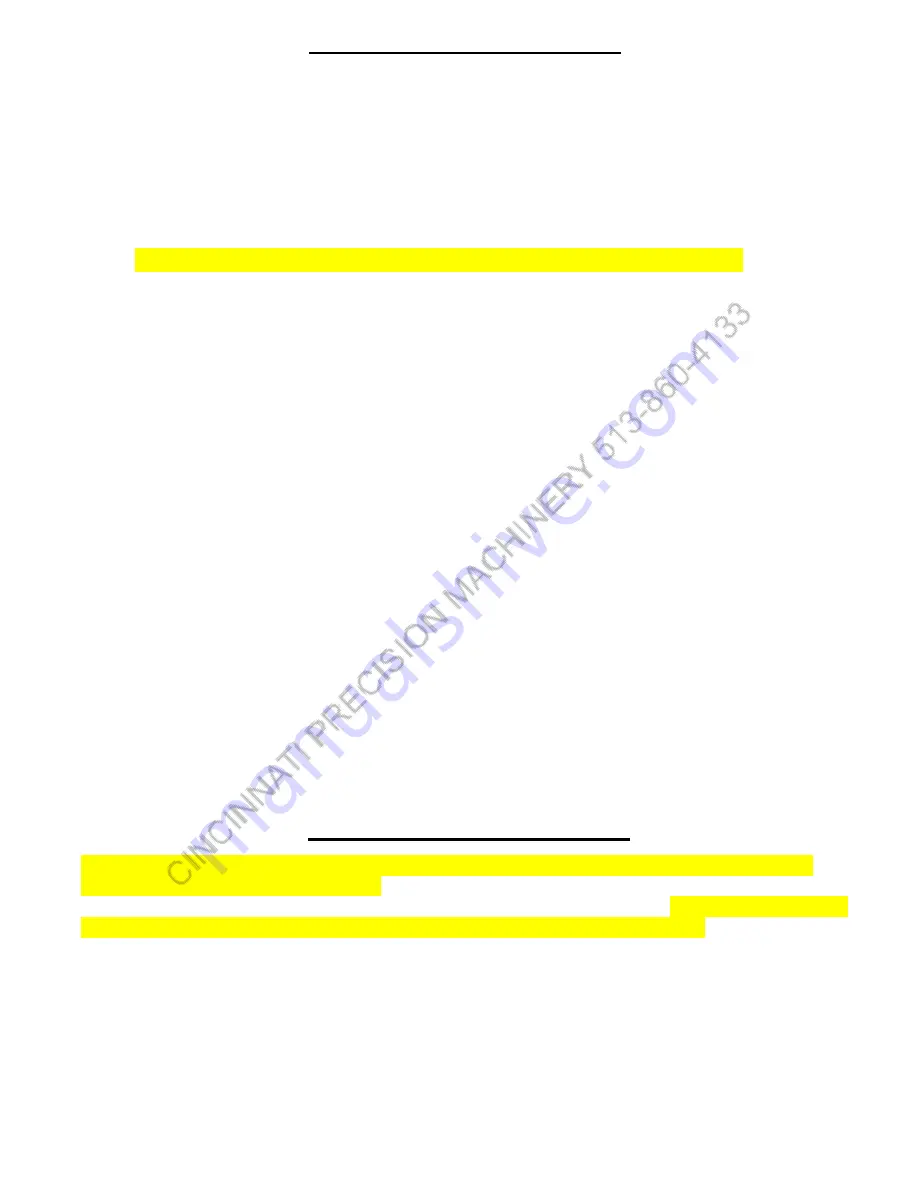
5
BLADE GAP ADJUSTMENT
The factory setting for the gap between the upper and lower blade is .002. This setting is the optimal clearance for
the entire range of material likely to be sheared on this machine. Different materials and thickness may require a
larger or slightly smaller clearance. If you have any specific questions regarding optimal blade gap, please consult
Tennsmith.
To adjust the blade gap of your shear, the turnbuckles (55) are utilized to move the cutter bar down and hold the
position while the blade adjustment is being made. Please note: when checking the blade clearance between the
blades at any particular point across the travel of the bed, check the gap at the point where the upper blade
intersects the lower blade by 1/8” depth.
To start, disconnect the main power connection to the shear.
1.
Loosen the jam nuts (54) that lock the turnbuckle in position.
2.
Move the cutter bar down by tightening each turnbuckle. To avoid putting the cutter bar in a bind, tighten
each turnbuckle evenly. The first checkpoint when verifying or changing the blade gap is 2 inches from the
right side end of the blade facing the machine. Make sure the upper blade intersects the lower blade by
1/8”. Once you have moved the cutter bar into the desired position, use a set of shim feeler gauges to verify
the blade clearance between the two blades. The second checkpoint is the center of the shear, and the last
is 2 inches from the left end of the blades.
3.
To close the gap on the either the left or the right ends of the blade, loosen the table bolts(24) for the
particular end you are adjusting, and loosen the 9/16” adjustment screw (22) located in the front of your
side panel by a ¼ turn. Next tighten the set screw (21) to move the lower blade towards the upper blade.
When you have reached the desired gap verified by your feeler gauge, tighten the adjustment screw (22) to
ensure the proper tension on the set screw. To open the gap, reverse the previous procedure.
4.
After you have reached the desired gap, tighten the table bolts (24) on each side.
5.
The blade gap in the center of the shear is controlled by the adjustment screw (40) located on the backside
of the cutter bar of the shear. To close the gap, tighten the screw in ¼ increments until you have reached
the desired gap.
6.
After you have adjusted the shear gap to the desired settings, move the cutter bar back to its original
settings. This is called the pitch or rake of the blade:
Rake angle settings:
Use a marker to mark the shear bed 2 inches to the from the right side edge of the table. Next, measure over 48
inches from the right side edge of the table and make another mark. Starting at the right hand side (facing the
machine) at the designated mark on the table, rotate the turnbuckle (55) until the distance between the top and
bottom blades is approximately 3/8 of an inch. At the opposing end, repeat the procedure allowing 1 ¾ inches
clearance between the upper and lower blades. After you have the desired clearance between the upper and lower
blades slightly adjust the turnbuckles so that they have an equal amount of tension. That is, if one turnbuckle has
more play or lost motion in it than the other, it should be readjusted accordingly. Once the rake has been set and
equal tension verified between the turnbuckles, retighten the jam nuts (54) and lock the turnbuckles in place.
HOLD-DOWN ADJUSTMENT
CAUTION: THIS SHEAR SHOULD NOT BE OPERATED WITHOUT THE HOLDDOWN IN
PLACE AND PROPERLY ALIGNED.
The hold-down (3) is designed to engage the material before the
blades yet allow only minimal clearance between the guard’s feet and the table surface.
The gap between the
hold-down feet and table surface should never be above 3/16” of an inch
.
The gap between
the hold-down and the table is controlled by turning the nut on the hold-down studs (10). Clockwise rotation will
increase clearance; counter clockwise turns will decrease the gap.
The guard should be held snug against the milled pads on the cutter bar and not feel loose. You must be careful,
however, that the hold-down bolts (13) are not so tight as to bind the guard when the cutter bar is in the down
position. Properly aligned, the bolts will snug but still allow rotation of the hold-down bolt washers (14). At the rear
of the cutter bar you will find two tapped holes wherein hold-down jam screws (45) are located. Once you have
applied proper tension to the hold-down bolts, tighten the jam screws to lock alignment in place. (Note: The milled
pads on the front and rear of the hold-down should be greased periodically to maintain proper action.