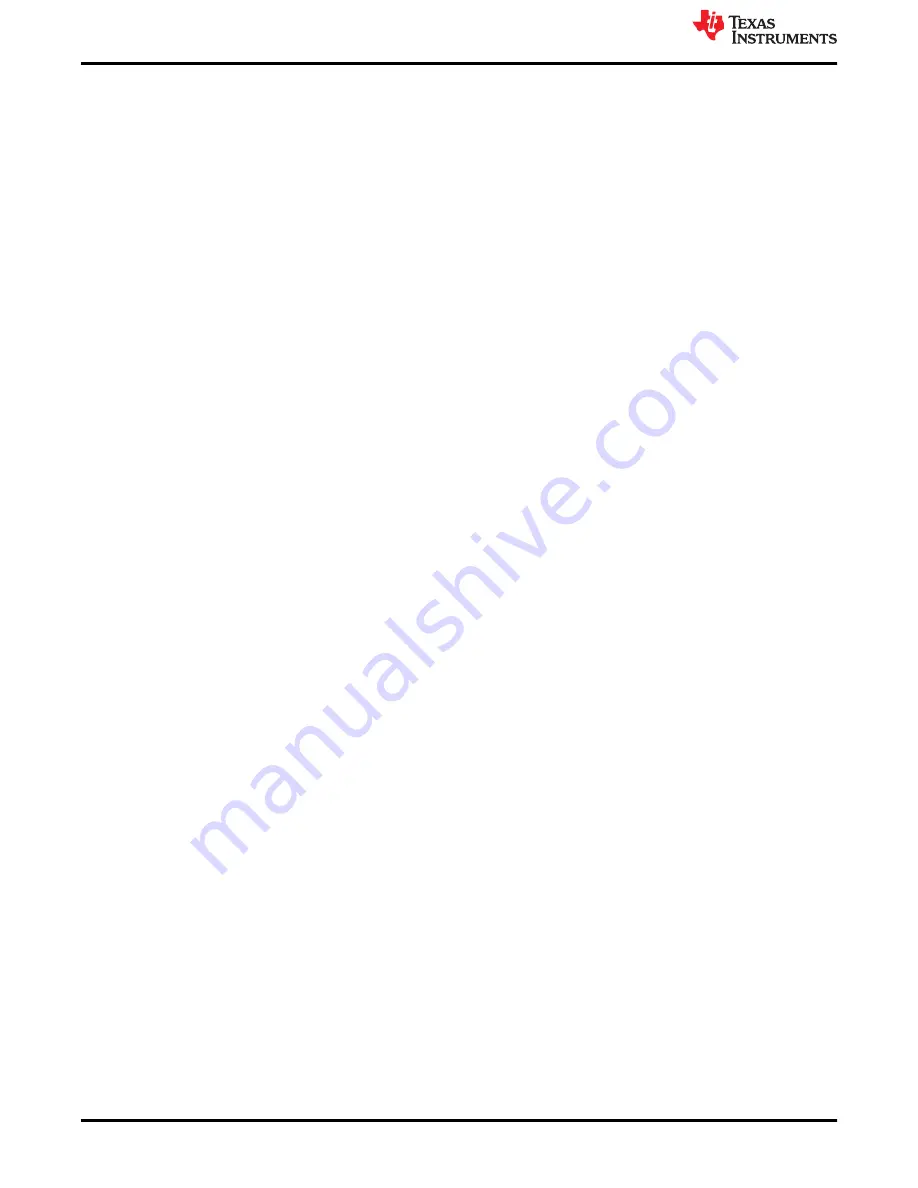
2.2 Design Considerations
2.2.1 Inductive Touch Buttons
The LDC3114-Q1 is the inductive sensing IC used to implement the touch buttons for this reference design.
There are two of these devices implemented on the board, each running four buttons. The LDC3114-Q1 uses
an inductive coil to determine the change in a metal target. The force on the metal target creates a deflection
in the button case and this deformation is measured by the IC to determine a button press. Additionally,
the LDC3114-Q1 includes a baseline tracking algorithm that monitors the button surface and can adapt to
environmental factors such as temperature change or damage to the surface. This device also includes digital
outputs that trigger when the button data crosses above the given threshold. Since the LDC3114-Q1 does not
have a changeable I2C address, an I2C switch (PCA9543) is used to communicate to both devices. This allows
for each device to continuously run the baseline algorithm that monitors the button surface.
Implementing an inductive touch button requires a metal target that is at a fixed distance from the sensor coil.
Aside form the general design theory for inductive sensors, there are a few important design considerations
to keep in mind when designing inductive touch buttons. For some button designs, the desired touch surface
might not be metal. In this case, a thin metal plane can be added behind a non-conductive surface, like plastic,
that acts as the metal target for the design. The distance between the sensor coil and the metal target is an
important factor for getting the desired button sensitivity for an application. The general guideline for this is for
the distance to stay between 3-20% of the coil diameter. This ensures that metal target does not touch the
sensor coil when it deflects but keeps it close enough to obtain a high force sensitivity. If the metal target gets
farther away from the sensor coil, then the button will have decreased sensitivity and can require more force to
get a proper button output. Since the target distance is an import part of the design, the coil diameter becomes
a critical design parameter as well. Many times, this parameter is constrained by the space available for the
sensor coils to be implemented on a PCB. From there, other factors like the number of turns, trace width, trace
spacing, and number of layers all account for the overall coil design. The trace width and spacing can be limited
by the PCB manufacturing process but can also be useful for changing the series resistance of the inductor
coil or allowing for more turns to be included. Generally, it is recommended to use the number of turns to set
the inner diameter of the inductive coil between 20-80% since the inner turns do not have as much impact on
the magnetic field. However, in a button application, the target is close enough that the inner coils still provide
additional benefit so increasing the number of turns to decrease the inner diameter can be considered for the
design. For more information on button design, please read the
Inductive Touch System Design Guide for HMI
.
For this reference design, the mechanical structure of the button is comprised of the 3D printed housing, the
PCB, and metal tape to provide a target surface. PCB space for the button was not a concern for this design
so an 8 mm diameter was chosen for the coil design. The
LDC Calculator Tool spreadsheet
determine the rest of the coil parameters. A trace width and spacing of 5 mils was used along with 8 turns per
layer. This makes the coil inner diameter slightly smaller than 4 mm. Or in other words, the coil fill ratio (inner
diameter divided by outer diameter) is roughly 50%. For most button designs, minimizing the coil fill ratio can
provide additional sensitivity but requires the target surface to be very close to the coil for it to be beneficial.
Otherwise, it is best to keep the ratio between 20% and 80% to maximize the Q factor of the design. Since this is
a two layer board, the number of layers for the coil design was set to two. The capacitance for this sensor design
was selected to be 220 pF which put the frequency at 8.396 MHz.
System Overview
4
Inductive Touch and Magnetic Dial Contactless User Interface Reference
Design
Copyright © 2022 Texas Instruments Incorporated