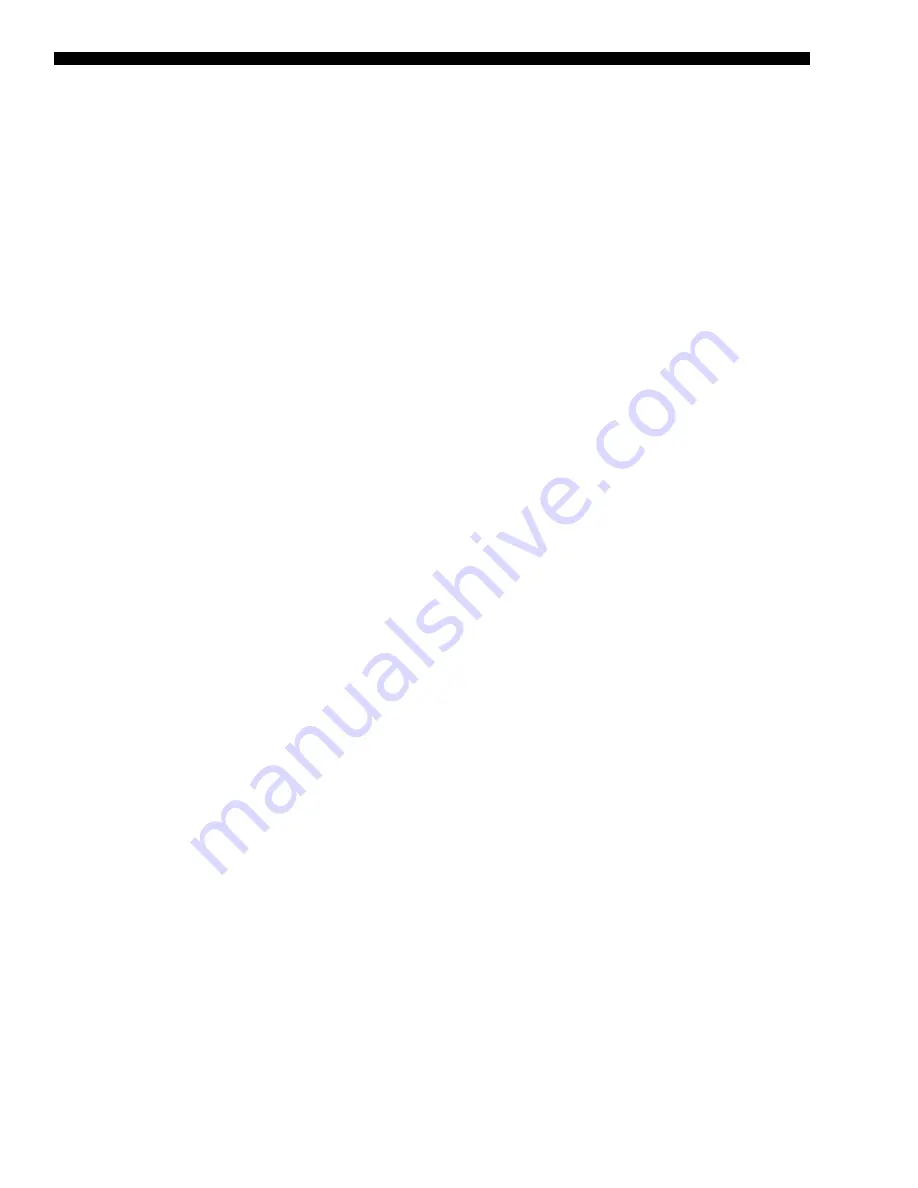
TEMPMASTER
76
FORM TPM3-EG1 (518)
2.
Condenser Coil:
Condenser coils shall be all aluminum micro-channel coils or
seamless copper tubes, arranged in staggered rows, mechanically expanded into
the aluminum fins. Coils are configured in a V-bank configuration, with individual flat
coils rotated from the vertical plane for protection from hail damage for each con-
densing circuit. Condensing coils shall have a subcooler for more efficient, stable
operation.
3.
Compressors:
Units shall use industrial-duty hermetic scroll compressors, piped
and charged with oil and POE R-410A refrigerant. Compressors shall have an en-
larged liquid carrying capacity to withstand rugged operating conditions. Compres
-
sor frame shall be cast iron, with cast iron fixed and orbiting scrolls. Each compres
-
sor shall feature a solid state protection module, designed to protect the compressor
from over-temperature and over-current conditions. Compressors shall be vibration-
isolated from the unit and installed in an easily accessible area of the unit. All com-
pressor-to-pipe connections shall be brazed to minimize potential for leaks. Each
compressor shall include a replaceable suction screen, discharge line check valve,
and oil sight glass.
4.
Compressor Capacity Modulation:
Unit shall include six compressors of varying
size to provide 14–100% of cooling during normal operation. The compressor se-
quence of operation shall reduce typical temperature change to less than 2.0°F at
the unit discharge at full design airflow. Unit shall not require hot gas bypass and the
inherent energy usage it requires to properly operate the unit. Upon entering cool
-
ing mode from other modes, the unit controller will estimate the cooling requirement
and match it closely to the capacity in order to reduce the time required to satisfy
the cooling requirements. After the initial calculation, the unit controller will add or
reduce stage(s) as necessary to establish a balance between the unit capacity and
the space cooling load.
5.
Low Ambient:
Compressors shall operate down to 0.0°F [optional] by monitor-
ing the refrigeration system discharge pressure and adjusting condenser airflow
to maintain the proper head pressure to protect compressor operation. Refrigerant
pressure transducers shall be included and provide the discharge pressure on the
single package unit control display.
6.
In-Line Liquid Line Driers [Replaceable Core Liquid Line Driers]:
Refrigerant
piping includes check valves, thermal expansion valves with replaceable thermo-
static elements, high and low pressure switches, and anti-recycling timing device to
prevent compressor restart for 5 minutes after shutdown.
7.
Condenser Wire Grill [Optional Louvered Condenser Enclosure or No Enclo-
sure]:
The condenser section shall be enclosed by a wire grill [louvered or none]
condenser enclosure on the three exposed sides. Paint finish shall match the color
and salt spray specifications of the unit exterior.
8.
Compressor Sound Treatment [Optional]:
Compressor sound blankets shall be
provided to attenuate radiated sound from the compressors.
9.
Service Valves [Optional]:
Liquid, suction, and discharge service valves shall be
included to provide a means of isolating the refrigerant charge in the system so that
the refrigeration system may be serviced without removing the charge of the unit.
Guide Specifications (Cont'd)