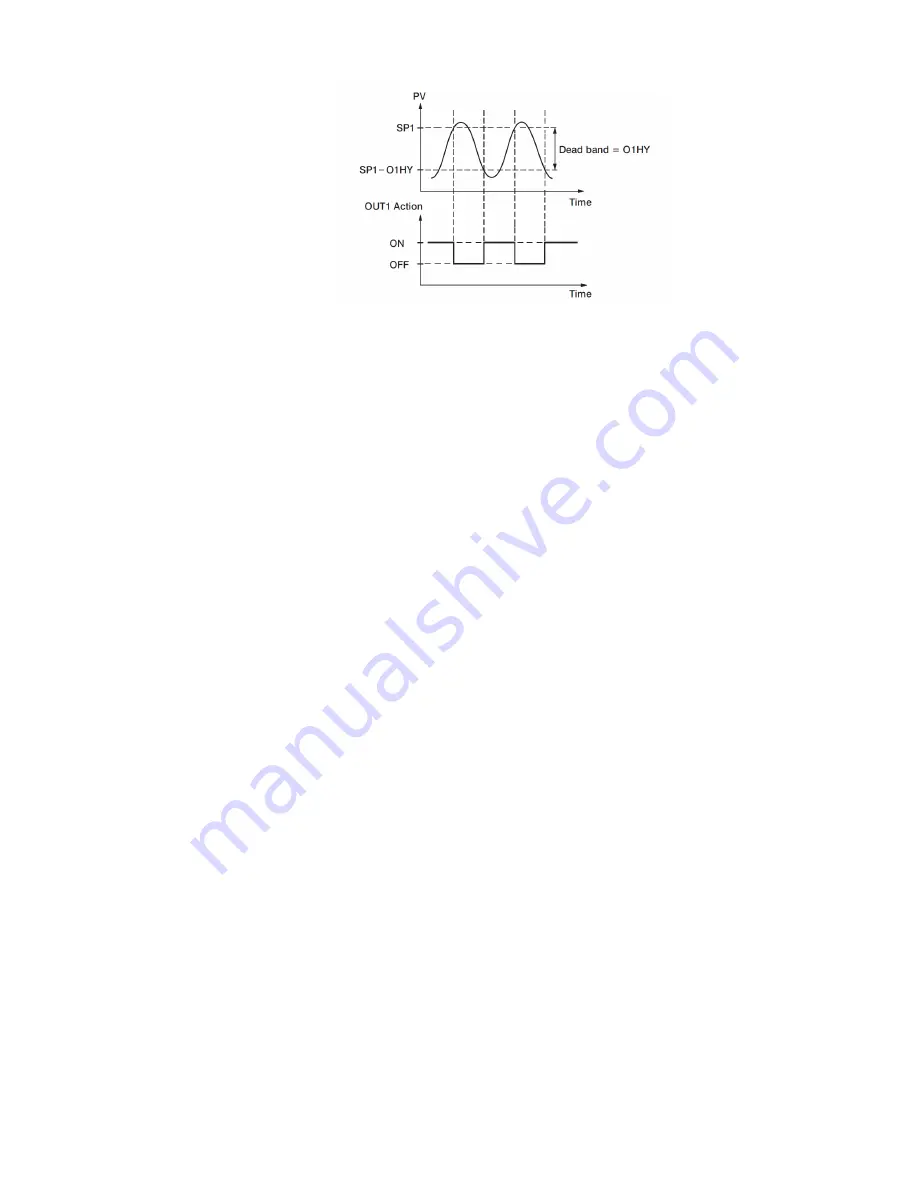
Page
25
of
44
ON-OFF control may cause excessive process oscillations even if the hysteresis is set to the smallest value.
If ON-OFF control is set (i.e. PB = 0), TI, TD, CYC1, OFST, CYC2, CPB, DB will no longer be applicable and
will be hidden. Auto-Tuning and Bumpless transfer will also be unavailable.
3.3.2
Heat only P or PD Control
Select REVR for OUT1, set TI = 0, OFST is used to adjust the control offset (manual reset).If
PB
≠
0 then O1HY will be hidden.
OFST Function:
OFST is measured in % with a range of 0 - 100.0 %. When the process is stable, let’s say
the process value is lower than the set point by 5°C. Let’s also say that 20 is used for the PB setting. In this
example, 5°C is 25% of the proportional band (PB).
By increasing the OFST value by 25%, the control output will adjust itself, and the process value will
eventually coincide with the set point.
When using Proportional (P) control (TI = 0), Auto-Tuning will be unavailable. Refer to “manual tuning "
section for the adjustment of PB and TD. Manual reset (OFST) is usually not practical because the load may
change from time to time; meaning the OFST setting would need to be constantly adjusted. PID control can
avoid this problem.
3.3.3
Heat only PID Control
Select REVR for OUT1. PB and TI should not be zero. Perform Auto-Tuning for initial
startup, or set PB, TI and TD using historical values. If the control result is not satisfactory, use manual or
Auto-Tuning to improve the control performance. The unit contains a PID and Fuzzy algorithm to achieve the
set point with a very small overshoot and very quick response to the process if it is properly tuned.
3.3.4
Cool only Control
ON-OFF control, P (PD) control and PID control can be used for cooling control. Set OUT1
to DIRT (direct action). The other functions for cooling only are ON-OFF control, cool only P (PD) control and
cool only PID control are same as for heating, except that the output variable (and action) is reversed.
NOTE:
ON-OFF control may result in excessive overshoot and undershoot problems in the process. P (or
PD) control will result in a deviation of the process value from the set point. It is recommended to use PID
control for Heat-Cool control when able to produce a stable and zero offset process value.