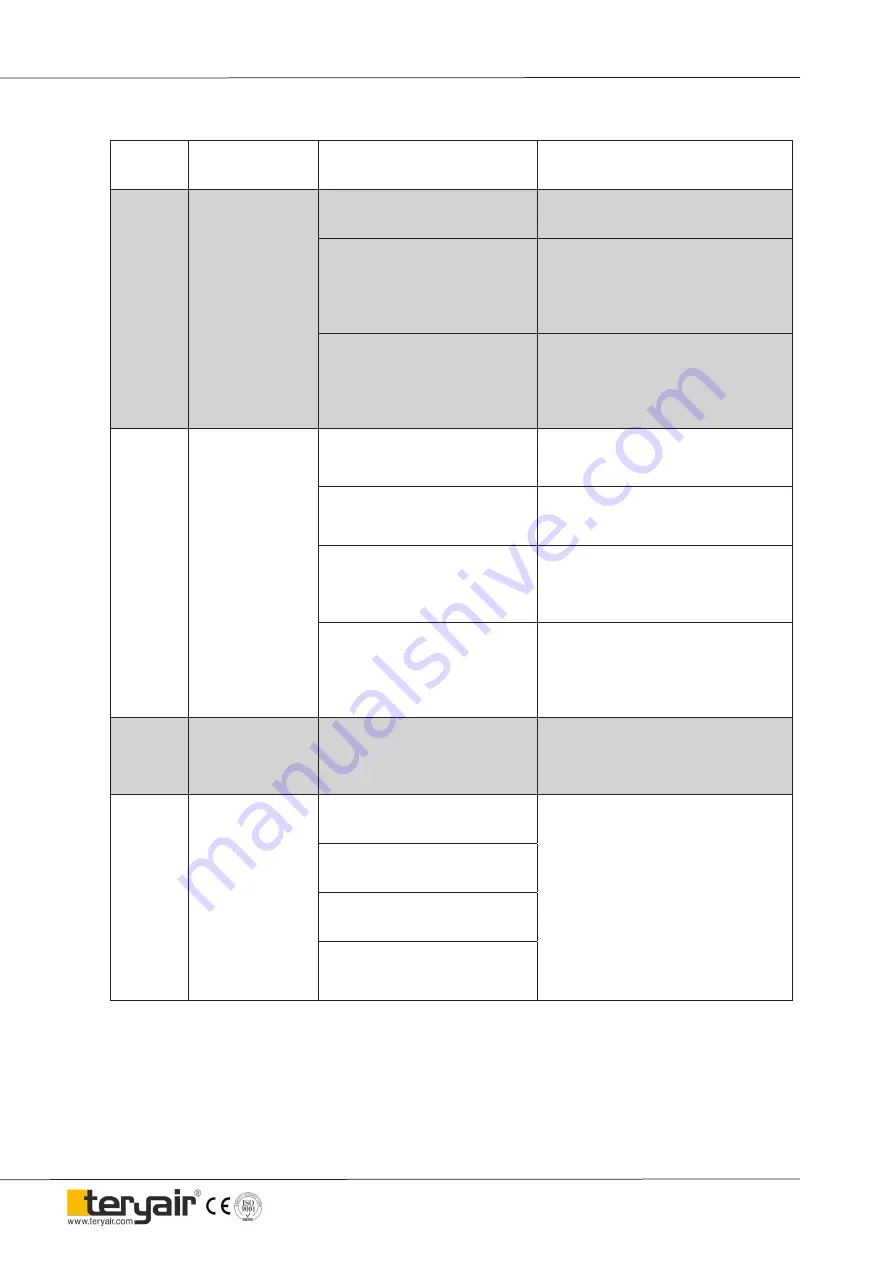
FF-MM-360-REV - 02
Page 7
Operation and Maintenance Guide ADPB 15 Plastic Pump Series
Troubleshooting
Serial No
Description
Causes
Remedial Action
1
Pump stops and
will not start
Insufficient Air Pressure
Check air pressure is as recommended
at the pump air inlet
Air Filter Blocked
Check if debris has clogged the inlet fil-
ter on the FRL unit/pump inlet air valve
( some models have air filter on the air
inlet valve ) and ensure clear passage of
air
Internal damage or excessive wear
on components
roceed to dismantle the pump, examine
component for wear, replace any worn
components, re assemble carefully as
instructed in this manual and re start
the pump.
2
Pumps runs slowly,
poor delivery
Cavitation
Check if cavitation is occurring in the
suction side, if so reduce suction vacu-
um by slowing down the pump.
Worn Balls and Seats
Check proper sealing action of balls
against seals, these components need to
be replaced as a set if they are worn.
Insufficient or wrong lubricant in
the air supply.
Ensure that the lubricant is as per the
recommended chart, a thicker lubricant
often makes the air valve work sluggish-
ly
Internal damage or excessive wear
on components
Proceed to dismantle the pump, exam-
ine component for wear, replace any
worn components, re assemble carefully
as instructed in this manual and re start
the pump.
3
Pump air valve
frerzes
Excessive moisture in supply air
line.
Ensure that the dew point of the
supplied air is low enough. Install a
air dryer or moisture separator on the
supply line
4
Air bubbles in
pump discharge or
product sprays out
of exhaust vent
Broken Diaphragm
Proceed to dismantle the pump,
examine component for wear, replace
any worn components, re assembly care-
fully as instructed in this manual and re
start the pump
mproper seal between inner
pistons, outer pistons and shaft.
Air leakage into product from
balls / seats area
Air sucked into suction pipeline
due to insufficiently tight joints on
suction pipeline.