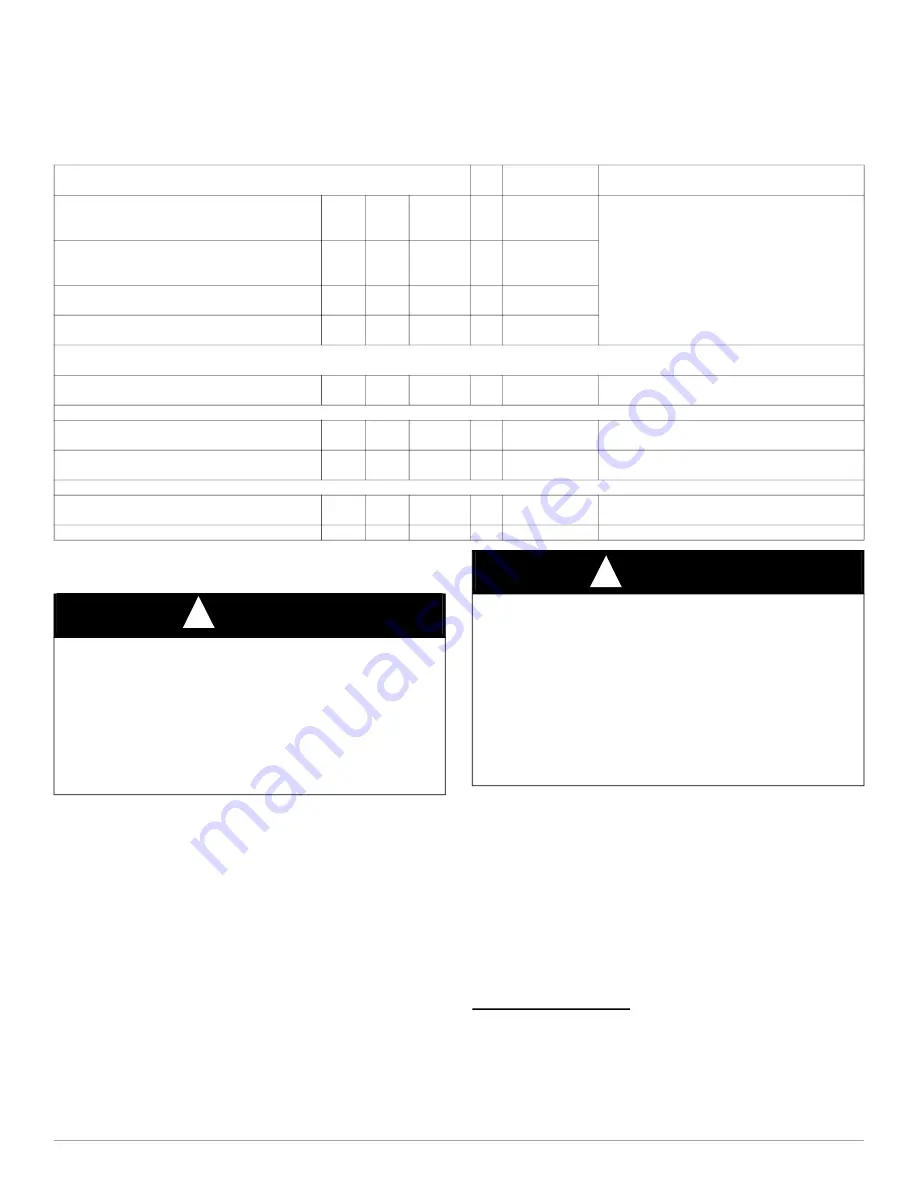
F97CMN and G97CMN: Installation, Start-up, Operating and Service and Maintenance Instructions
Manufacturer reserves the right to change, at any time, specifications and designs without notice and without obligations.
49
Example 2
A direct-vent 60,000 BTUH furnace installed at 2100 ft. (640M). Venting system includes
FOR EACH PIPE:
100 feet (30 M) of
vent pipe, 95 feet (29 M) of combustion air inlet pipe, (3) 90º long-radius elbows, and a polypropylene concentric vent kit. Also
includes 20 feet (6.1 M) of flexible polypropylene vent pipe, included within the 100 feet (30 M) of vent pipe.
VERIFY FROM POLYPROPYLENE VENT MANUFACTURER’S INSTRUCTIONS for the multiplier correction for flexible vent pipe.
Can this application use 60mm o.d. (2”) polypropylene vent piping? If not, what size piping can be used?
START-UP, ADJUSTMENT, AND SAFETY
CHECK
General
1. Furnace must have a 115-v power supply properly connected and
grounded.
NOTE:
Proper polarity must be maintained for 115-v wiring. Control
status indicator light flashes code 10 and furnace does not operate if
polarity is incorrect or if furnace is not grounded.
2. Thermostat wire connections at terminals R, W/W1, G, and Y/Y2
must be made at 24-v terminal block on furnace control. See
communicating wall control instructions for proper wiring of
communicating controls.
3. Natural gas service pressure must not exceed 0.5 psig (14- in. w.c.,
350 Pa), but must be no less than 0.16 psig (4.5-in. w.c., 1125 Pa).
4. Blower door must be in place to complete 115-v electrical circuit
and supply power to the furnace components.
Before operating furnace, check flame rollout manual reset switch for
continuity. If necessary, press button to reset switch.
EAC-1 terminal is energized whenever blower operates, HUM terminal
is only energized when blower is energized in heating.
Setup Switches
There are four (4) sets of setup switches on the furnace control board.
These switches configure the furnace for correct application
requirement. They also select the airflow settings for Air Conditioning
and Continuous Fan airflows.
The Setup Switch locations are shown and described on
. The
setup switches are also shown on the unit wiring label.
Setup Switches (SW1)
The furnace control has eight (8) setup switches that may be set to meet
the application requirements. Refer to
section for setup switch configurations. To set these setup switches for
the appropriate requirement:
1. Remove blower door.
2. Locate setup switches on furnace control.
Measure the required linear length of
RIGID
air inlet and vent pipe; insert the
longest of the two here: 100 ft. Of rigid pipe - 20 ft. Of flexible pipe
=
80 ft.
(24 M)
Use length of the longer of the vent
or air inlet piping system
Add equiv length of (3) 90º long-radius elbows
(use the highest number of elbows for either the
vent or inlet pipe)
3
x
5 ft.
(1.5 M)
=
15 ft.
(4.6 M)
Example from polypropylene vent
manufacturer’s instructions, Verify from vent
manufacturer’s instructions.
Add equiv length of 45º long-radius elbows
(use the highest number of elbows for either the
vent or inlet pipe)
0
x
=
0 ft.
(0 M)
Add equiv length of factory concentric vent term
9
x
3.3 ft
(0.9 M)
=
30 ft.
(9 M)
Add correction for flexible vent pipe, if any
2*
x
20 ft.
(6.1 M)
=
40 ft.
(12.2 M)
*
VERIFY FROM VENT MANUFACTURER’S INSTRUCTIONS; For example only, assume 1 meter of flexible 60mm (2”) or 80mm (3”) polypropylene
pipe equals 2.0 meters (6.5 ft.) of PVC/ABS pipe.
Total Equivalent Vent Length (TEVL)
165 ft.
(50 M)
Add all of the above lines
Maximum Equivalent Vent Length (MEVL)
95 ft.
(29 M)
Is TEVL less than MEVL?
NO
Therefore, 60mm (2”) pipe may NOT be used;
try 80mm (3”)
Maximum Equivalent Vent Length (MEVL)
185 ft.
(57 M)
Is TEVL less than MEVL?
YES
Therefore, 80mm (3”) pipe MAY be used
NOTICE
!
Important Installation and Start-up Procedures
Failure to follow this procedure may result in a nuisance smoke or odor
complaint.
The manifold pressure, gas rate by meter clocking, temperature rise and
operation must be checked after installation. Minor smoke and odor
may be present temporarily after start-up from the manufacturing
process. Some occupants are more sensitive to this minor smoke and
odor. It is recommended that doors and windows be open during the
first heat cycle.
CAUTION
!
UNIT OPERATION HAZARD
Failure to follow this caution may result in intermittent unit operation
or performance dissatisfaction.
These furnaces are equipped with a manual reset limit switch in burner
assembly. This switch opens and shuts off power to the gas valve if an
overheat condition (flame rollout) occurs in the burner
assembly/enclosure. Correct inadequate combustion-air supply,
improper gas pressure setting, improper burner or gas orifice
positioning, or improper venting condition before resetting switch. DO
NOT jumper this switch.