check Valve Test” on
page 5-48.
Flushing Valve Check Valve Test
IMPORTANT
• Performing this test will isolate the flushing valve
check valve from the rest of the hydrostatic
system.
• This test works together with the traction system
test, traction pump tests, and wheel motors tests
to isolate a problem within the hydrostatic power
train.
!
WARNING
TN3107
The hydraulic system is under pressure, and the
oil will be hot.
• Always relieve pressure in the hydraulic
system before performing service.
• Failure to follow appropriate safety
precautions may result in death or serious
injury.
Required Tools and Materials
• Flow Meter
• -8 ORFS Test Hoses 4000 psi (276 bar)
• Flow Lock Tool
• Wheel Restraint
Summary of Contents for JACOBSEN GP400
Page 1: ...GP400 Riding Greens Mower Technical Repair Manual USAG004 USAD004...
Page 2: ......
Page 4: ......
Page 8: ......
Page 11: ...SAFETY 4252490 Rev A 1 3 1 Figure 1 1 TN3769 11 9 5 10 1 2 4 6 7 8 3...
Page 12: ...1 4 4252490 Rev A SAFETY 1 7 1 6 11 8 5...
Page 13: ...SAFETY 4252490 Rev A 1 5 1 Pb 4 2 3 14 10 4127335 SRC 9...
Page 65: ...ELECTRICAL 4252490 Rev A 4 13 4 Page Intentionally Blank...
Page 70: ...4 18 4252490 Rev A ELECTRICAL 4 Page Intentionally Blank...
Page 74: ...4 22 4252490 Rev A ELECTRICAL 4 Page Intentionally Blank...
Page 84: ...4 32 4252490 Rev A ELECTRICAL 4 Page Intentionally Blank...
Page 118: ...4 66 4252490 Rev A ELECTRICAL 4...
Page 128: ...5 10 4252490 Rev A HYDROSTATIC POWER TRAIN 5 Page Intentionally Blank...
Page 132: ...5 14 4252490 Rev A HYDROSTATIC POWER TRAIN 5 Page Intentionally Blank...
Page 136: ...5 18 4252490 Rev A HYDROSTATIC POWER TRAIN 5 Page Intentionally Blank...
Page 140: ...5 22 4252490 Rev A HYDROSTATIC POWER TRAIN 5 Page Intentionally Blank...
Page 144: ...5 26 4252490 Rev A HYDROSTATIC POWER TRAIN 5 Page Intentionally Blank...
Page 192: ...5 74 4252490 Rev A HYDROSTATIC POWER TRAIN 5...
Page 209: ...HYDRAULICS 4252490 Rev A 6 17 6 Page Intentionally Blank...
Page 272: ...7 18 4252490 Rev A STEERING 7...
Page 312: ...8 40 4252490 Rev A CUTTING UNITS 8...
Page 351: ......
Page 353: ......
Page 354: ......