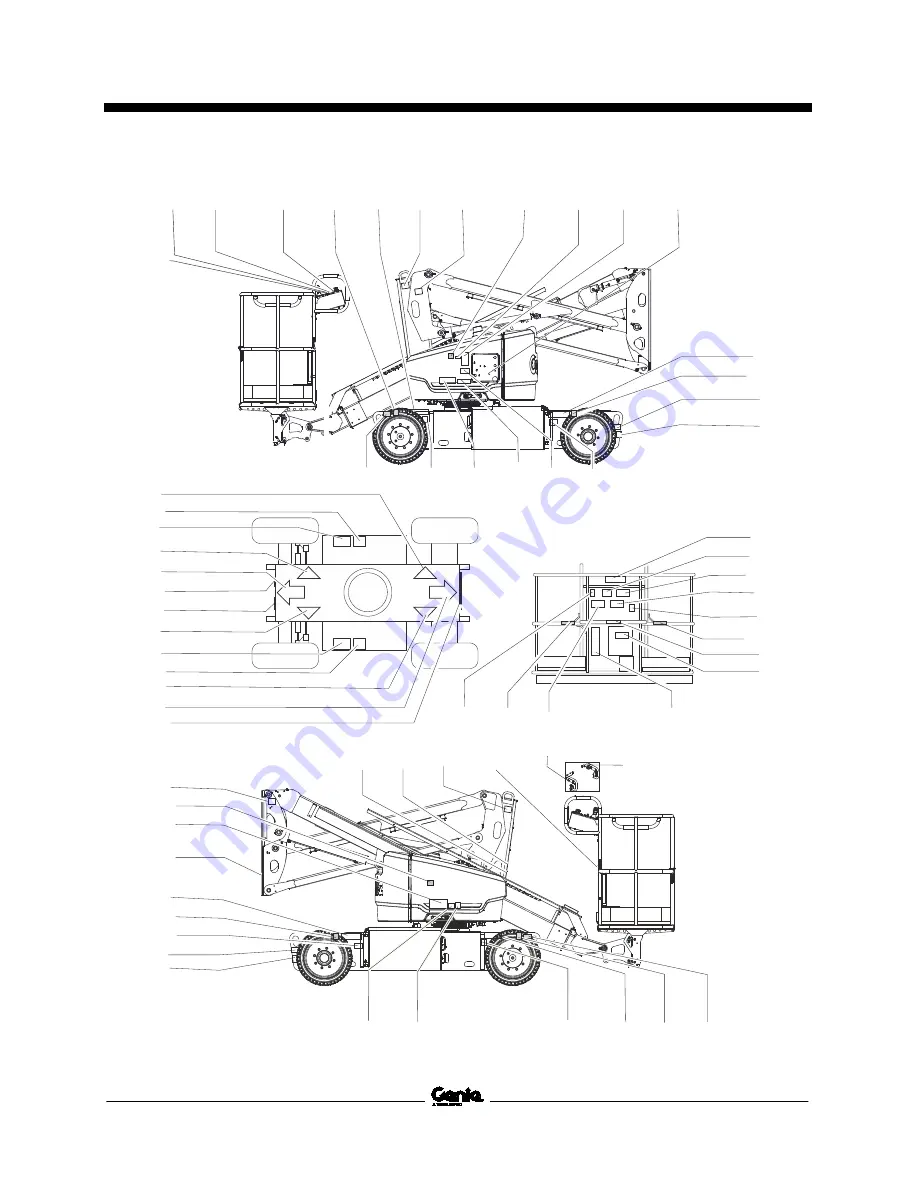
First Edition • Second Printing
Operator's Manual
Inspections
Part No. 1257143GT
Z
®
-33
37
27204
27206
114334
133286
27207
27207
114252
114345
114345
82481
27205
82481
27206
114252
82487
97815
114249
114252
114249
133067
82487
1257156
1258982
1258499
1258982
1258982
1281175
114249
133067
1258499
1261930
1257157
1258500
72086
52475
72086 1258982
72086
52475
72086
52475
114249 52475 72086
1258501
133067
219958
*28174
*28235
1281175
219956
114248
1281175
1281175
72086
1261869
1262127
1262127
44981
114427
1272242
*28174
*28235 44981
1263542
1263542
1286362
1278982
1278542
1261929
72867