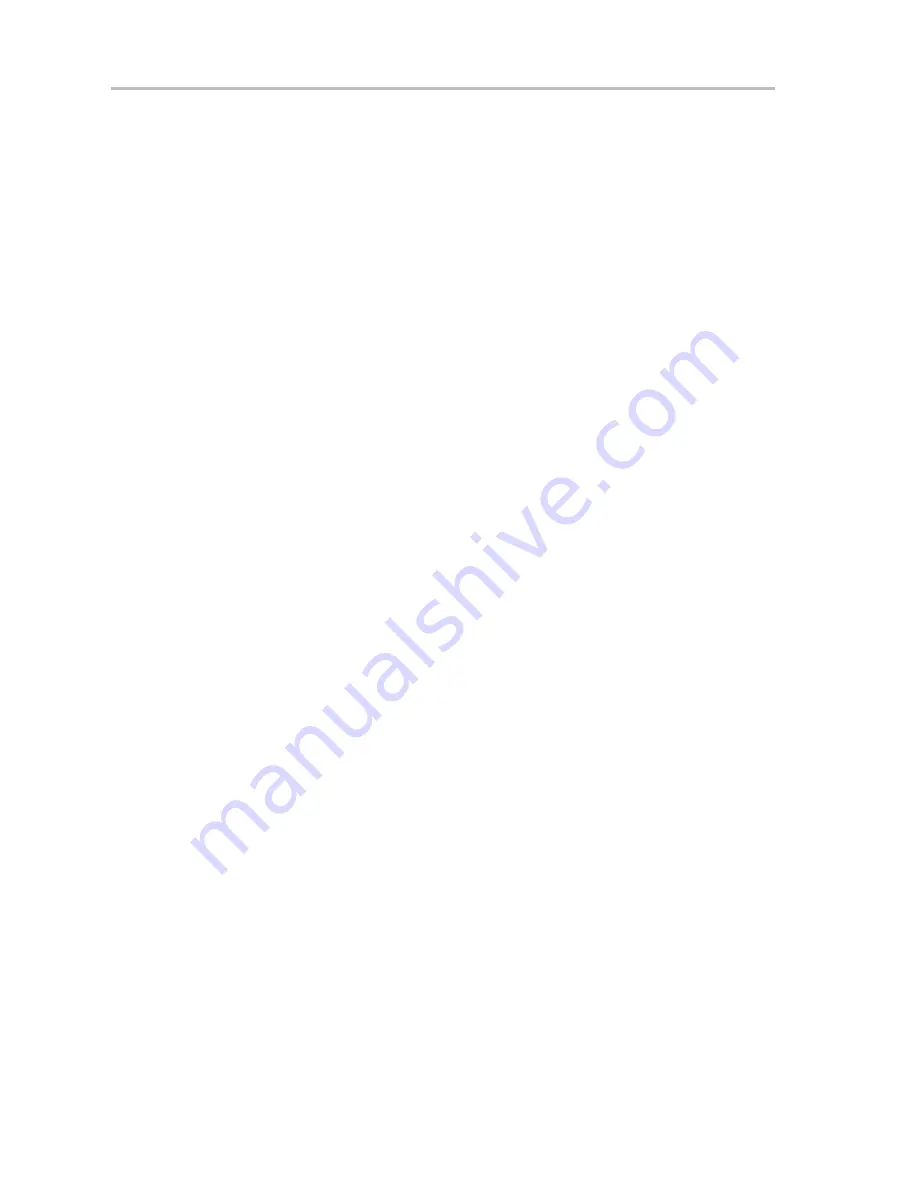
General High-Speed Amplifier Design Considerations
1-16
General Information
1.8
General High-Speed Amplifier Design Considerations
The THS7002 EVM layout has been designed and optimized for use with
high-speed signals and can be used as an example when designing THS7002
applications. Careful attention has been given to component selection,
grounding, power supply bypassing, and signal path layout. Disregard of these
basic design considerations could result in less than optimum performance of
the THS7002 dual differential line drivers and receivers IC.
Surface-mount components were selected because of the extremely low lead
inductance associated with this technology. Also, because surface-mount
components are physically small, the layout can be very compact. This helps
minimize both stray inductance and capacitance.
Tantalum power supply bypass capacitors (C4, C5, and C21) at the power
input pads help supply currents for rapid, large signal changes at the amplifier
output. The 0.1
µ
F power supply bypass capacitors (C2, C3, C11, C12, C18,
and C19) were placed as close as possible to the IC power input pins in order
to keep the PCB trace inductance to a minimum. This improves
high-frequency bypassing and reduces harmonic distortion.
A proper ground plane on both sides of the PCB should always be used with
high-speed circuit design. This provides low-inductive ground connections for
return current paths. In the area of the preamplifier input pins, however, the
ground plane was removed to minimize stray capacitance and reduce ground
plane noise coupling into these pins. This is especially important for the
inverting pin while the amplifier is operating in the noninverting mode. Because
the voltage at this pin swings directly with the noninverting input voltage, any
stray capacitance would allow currents to flow into the ground plane, causing
possible gain error and/or oscillation. Capacitance variations at the amplifier
IC input pin of less than 1 pF can significantly affect the response of the
amplifier.
In general, it is always best to keep signal lines as short and as straight as
possible. Sharp 90
_
corners should generally be avoided — round corners or
a series of 45
_
bends should be used, instead. Stripline techniques should
also be incorporated when signal lines are greater than 3 inches in length.
These traces should be designed with a characteristic impedance of either 50
Ω
or 75
Ω
, as required by the application. Such signal lines should also be
properly terminated with an appropriate resistor.
Finally, proper termination of all inputs and outputs should be incorporated into
the layout. Unterminated lines, such as coaxial cable, can appear to be a
reactive load to the amplifier IC. By terminating a transmission line with its
characteristic impedance, the amplifier’s load then appears to be purely
resistive, and reflections are absorbed at each end of the line. Another
advantage of using an output termination resistor is that capacitive loads are
isolated from the amplifier output. This isolation helps minimize the reduction
in amplifier phase-margin and improves the amplifier stability for improved
performance such as reduced peaking and settling times.