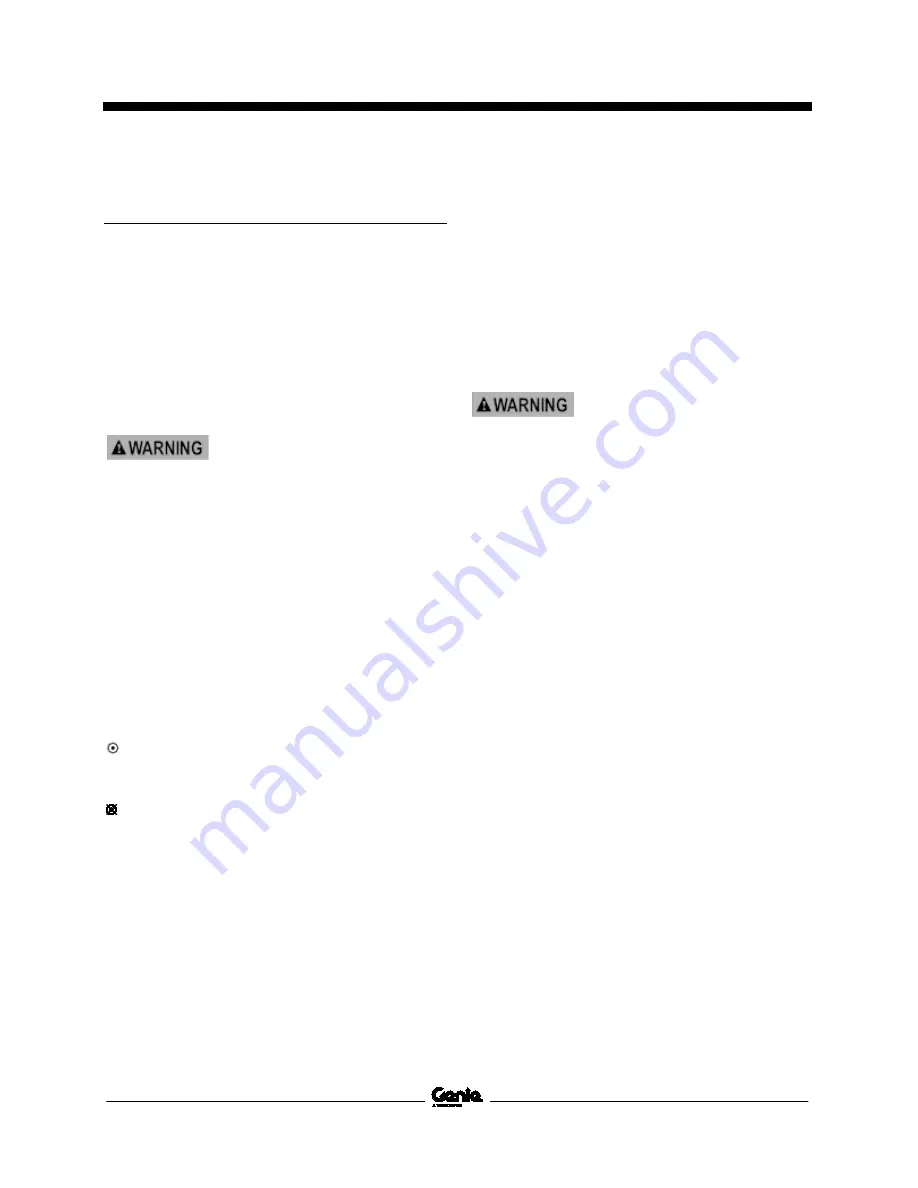
October 2021
Service and Repair Manual
Hydraulic Pumps
Part No. 1268515GT
Z
®
-34/22 Bi-Energy
47
8-1
Auxiliary Pump
How to Test the Au xiliary Pu mp
How to Test the Auxiliary Pump
Note: When removing a hose assembly or fitting,
the O-ring (if equipped) on the fitting and/or hose
end must be replaced. All connections must be
torqued to specification during installation. Refer to
Specifications,
Hydraulic Hose and Fitting Torque
Specifications.
1 Tag, disconnect and plug the high pressure
hydraulic hose from the auxiliary pump.
Bodily injury hazard. Spraying
hydraulic oil can penetrate and
burn skin. Loosen hydraulic
connections very slowly to allow
the oil pressure to dissipate
gradually. Do not allow oil to
squirt or spray.
2 Connect a 0 to 5000 psi / 0 to 350 bar
pressure gauge to the high pressure port on
the pump.
3 Turn the key switch to ground control and pull
out the red Emergency Stop button to the on
position at both the ground and platform
controls.
4 Activate any function using auxiliary power.
Result: The pressure gauge reads 2800 psi
/193 bar, immediately stop. The pump is
good.
Result: The pressure fails to reach 2800 psi
/193 bar, the pump is faulty and will need to
be serviced or replaced.
5 Remove the pressure gauge and install the
hydraulic hose.
How to Re mov e th e Auxiliary Pum p
How to Remove the Auxiliary
Pump
Note: When removing a hose assembly or fitting,
the O-ring (if equipped) on the fitting and/or hose
end must be replaced. All connections must be
torqued to specification during installation. Refer to
Specifications,
Hydraulic Hose and Fitting Torque
Specifications.
1 Tag, disconnect and plug the hydraulic hoses
from the pump.
Bodily injury hazard. Spraying
hydraulic oil can penetrate and
burn skin. Loosen hydraulic
connections very slowly to allow
the oil pressure to dissipate
gradually. Do not allow oil to
squirt or spray.
2 Remove the pump mounting fasteners.
Carefully remove the pump.
Summary of Contents for Genie Z-34/22
Page 63: ...October 2021 Service and Repair Manual Manifolds Part No 1268515GT Z 34 22 Bi Energy 51 ...
Page 89: ...October 2021 Service and Repair Manual 77 Electrical Schematic ANSI CSA from SN Z34F 12066 ...
Page 92: ...Service and Repair Manual October 2021 80 Electrical Schematic ANSI CSA from SN Z34F 12066 ...
Page 97: ...October 2021 Service and Repair Manual 85 PBOX Wiring Diagram ANSI CSA from SN Z3414 9686 ...
Page 103: ...October 2021 Service and Repair Manual 91 Electrical Schematic CE AS from SN Z34F 12066 ...
Page 106: ...Service and Repair Manual October 2021 94 Electrical Schematic CE AS from SN Z34F 12066 ...
Page 114: ...Service and Repair Manual October 2021 102 Power Cable Wiring Diagram from SN Z3414 9686 ...
Page 115: ...October 2021 Service and Repair Manual 103 Drive Contactor Panel Wiring Diagram ...
Page 118: ...Service and Repair Manual October 2021 106 Manifold and Limit Switch Wiring Diagram ...
Page 119: ...October 2021 Service and Repair Manual 107 LVI BCI Option Wiring Diagram ...
Page 122: ...Service and Repair Manual October 2021 110 Charger Interlock Option ...
Page 123: ...October 2021 Service and Repair Manual 111 Engine Wiring Diagram ...
Page 126: ...Service and Repair Manual October 2021 114 Contact Alarm Option from SN Z34F 12066 ...
Page 127: ...October 2021 Service and Repair Manual 115 Fuel Level Sensor Option from SN Z34F 12066 ...
Page 129: ...October 2021 Service and Repair Manual 117 Hydraulic Schematic ...
Page 131: ......