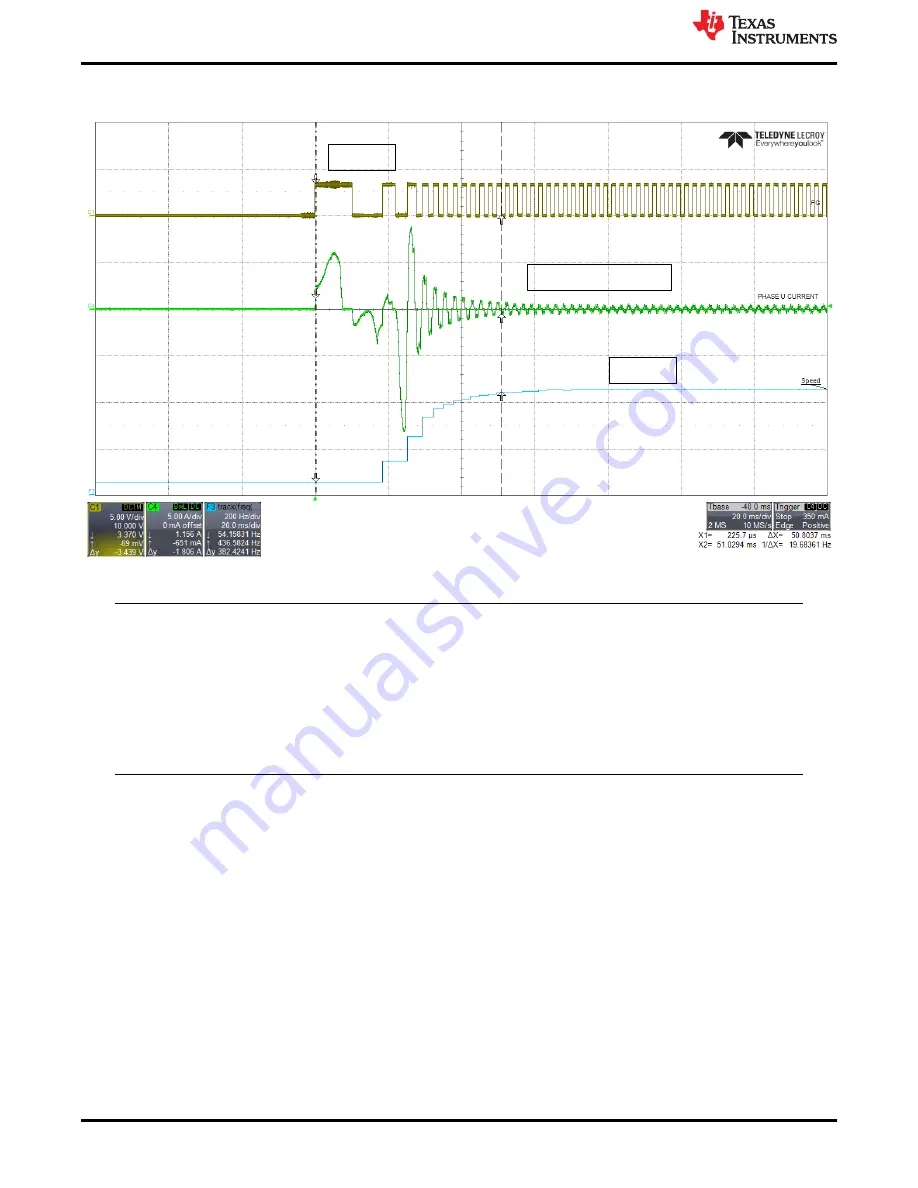
shows FG, phase current and motor electrical speed waveform. Motor takes 50 ms to reach target
speed from zero speed.
Phase current
Speed
FG
Figure 4-2. Phase current, FG and motor speed - Faster startup time
Note
If Abnormal speed fault [ABN_SPEED] or Loss of sync [LOSS_OF_SYNC] fault gets triggered, it is
recommended to follow below debug steps.
1. Select Double align as the motor startup method in [MTR_STARTUP].
2. Increase align time [ALIGN_TIME].
3. Configure align current threshold [ALIGN_CURR_THR] to 50% of cycle by cycle current limit
[ILIMIT].
4. Configure First cycle frequency select [FIRST_CYCLE_FREQ_SEL] to 0.
4.3.5 Improving speed regulation
For applications that require better speed regulation, it is recommended to tune Speed loop PI controllers
[SPD_LOOP_KP] and [SPD_LOOP_KI]. Kp coefficient of speed loop [SPD_LOOP_KP] controls the settling time
and speed overshoots. Ki coefficient of Speed loop [SPD_LOOP_KI] controls speed overshoot and ensures
regulation of speed at set value and drives the error to zero.
Step 1: Enable speed loop [SPEED_LOOP_DIS]
Step 2: Tuning speed loop Kp [SPD_LOOP_KP] and Ki [SPD_LOOP_KI] is experimental. It is recommended to
manually tune Speed loop Kp and Ki till the desired results are achieved.
Refer to
to read back motor speed using DACOUTs.
4.3.6 Stopping motor quickly
MCT8316A provides two options for applications that require stopping the motor quickly.
Option 1: Stopping motor quickly while spinning in closed loop.
Basic Controls
18
MCT8316A Tuning Guide
SLLU336 – MAY 2021
Copyright © 2021 Texas Instruments Incorporated