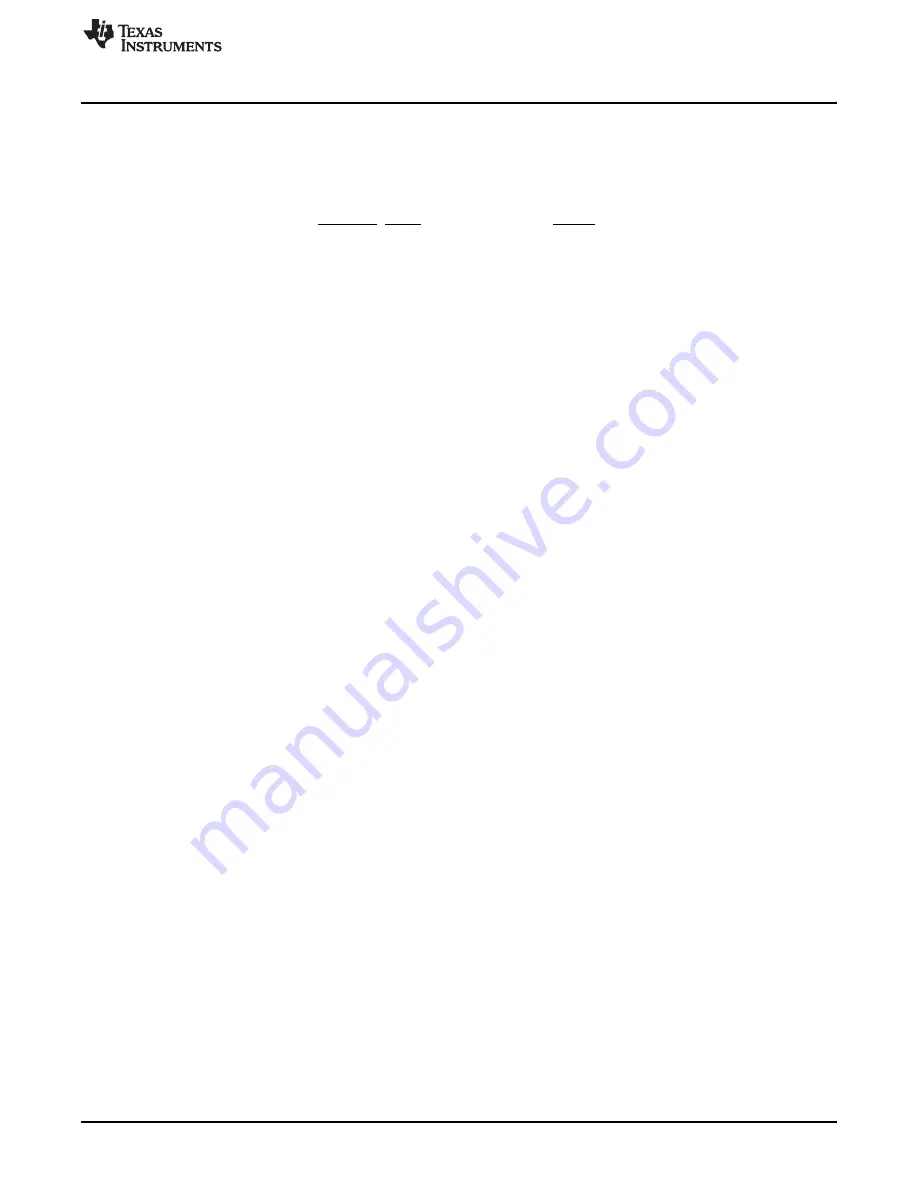
Layout and Bill of Material
8
Layout and Bill of Material
8.1
bq51020 Traces
The bq51020 device pins can be classified as follows:
•
Signal/Sensing Traces
–
TS/CTRL, EN1, EN2, PD_DET, WPG, COMM, ILIM, AD, ADEN, FOD, TMEM, CM_ILIM, VO_REG,
VTSB, Term.
–
Make sure these traces are not interfered by the noisy traces
•
Noisy Traces
–
AC1, AC2, BOOT, COMM
–
Make sure these traces are isolated from other traces, use ground plan
•
Power Traces
–
AC1, AC2, OUT, CLAMP, PGND
–
Make sure to use the correct width for the right current rating.
8.2
Layout Guidelines
Use the following layout guidelines:
•
The traces from the input connector to the inputs of the bq51020 IC pin should be as wide as possible
to minimize the impedance in the lines. Otherwise, this causes a voltage drop and thermal issue.
•
Keep the trace resistance as low as possible on AC1, AC2, OUT, and PGND.
•
Use the appropriate current rating traces (width) the AC, OUT and PGND.
•
The PCB should have a ground plane (return) connected directly to the return of all components
through vias (At least two vias per capacitor for power-stage capacitors, one via per capacitor for
small-signal components).
•
The dissipation of heat path is important. Adding internal layers increases the thermal performance.
Multiple vias in the PGND pins of the IC is recommended to decrease the thermal resistance in the
board and allow much easier thermal dissipation through inner layer and power ground layers.
•
The via interconnect is important and must be optimized near the power pad of the IC and the GND.
•
2-oz copper, or greater, is recommended
•
For high-current applications, the balls for the power paths should be connected to as much copper in
the board as possible. This allows better thermal performance because the board conducts heat away
from the IC.
•
It is always good practice to place high frequency bypass capacitors next to RECT and OUT.
8.3
Printed-Circuit Board Layout Example
The primary concerns when laying a custom receiver PCB are as follows:
•
AC1 and AC2, GND return trace resistance
•
OUT trace resistance
•
GND connection
•
Copper weight
≥
2 oz
For a 1-A fast charge current application, the current rating for each net is as follows:
•
AC1 = AC2 = 1.2 A
•
BOOT1 = BOOT2 = 1 A
•
RECT = 50 mA
•
OUT = 1 A
•
COMM1 = COMM2 = 300 mA
•
CLAMP1 = CLAMP2 = 500 mA
15
SLUUB03 – April 2014
bq51020EVM (5-W WPC) Integrated Wireless Receiver Power Supply
Copyright © 2014, Texas Instruments Incorporated