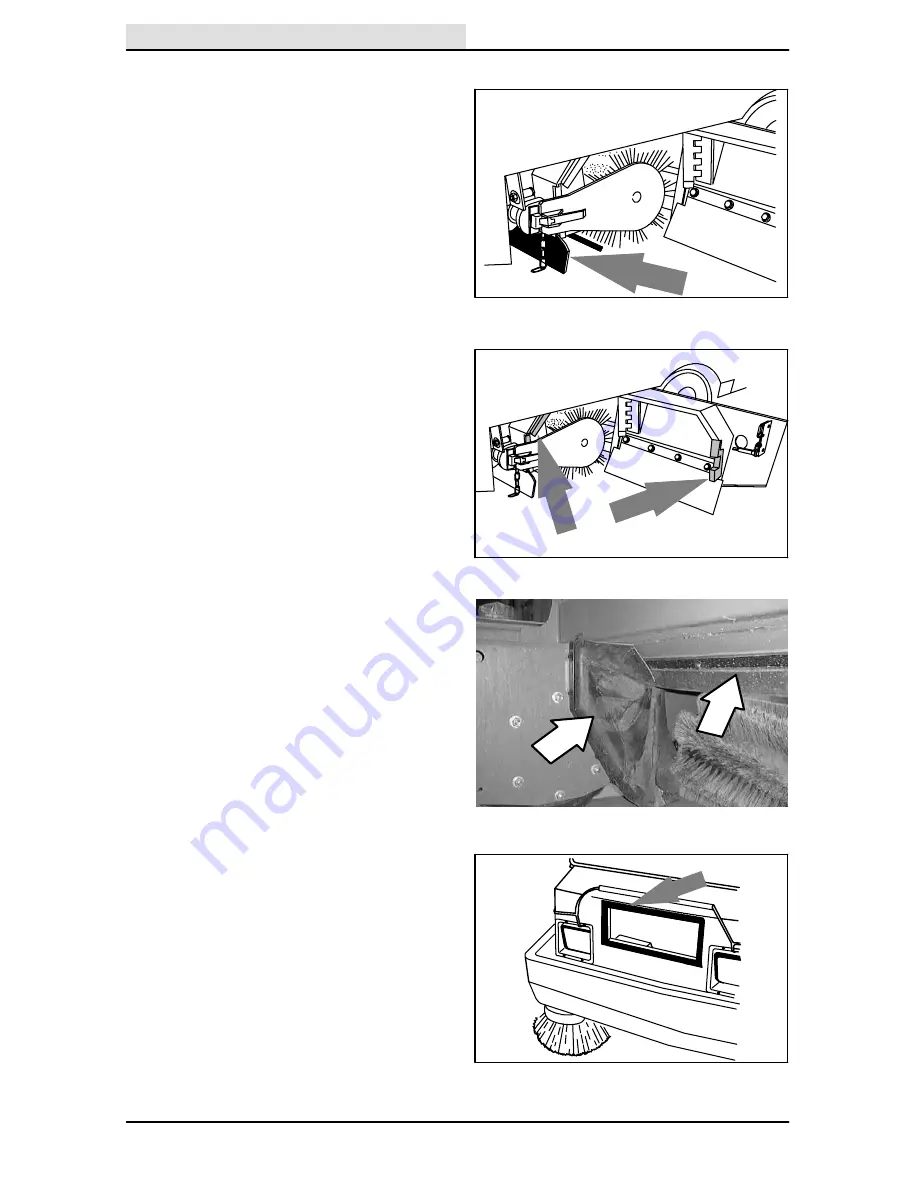
MAINTENANCE
6550E 330359 (2--99)
64
REAR SKIRTS
The two rear skirts are located on the bottom rear
of the main brush compartment. The vertical skirt
should clear the floor up to 5 mm (0.25 in) in dusty
conditions, and touch the floor otherwise. The
recirculation skirt is self-adjusting.
Check the skirts for wear or damage and
adjustment daily.
BRUSH DOOR SEALS
The brush door seals are located on both main
brush doors and on corresponding portions of the
main frame.
Check the seals for wear or damage every
100 hours of operation.
HOPPER SEALS
The hopper seals are located on the front and side
portions of the machine frame that contact the
hopper.
Check the seals for wear or damage every
100 hours of operation.
HOPPER INSPECTION DOOR SEAL
The hopper inspection door seal is located on the
hopper and seals the front of the debris hopper.
Check the seal for wear or damage every
100 hours of operation.
08021
08022
08024