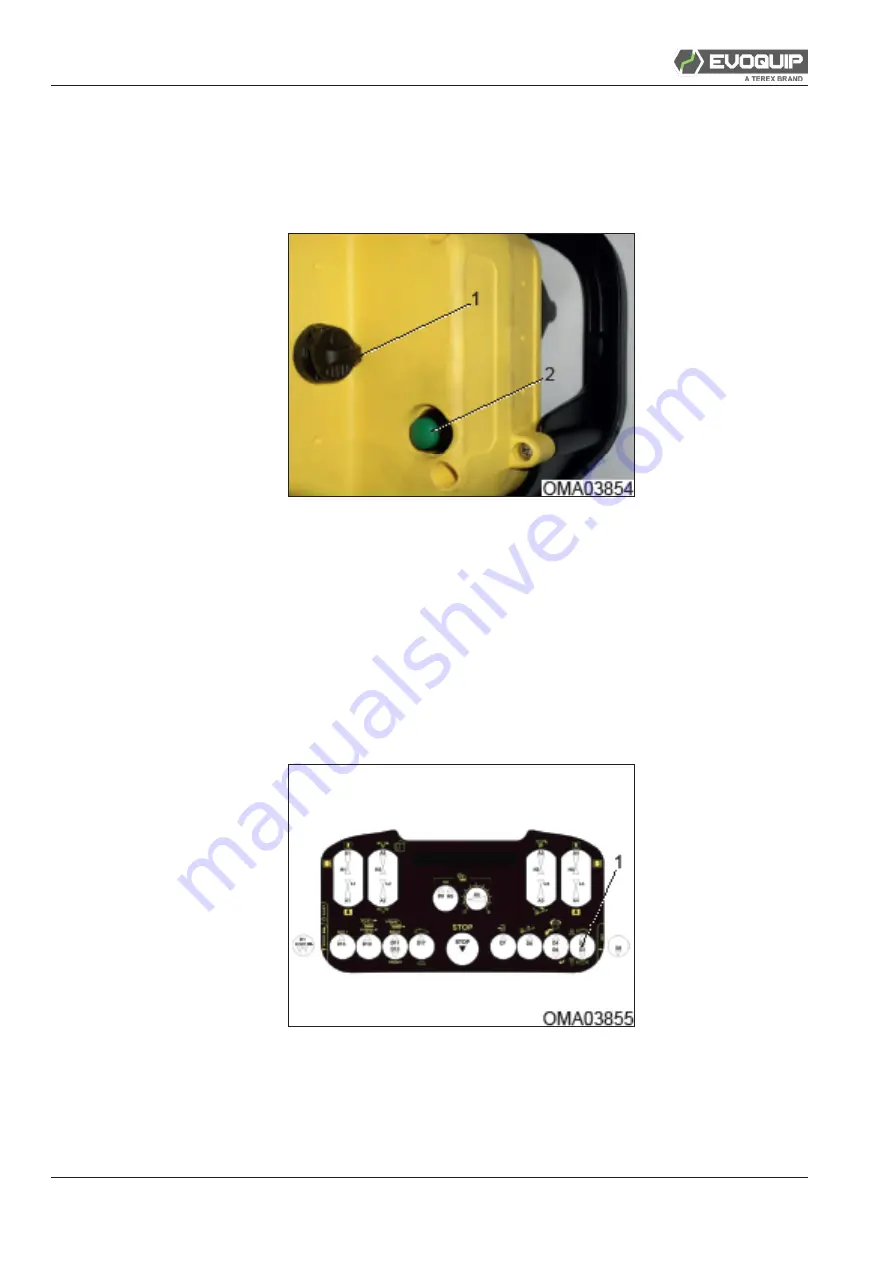
5 Transportation
Operations Manual
Bison 120
20-07-2018
Page 5-6
Revision 2.0
6. Ensure that all function toggle switches are in the off position and that the chamber switch
is in neutral position.
7. Turn the ignition key (Item 1) of the radio control to 1, Reference: Figure 5.3.
»
The LED light on the handset will be flashing at a fast speed which means the handset is not
connected .
Figure 5.3 - Radio Ignition Switch
8. Press button 2 to connect the handset to the reciever, Reference: Figure 5.3.
9. The green LED on the handset will now be flashing slowly and the blue “STATUS” light on
the receiver will be flashing showing a connection.
If a red LED flashes then either:
• The toggle switches are not all in neutral
• The battery needs recharged
10. Press the engine ignition toggle switch (Item 1) forward on the radio control to start the
engine, Reference: Figure 5.4.
Figure 5.4 - Ignition Toggle Switch
11. Use the potentiometer to modify the engine speed (Item 1), Reference: Figure 5.5.
Summary of Contents for Evoquip Bison 120
Page 2: ...EvoQuip 200 Coalisland Road Dungannon Co Tyrone BT71 4DR Telephone 44 0 28 8774 0701...
Page 208: ...Appendix A Operations Manual Bison 120 20 07 2018 Page A 2 Revision 2 0...
Page 219: ...Appendix C Operations Manual Bison 120 20 07 2018 Page C 5 Revision 2 0 c Main Wiring...
Page 220: ...Appendix C Operations Manual Bison 120 20 07 2018 Page C 6 Revision 2 0 d Relay Box...
Page 223: ......