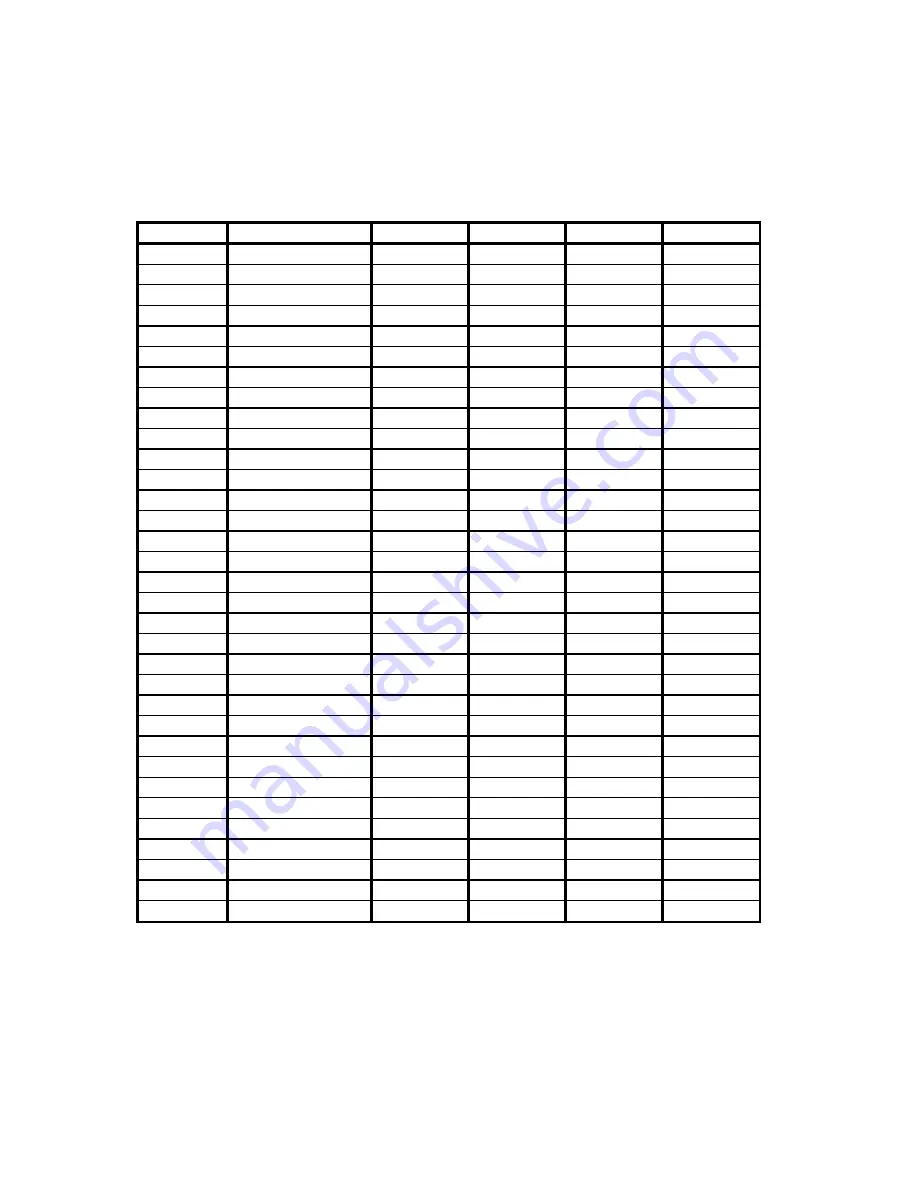
TECUMSEH POWERED BELT DRIVE BLOWER PARTS
SCHEMATIC REFERENCE 2003
BD18-T-5.5 BD21-T-5.5 BD24-T-5.5 BD 27-T-10
ITEM #
DISCRIPTION
PART #
PART #
PART #
PART #
1
FRONT GRILL
230-032
230-029
230-030
230-031
1A
GRILL EMBLEM
400-028
400-029
400-030
400-031
1B
NEOWASHER
120-004
120-004
120-004
120-004
1C
GRILL BOLT
100-002
100-002
100-002
100-002
2
BLADE
260-075
260-019
260-026
260-031
2A
BUSHING
160-018
160-018
160-018
160-019
3
BELT
180-011
180-003
180-001
180-002
4
TOP PULLEY
160-030
160-030
160-002
160-003
5
SHROUD
705-001
705-002
705-003
705-004
5A
FRONT TRIM
410-002
410-003
410-004
410-005
6
ENGINE PULLEY
160-030
160-029
160-029
160-004
7
REAR GRILL
230-023
230-021
230-022
230-024
7A
NYLOCK
130-003
130-003
130-003
130-003
7B
NEOWASHER
120-004
120-004
120-004
120-004
7C
GRILL BOLT
100-002
100-002
100-002
100-002
8
BEARING ASSY
600-069C
600-069C
600-068D
600-071
8A
SHAFT KEY
300-009
300-009
300-009
300-009
9
FRONT FOOT
580-006
580-006
580-006
580-006
10
FRAME
600-190
600-190
600-191
600-041
11
GAS TANK
200-002
200-002
200-002
200-002
12
ROCKER LTCH
600-159
600-159
600-159
600-159
13
HANDLE ASSY
600-200
600-200
600-201
600-188
14
NYLOCK BSHNG
120-002
120-002
120-002
120-002
15A
LEFT LEG
600-166
600-155
600-164
600-031
15B
RIGHT LEG
600-167
600-154
600-165
600-017
16
ENGINE
350-015
350-015
350-015
350-002
16A
MUFFLER
190-035
190-035
190-035
190-001
17
STEP BAR
600-180
600-049
600-049
600-054
18
STEP SPRING
300-019
300-019
300-019
300-019
19
REAR SPR. ASSY
600-001
600-001
600-001
600-001
20
REAR FOOT PAD
580-001
580-001
580-001
580-001
21
WHEEL BOLT
100-002
100-002
100-002
100-002
22
WHEEL
240-003
240-003
240-003
240-003
5/30/2003
8.3