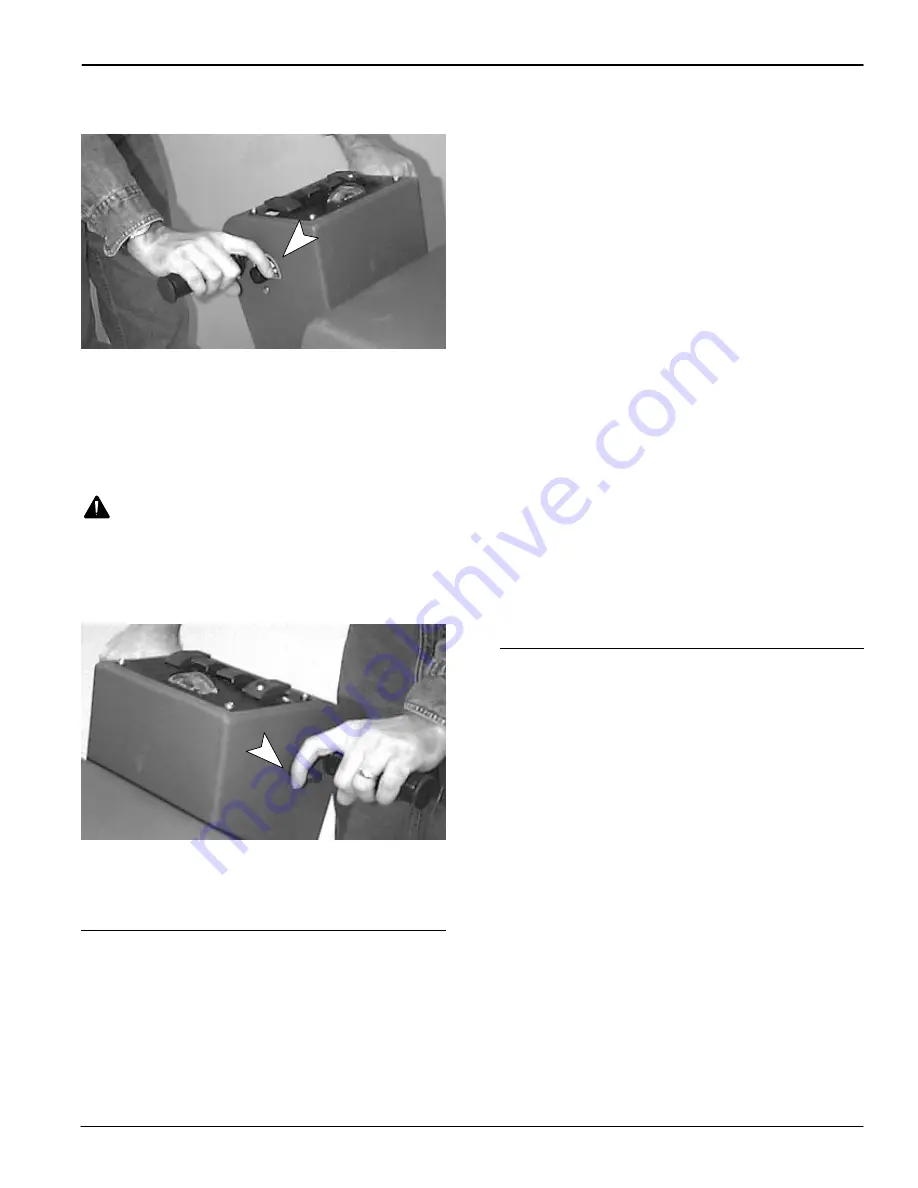
OPERATION
Tennant 1500 (05–99)
7
4.
Before you begin cleaning, turn speed control
knob to slowest speed (Figure 7).
FIG. 7
5.
To begin cleaning, rotate control grips completely
forward and gradually turn speed control knob to
desired cleaning speed (Figure 7).
For optimum cleaning results, operate at a cleaning
speed of 15 m (50 ft) per minute for deep cleaning
and 30 m (100 ft) per minute for interim cleaning.
WARNING: Flammable materials or reactive
metals can cause explosion or fire. Do not pick
up.
6.
To stop machine, release control grips.
7.
To operate machine in reverse, simply pull reverse
switch backwards one speed (Figure 8).
FIG. 8
8.
After cleaning carpets, allow sufficient time for
carpet to dry. Use a carpet blower to reduce drying
time.
WHILE OPERATING MACHINE
1.
Periodically check for foam buildup in recovery
tank
(look through clear lid). If excessive foam
buildup begins to develop, pour a recommended
foam control solution into recovery tank.
ATTENTION: Do not allow foam or water to enter
float shut-off screen, vacuum motor damage will
result. Foam will not activate float shut-off
screen. Vacuum damage due to foam or water is
not covered by warranty.
2.
Always operate at a slower speed when cleaning
around walls or obstacles.
3.
Always reduce speed to maintain control when
turning machine.
4.
Overlap each pass by 50 mm (2 in).
5.
Before reaching end of cleaning path, turn off
pump switch and continue to drive machine
forward to extract solution.
6.
Periodically check battery meter discharge level.
When needle drops to the red zone, recharge
batteries.
ATTENTION: Do not continue to run machine
when battery meter needle is in the red zone,
battery damage will result.
7.
While cleaning, view clear hose gallon marker for
remaining cleaning solution. Each mark on hose
indicates 19 L (5 gal).
8.
When solution tank runs dry, turn off pump and
vacuum switches, raise brush, and transport
machine to draining area
(See Draining Tanks).
9.
If the cleaning path leaves streaks, spray tip
cleaning is required (See Weekly Maintenance)
.
CIRCUIT BREAKERS
The machine is equipped with two resetable circuit
breakers, Main (15A) and Vacuum/Drive (60A), to
protect machine from damage. If a circuit breaker
should trip, determine cause and reset breaker by
depressing circuit breaker button.
The main and vacuum/drive circuit breakers are
designed to stop current flow by manually pulling out
the circuit breaker button. Pull out the main circuit
button to protect you from electric shock when
servicing machine, or when machine is left
unattended. Pull out vacuum/drive circuit breaker
button to keep machine stationary while performing
specific maintenance procedures. Circuit breakers are
located below control console (Figure 9).