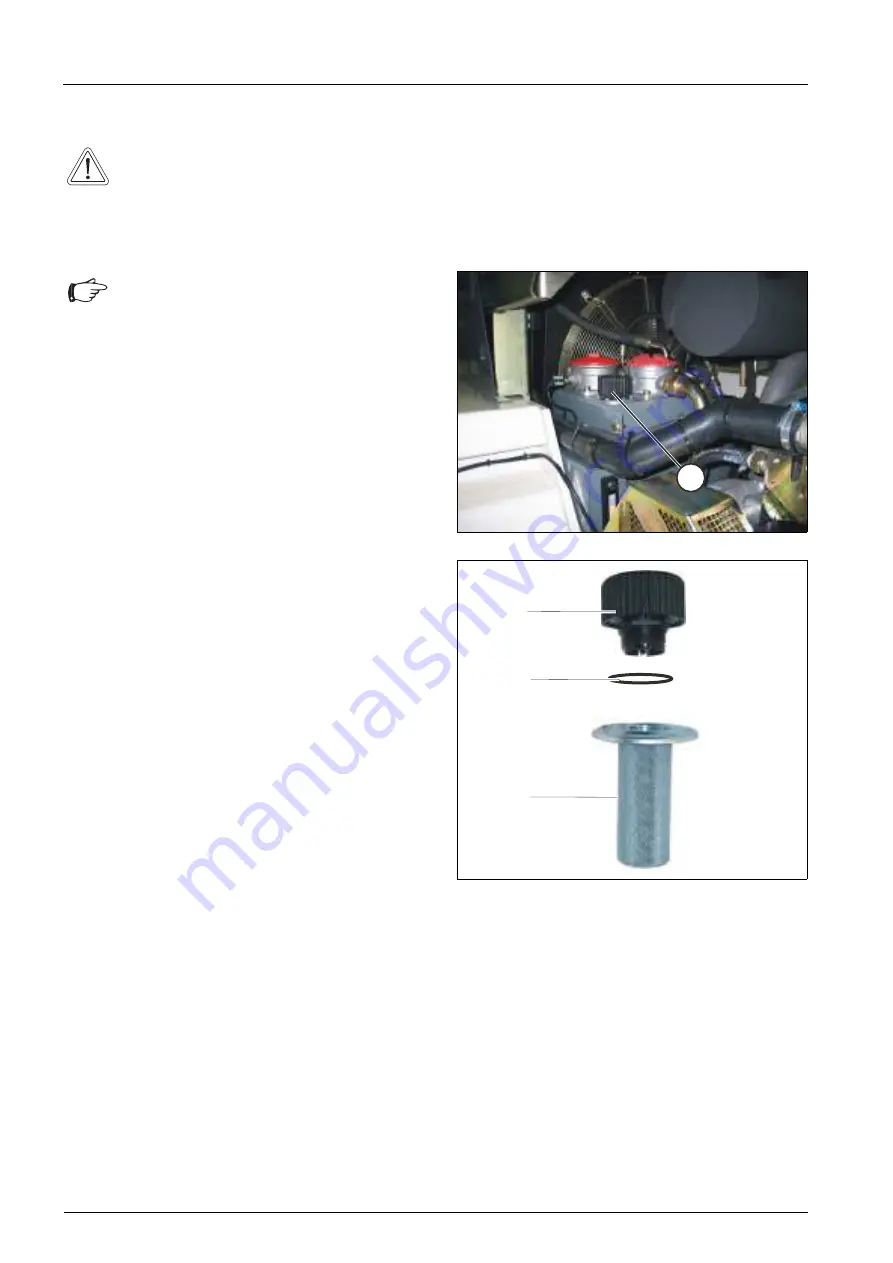
Care and Maintenance
7
95/112
TL160
Operating Manual 12.9.08 Version 1.0
7.8.13 Replacing the breather
•
Remove the breather (71/2) and dispose of
according to regulations.
•
Clean the screen (72/3) and check for damage;
replace if required.
•
Screw in new breather (72/1) with O-ring (72/2)
and tighten by hand.
Machine damage
due to dirt reaching the uncovered hydraulic
oil tank.
• Before starting, clean all parts above the
tank.
Fig. 71
Hydraulic oil tank
L864-724
2
Attention
• The breather must be replaced if it is dirty,
for example due to hydraulic oil vapor.
Fig. 72
Replacing the breather
1
L864-725
2
3
Summary of Contents for TL160
Page 6: ...Index 6 112 TL160 Operating Manual 12 9 08 Version 1 0...
Page 12: ...12 112 TL160 Introduction 1 Operating Manual 12 9 08 Version 1 0...
Page 22: ...Safety and Accident Prevention 2 22 112 TL160 Operating Manual 12 9 08 Version 1 0...
Page 62: ...Recovery Loading and Transporting 6 62 112 TL160 Operating Manual 12 9 08 Version 1 0...
Page 104: ...Care and Maintenance 7 104 112 TL160 Operating Manual 12 9 08 Version 1 0...
Page 110: ...Appendix 9 110 112 TL160 Operating Manual 12 9 08 Version 1 0...
Page 114: ......