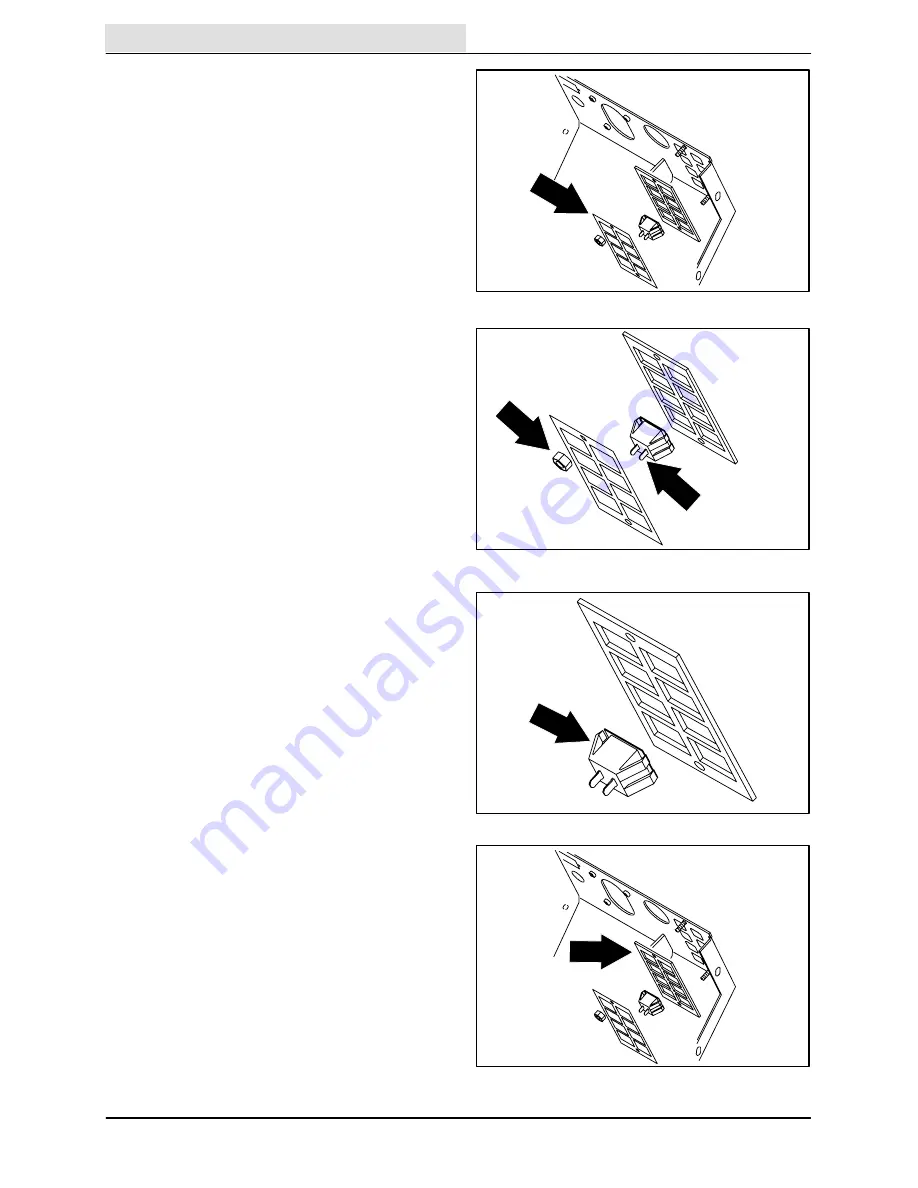
ELECTRICAL
4-14
6400E MM434 (7--99)
3. Locate the indicator light panel mount plate
next to the power steering orbital control.
4. Remove the two nyloc nuts holding the
mount plate to the instrument panel. Pull the
mount plate back away from the instrument
panel.
5. Unplug the two wires leading to the light that
needs to be changed.
6. Squeeze the sides of the light and push the
light out of the mount plate.
7. Install the new light in the mount plate. Snap
in place.
8. Reconnect the wires to the new light. See
schematic in this section.
9. Position the mount plate back on the
instrument panel. Reinstall the two nyloc
nuts and tighten.
Summary of Contents for 6400E
Page 1: ...MM434 Rev 02 11 01 Service Manual 6400E ...
Page 4: ...GENERAL INFORMATION 1 2 6400E MM434 11 01 ...
Page 18: ...GENERAL INFORMATION 1 16 6400E MM434 7 99 ...
Page 20: ...CHASSIS 2 2 6400E MM434 7 99 ...
Page 41: ......
Page 42: ......
Page 43: ......
Page 44: ......
Page 45: ......
Page 46: ......
Page 47: ......
Page 48: ......
Page 49: ......
Page 50: ......
Page 51: ......
Page 52: ......
Page 53: ......
Page 54: ......
Page 55: ......
Page 56: ......
Page 57: ......
Page 58: ......
Page 59: ......
Page 60: ......
Page 61: ......
Page 62: ......
Page 64: ...SWEEPING 3 2 6400E MM434 7 99 ...
Page 142: ...ELECTRICAL 4 2 6400E MM434 7 99 ...
Page 176: ...ELECTRICAL 4 36 6400E MM434 11 01 ELECTRICAL SCHEMATIC 1 2 3 4 ...
Page 177: ...ELECTRICAL 4 37 6400E MM434 11 01 ELECTRICAL SCHEMATIC 1 2 3 4 ...
Page 179: ...ELECTRICAL 4 39 6400E MM434 11 01 CONTROL PANEL CABLE GROUP ...
Page 180: ...ELECTRICAL 4 40 6400E MM434 11 01 CONTROL PANEL WIRE GROUP ...
Page 182: ...ELECTRICAL 4 42 6400E MM434 11 01 WIRE HARNESS GROUP ...
Page 188: ...ELECTRICAL 4 48 6400E MM434 7 99 ...
Page 190: ...HYDRAULICS 5 2 6400E MM434 7 99 ...
Page 226: ...HYDRAULICS 5 38 6400E MM434 11 01 HYDRAULIC SCHEMATIC ELECTRIC ...
Page 243: ......
Page 244: ......
Page 245: ......
Page 246: ......
Page 247: ......
Page 248: ......
Page 249: ......
Page 250: ......
Page 251: ......
Page 252: ......
Page 253: ......
Page 254: ......
Page 255: ......
Page 256: ......
Page 257: ......
Page 258: ......
Page 259: ......
Page 260: ......
Page 261: ......
Page 262: ......
Page 263: ......
Page 264: ......
Page 265: ......
Page 266: ......
Page 267: ......
Page 268: ......
Page 269: ......
Page 270: ......
Page 271: ......
Page 272: ......
Page 273: ......
Page 274: ......
Page 275: ......
Page 276: ......
Page 277: ......
Page 278: ......
Page 279: ......
Page 280: ......
Page 281: ......
Page 282: ......
Page 283: ......
Page 284: ......
Page 285: ......
Page 286: ......
Page 287: ......
Page 288: ......
Page 289: ......
Page 290: ......