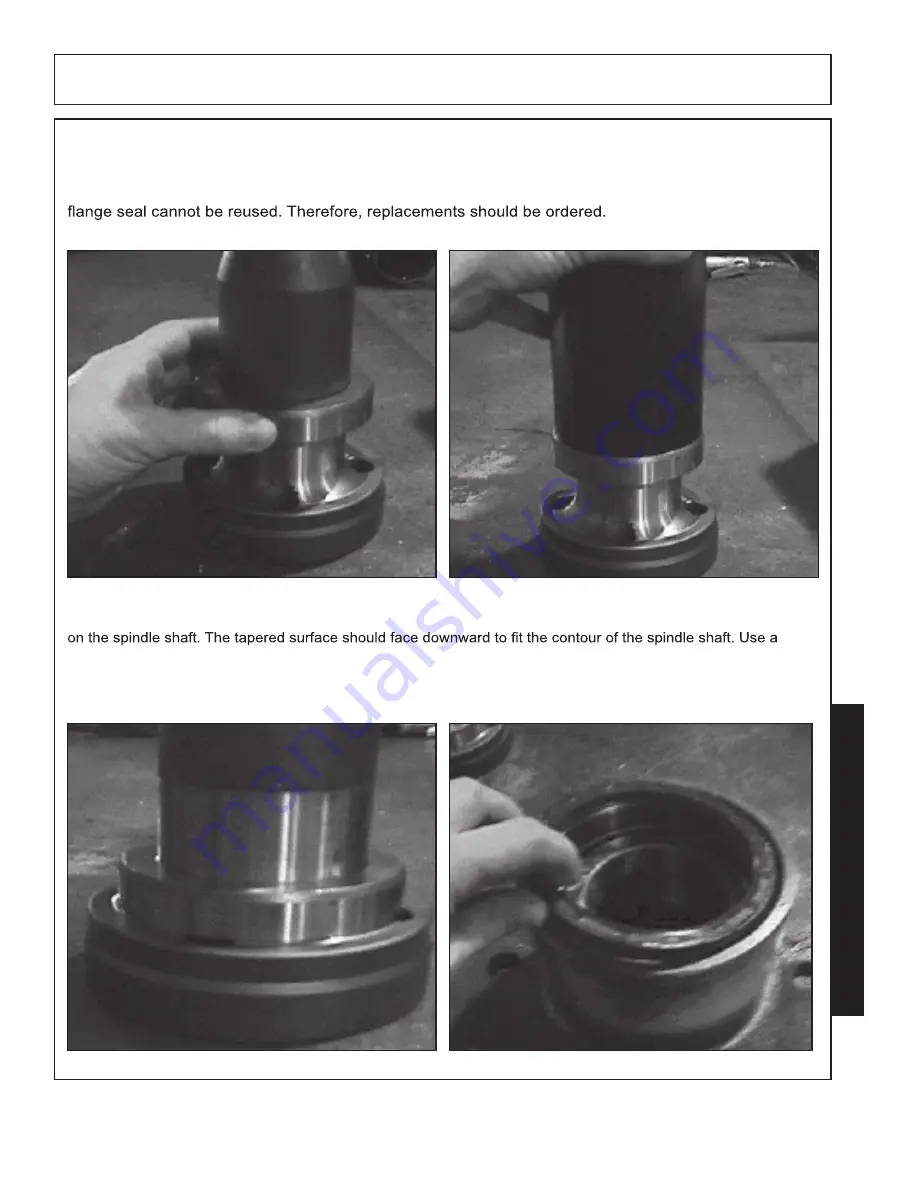
KB21 Service Manual Pub 09-14
88
Mowers & Spindles
60-B. Spindle
Asy Repair
Spindle Housing Assembly
If installing new bearings, be sure to install new bearing cups (races). When installing the bearing cups,
make sure that they are properly seated into the housing. DO NOT DRIVE AGAINST THE BEARING
SURFACE. All parts should be thoroughly cleaned. The bearing nut, the lower seal and the motor
Place a thin coat of silicone on the inside (tapered side) of the bearing ring (Fig-N). Place the bearing ring (Fig-O)
piece of 2-3/4” 16 gauge tubing, 8” long to drive the bearing ring down on to the spindle until the bearing
ring bottoms out against the spindle (Fig-P). Remove any excess silicone from the spindle shaft and bearing ring.
Turn the housing upside down so that the bearing seal and retaining ring may be installed. Lubricate the
seal prior to installation (Fig-R).
FIGURE - O
FIGURE - P
FIGURE - Q
FIGURE - R
Summary of Contents for KB21
Page 1: ...KB21 10 14 2014 37002994247S ...
Page 2: ...KB21 Service Manual Pub 09 14 2 ...
Page 3: ...KB21 Service Manual Pub 09 14 3 1 800 882 5756 1 800 882 5758 ...
Page 7: ...KB21 Service Manual Pub 09 14 7 Section 10 Safety ...
Page 8: ...KB21 Service Manual Pub 09 14 8 ...
Page 9: ...KB21 Service Manual Pub 09 14 9 ...
Page 10: ...KB21 Service Manual Pub 09 14 10 ...
Page 11: ...KB21 Service Manual Pub 09 14 11 ...
Page 12: ...KB21 Service Manual Pub 09 14 12 ...
Page 13: ...KB21 Service Manual Pub 09 14 13 ...
Page 14: ...KB21 Service Manual Pub 09 14 14 ...
Page 15: ...KB21 Service Manual Pub 09 14 15 ...
Page 16: ...KB21 Service Manual Pub 09 14 16 ...
Page 17: ...KB21 Service Manual Pub 09 14 17 ...
Page 18: ...KB21 Service Manual Pub 09 14 18 ...
Page 19: ...KB21 Service Manual Pub 09 14 19 ...
Page 20: ...KB21 Service Manual Pub 09 14 20 ...
Page 21: ...KB21 Service Manual Pub 09 14 21 ...
Page 22: ...KB21 Service Manual Pub 09 14 22 ...
Page 23: ...KB21 Service Manual Pub 09 14 23 ...
Page 24: ...KB21 Service Manual Pub 09 14 24 ...
Page 25: ...KB21 Service Manual Pub 09 14 25 P N 30002988455 ...
Page 26: ...KB21 Service Manual Pub 09 14 26 P N D624 ...
Page 27: ...KB21 Service Manual Pub 09 14 27 P N D688 P N D622 ...
Page 28: ...KB21 Service Manual Pub 09 14 28 P N D626 P N D619 P N D620 ...
Page 29: ...KB21 Service Manual Pub 09 14 29 P N D621 P N D835 ...
Page 30: ...KB21 Service Manual Pub 09 14 30 P N D637 P N D617 P N D623 ...
Page 31: ...KB21 Service Manual Pub 09 14 31 ...
Page 32: ...KB21 Service Manual Pub 09 14 32 ...
Page 33: ...KB21 Service Manual Pub 09 14 33 Safety ...
Page 34: ...KB21 Service Manual Pub 09 14 34 Safety ...
Page 36: ...KB21 Service Manual Pub 09 14 36 ...
Page 76: ...KB21 Service Manual Pub 09 14 76 Mowers Spindles 60 A Rotary Mowers ...
Page 78: ...KB21 Service Manual Pub 09 14 78 Mowers Spindles 60 A Rotary Mowers insufficient l o g l l ...
Page 79: ...KB21 Service Manual Pub 09 14 79 Mowers Spindles 60 A Rotary Mowers ...
Page 83: ...KB21 Service Manual Pub 09 14 83 Mowers Spindles 60 B Spindle Asy Repair ...
Page 91: ...KB21 Service Manual Pub 09 14 91 Mowers Spindles 60 B Spindle Asy Repair ...
Page 93: ...KB21 Service Manual Pub 09 14 93 Section 80 Testing Subsections 80 A Mechanical Control Valve ...
Page 96: ...KB21 Service Manual Pub 09 14 96 ...
Page 100: ...KB21 Service Manual Pub 09 14 100 C first h replace the Channel Seals References 90 A REPAIR ...
Page 102: ...KB21 Service Manual Pub 09 14 102 is to the s s h g fourth g g b g h References 90 A REPAIR ...
Page 103: ...KB21 Service Manual Pub 09 14 103 r p p o u c References 90 A REPAIR ...
Page 105: ...KB21 Service Manual Pub 09 14 105 4 5 6 7 References 90 A REPAIR ...
Page 106: ...KB21 Service Manual Pub 09 14 106 8 9 10 11 12 References 90 A REPAIR ...
Page 107: ...KB21 Service Manual Pub 09 14 107 13 References 90 A REPAIR ...
Page 108: ...KB21 Service Manual Pub 09 14 108 14 15 16 17 References 90 A REPAIR ...
Page 109: ...KB21 Service Manual Pub 09 14 109 References 90 B PUMP REPAIR PARTS LOCATION ...
Page 112: ...KB21 Service Manual Pub 09 14 112 References 90 C PUMP SHAFT ISSUES ...
Page 114: ...KB21 Service Manual Pub 09 14 114 References 90 D HYDRAULIC SYSTEM OPERATION ...
Page 115: ...KB21 Service Manual Pub 09 14 115 Reference 90 E PVG32 TROUBLESH OOTING ...
Page 116: ...KB21 Service Manual Pub 09 14 116 Reference 90 E PVG32 TROUBLESH OOTING ...
Page 117: ...KB21 Service Manual Pub 09 14 117 References 90 F Safety Refere nces ...
Page 118: ...KB21 Service Manual Pub 09 14 118 References 90 F Safety Refere nces ...
Page 119: ...KB21 Service Manual Pub 09 14 119 References 90 F Safety Refere nces ...
Page 120: ...KB21 Service Manual Pub 09 14 120 References 90 F Safety Refere nces ...
Page 121: ...KB21 Service Manual Pub 09 14 121 5HIHUHQFHV 6 DIHW 5 HIHUHQF HV ...
Page 122: ...KB21 Service Manual Pub 09 14 122 5HIHUHQFHV 6 DIHW 5 HIHUHQF HV ...
Page 123: ...KB21 Service Manual Pub 09 14 123 5HIHUHQFHV 6 DIHW 5 HIHUHQF HV ...
Page 124: ...KB21 Service Manual Pub 09 14 124 5HIHUHQFHV 6 DIHW 5 HIHUHQF HV ...
Page 125: ...KB21 Service Manual Pub 09 14 125 5HIHUHQFHV 6 DIHW 5 HIHUHQF HV ...
Page 126: ...KB21 Service Manual Pub 09 14 126 37002994247S ...