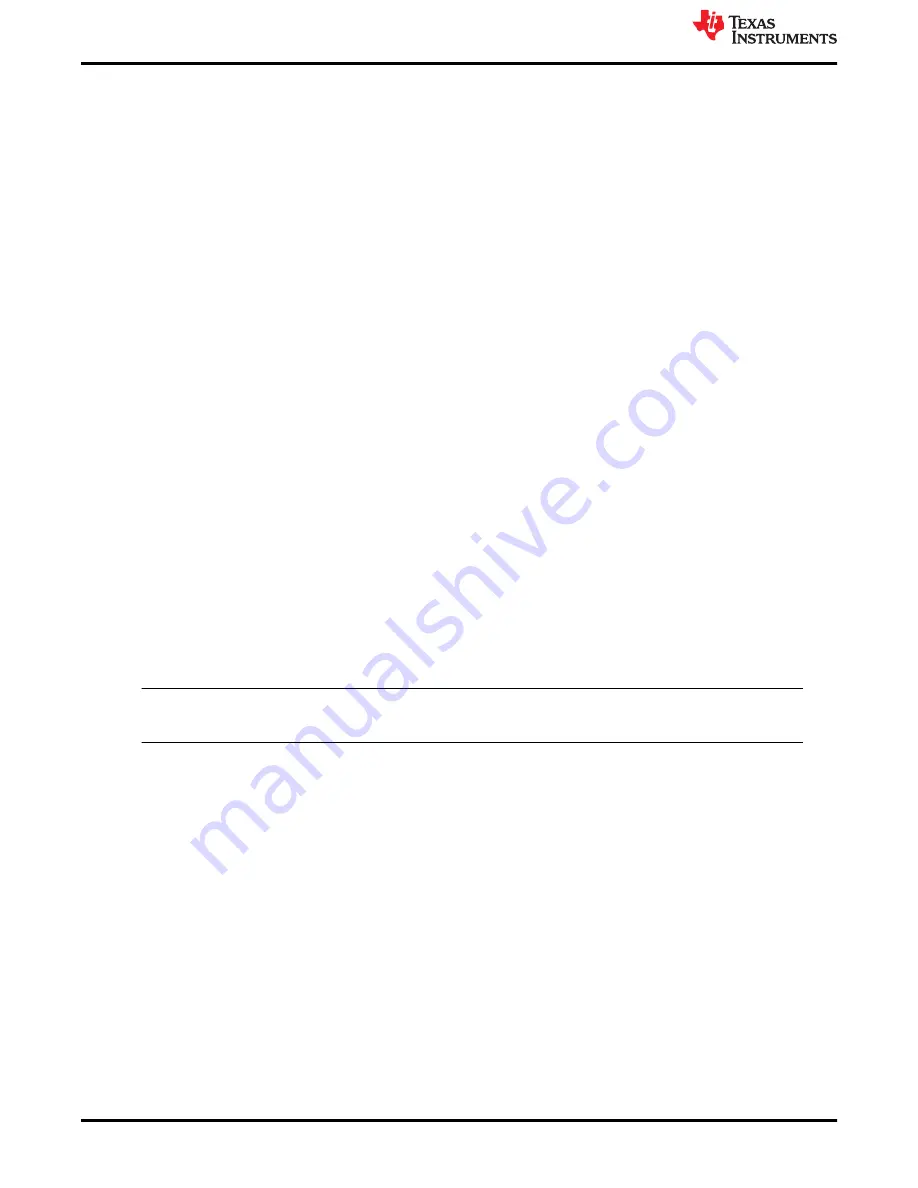
7 Test Procedure
7.1 Line and Load Regulation and Efficiency Measurement Procedure
1. Set up the EVM as described in
and
.
2. Ensure the load is set to constant-resistance mode and to sink at 0 ADC.
3. Ensure all jumper setting are configured as shown in
4. Ensure the jumper provided in the EVM shorts on J2 before V
IN
is applied.
5. Increase V
IN
from 0 V to 12 V. Use V1 to measure input voltage.
6. Remove the jumper on J2 to enable the controller.
7. Use V2 to measure the V
OUT
voltage.
8. Vary the load from 0 ADC to 10 ADC, V
OUT
must remain in load regulation.
9. Vary V
IN
from 8 to 14 V, V
OUT
must remain in line regulation.
10. To disable the converter, place the jumper on J2.
11. Decrease the load to 0 A
12. Decrease V
IN
to 0 V.
7.2 PMBUS Setup and Verification
The TPS53915EVM-PWR587 contains a 10-Ω series resistor in the feedback loop for loop response analysis.
1. Download the Graphical User Interface (GUI) from
2. Type
fusion
in the TI search bar.
3. Select
FUSION_DIGITAL_POWER_DESIGNER
from the search result.
4. Download and install the latest release version of the software. The most current version to date is version
1.8.325 of the Fusion Digital Power Designer.
5. Connect the USB Interface Adaptor EVM (see
for more information) to J4 of the EVM. Ensure
that Pin 1 of the USB interface adaptor (red wire) is connected correctly to Pin 1 of J4 on the EVM.
6. Connect the USB wire of the USB interface adaptor to one of the USB ports on the computer tower.
7. Ensure that the EVM is powered up and connected to the USB interface adaptor before opening the Fusion
Designer GUI.
8. Double click the shortcut icon on the desktop for the Fusion Designer GUI. Use the
online
version.
9. Double click on the
TPS40400, TPS4042x, ect (DEVICE CODE)
from the
Select Device Scanning Mode
10. When the GUI is loaded (see
), verify communication between the GUI and the EVM by changing
the frequency of the EVM.
Note
The TPS53915EVM is pre-set to a 400-KHz switching frequency.
11. Use the oscilloscope to monitor the switching frequency on the EVM on TP6.
12. Select a different frequency by clicking on the drop down box of the
FREQUENCY_CONFIG:TPS53819
(TPS5391X)
.
13. Click on
Write to Hardware
and monitor the change of the switching frequency on the oscilloscope.
See the
TPS53915 1.5 to 18 V (4.5 to 25 V bias) Input, 12-A Single Synchronous Step-Down SWIFT™
for more information regarding PMBUS registers.
Test Procedure
8
TPS53915 Step-Down Converter Evaluation Module User's Guide
SLUUAS2C – OCTOBER 2013 – REVISED NOVEMBER 2021
Copyright © 2021 Texas Instruments Incorporated