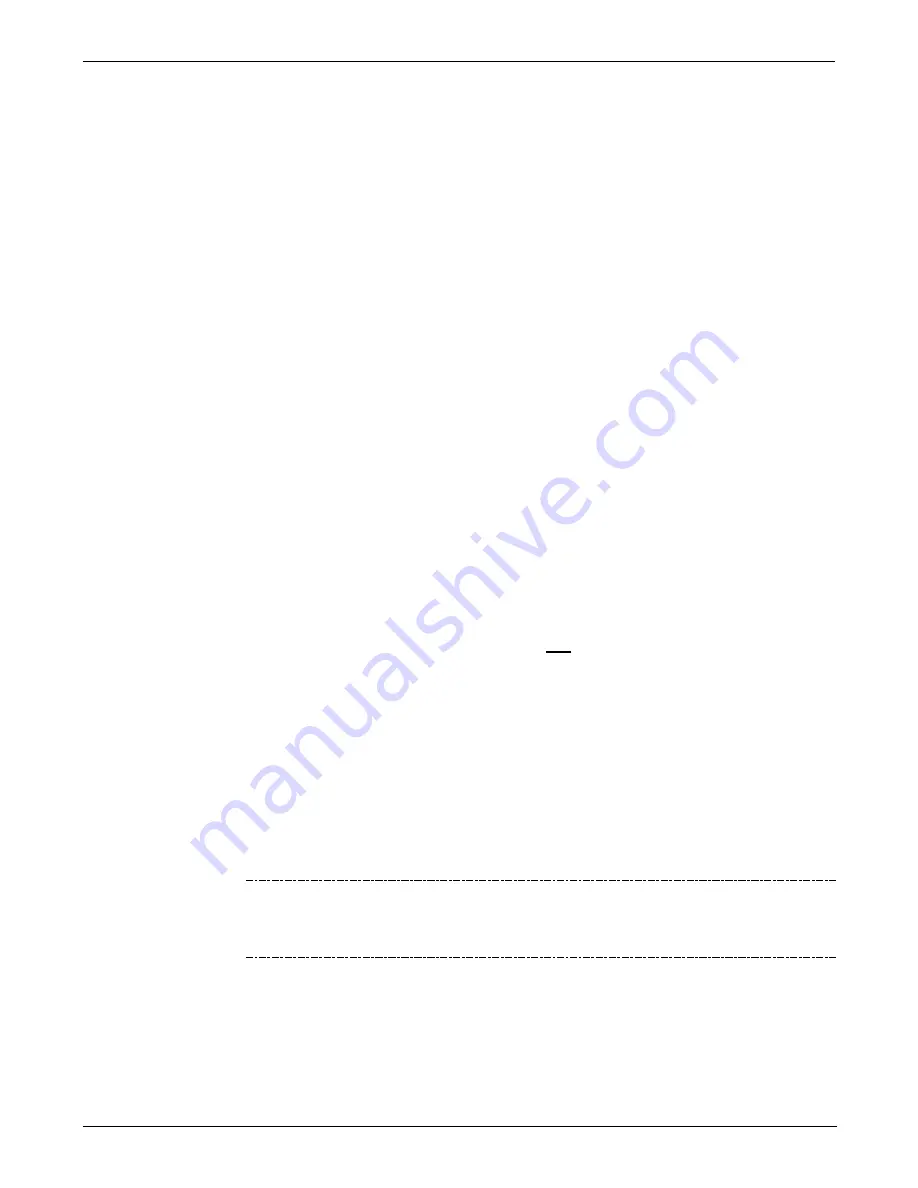
Teledyne API - Model T200H/T200M Operation Manual
Troubleshooting & Service
237
•
A dirty reaction cell can cause high AutoZero values. Clean the reaction cell
according to Section 6.3.5.
•
Finally, a high
HVPS
voltage value may cause excess background noise and a high
AZERO
value. The HVPS value changes from analyzer to analyzer and could show
nominal values between 450 and 800 V. Check the low-level hardware calibration
of the preamplifier board and, if necessary, recalibrate exactly as described in
Section 13 in order to minimize the
HVPS
.
7.5. SUBSYSTEM CHECKOUT
The preceding sections of this manual discussed a variety of methods for identifying
possible sources of failures or performance problems within the analyzer. In most cases
this included a list of possible causes and, in some cases, quick solutions or at least a
pointer to the appropriate sections describing them. This section describes how to
determine if a certain component or subsystem is actually the cause of the problem being
investigated.
7.5.1. SIMPLE LEAK CHECK USING VACUUM AND PUMP
Leaks are the most common cause of analyzer malfunction. This section presents a
simple leak check, whereas Section 7.5.2 details a more thorough procedure. The
method described here is easy, fast and detects, but does not locate, most leaks. It also
verifies the sample pump condition.
•
Turn the analyzer ON, and allow at least 30 minutes for flows to stabilize.
•
Cap the sample inlet port (cap must be wrench-tight).
•
After several minutes, when the pressures have stabilized, the SAMP (sample
pressure) and the RCEL (vacuum pressure) readings.
•
If both readings are equal to within 10% and less than 10 in-Hg-A, the instrument is
free of large leaks. It is still possible that the instrument has minor leaks.
•
If both readings are < 10 in-Hg-A, the pump is in good condition. A new pump will
create a pressure reading of about 4 in-Hg-A (at sea level).
7.5.2. DETAILED LEAK CHECK USING PRESSURE
If a leak cannot be located by the above procedure, obtain a leak checker that contains a
small pump, shut-off valve, and pressure gauge to create both over-pressure and
vacuum. Alternatively, a tank of pressurized gas, with the two stage regulator adjusted
to ≤ 15 psi, a shutoff valve and pressure gauge may be used.
Note
Once tube fittings have been wetted with soap solution under a pressurized
system, do not apply or re-apply vacuum as this will cause soap solution to be
sucked into the instrument, contaminating inside surfaces. Do not exceed 15 psi
when pressurizing the system.
•
Turn OFF power to the instrument and remove the instrument cover.
•
Install a leak checker or a tank of gas (compressed, oil-free air or nitrogen) as
described above on the sample inlet at the rear panel.
•
Disconnect the pump tubing on the outside rear panel and cap the pump port. If
zero/span valves are installed, disconnect the tubing from the zero and span gas
07270D DCN7141