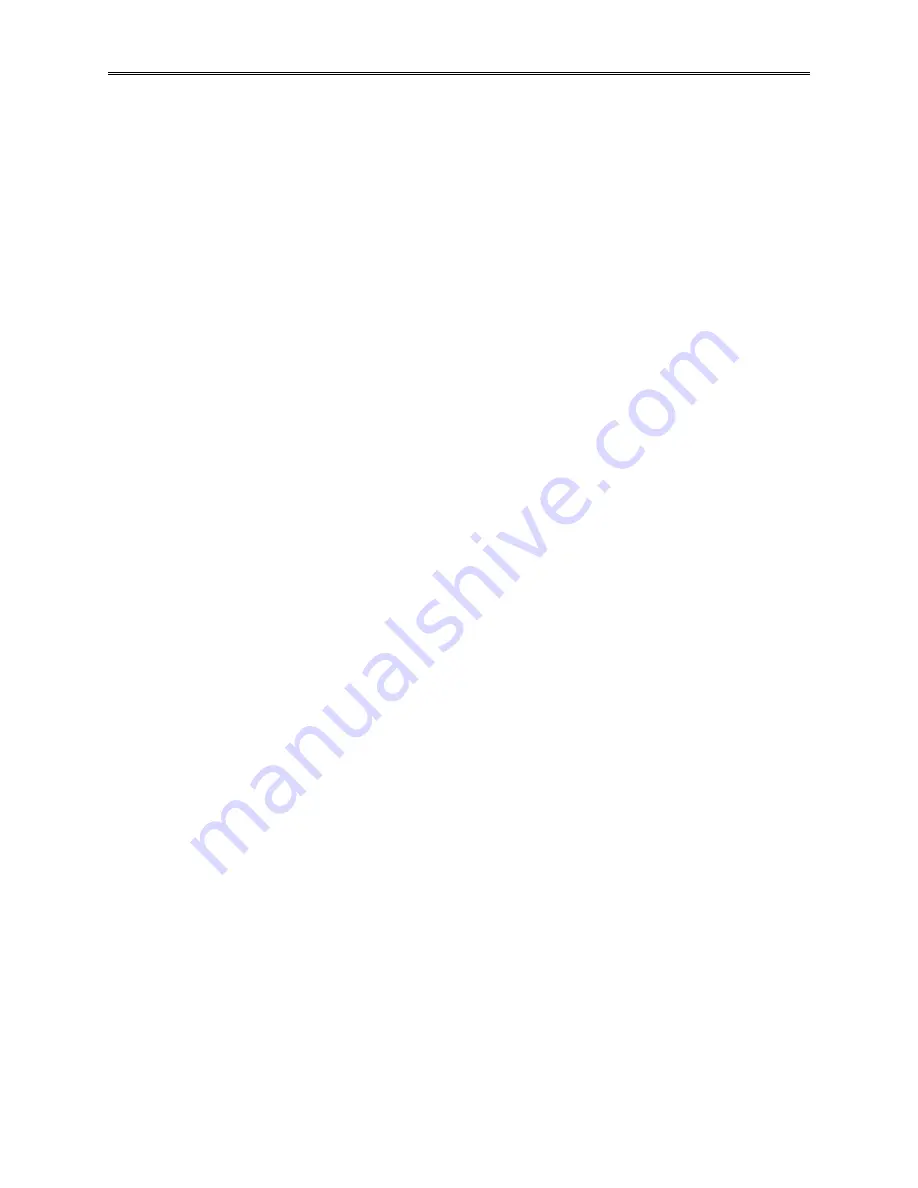
Chapter 7 – Maintenance
TestEquity 1007H Temperature Chamber
Page 7-5
How to Verify the Performance
(Controlled humidity mode)
These tests verify the performance of the heating, single-stage refrigeration mode,
humidification, electrical controls, F4T/F4 Controller, and air circulation systems. The chamber
should meet all published performance specifications for controlled humidity conditions if all of
these tests are successfully passed. These tests assume that the F4T/F4 Controller’s setup and
tuning values have not been changed from the values as shipped from TestEquity. Also, the
Limit Controller high limit must be set to over +85°C (+88°C would be fine). If the chamber
fails any of these tests, it should be removed from service to prevent further damage until the
cause of the problem is determined and resolved.
1.
The chamber interior should be empty and at ambient temperature, approxi23°C.
Water Inlet must be connected to a source of filtered water or the optional water recirculation
system.
2.
Set the F4T/F4 Controller temperature set point to 85.0°C, and humidity set point to 85.0%
RH. F4T Humidity button or F4 Digital Output 2 must be ON. Turn the Master Switch ON.
3.
The Heat Light and Humidity Mode Light should be ON continuously and the Cool light
should be OFF. The Humidity Light should be ON continuously only after the humidifier
fills up with water.
4.
The chamber should heat up to about 80°C and begin controlling (Heat Light cycles
ON/OFF) within 7 minutes.
5.
The chamber temperature should slowly increase and stabilize to 85°C. It should NOT
overshoot beyond 85°C by more than 1.0°C, and the compressor should NOT need to turn
ON at this point in order to maintain 85°C.
6.
The chamber humidity should begin to increase within approximately 5-10 minutes after the
Humidity Light turns on. Then, the humidity should increase to 75% RH and the begin
controlling (Humidity Light cycles ON/OFF)
7.
After stabilization, the chamber temperature should be 85.0°C, ±0.5°C. The humidity should
be 85.0%RH, ±0.5% on a short-term basis.
8.
Next, change temperature set point to 50.0°C. Leave the humidity set point at 85.0% RH
9.
The high-stage compressor should turn ON (if it was not already ON), the Cool Light should
be ON continuously and the Heat Light should be OFF. The humidity will drop at this point.
10.
The chamber should cool down to about 55°C and begin controlling (Cool Light cycles
ON/OFF) within a short time.
11.
The chamber temperature should decrease and stabilize to 50°C. It should NOT undershoot
50°C by more than 2°C, and the compressors should NOT need to turn OFF in order to
maintain 50°C. After stabilization, the chamber temperature should be 50.0°C ±0.5°C, or a
total of 1°C. It may take approximately 45 minutes to stabilize at 85.0%, ±2.0%RH.
12.
Next, change the humidity set point to 50.0%RH. Leave the temperature set point at 50.0°C.
13.
The Humidity light will be OFF. The chamber humidity should go down to about 60%RH
fairly quickly. It may take approximately 15 additional minutes to stabilize at 50.0%,
±3.0%RH.
14.
This concludes the controlled-humidity chamber performance verification tests.