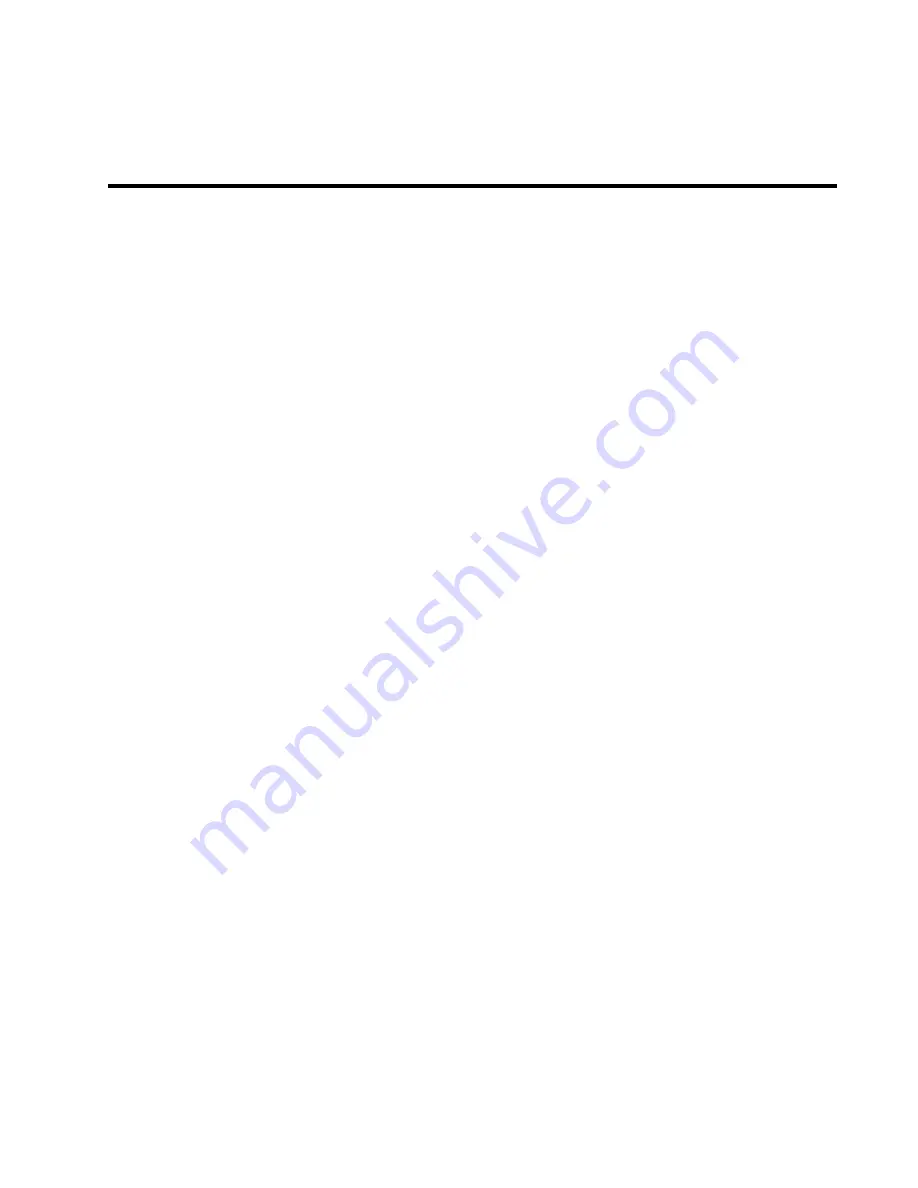
21
Chapter 5: Theory of Operation
Scientific CMOS, aka sCMOS, is a recent development in image sensor technology. The
primary advantage provided by sCMOS sensors is high frame rates, even with very large
pixel counts, while still operating with very low electronic noise. This largely eliminates
the speed-resolution-noise trade off inherent in CCD sensors.
5.1
CMOS Image Sensor Structure
A major difference between traditional CCD sensors and CMOS sensors is the location
where charge-to-voltage conversion of accumulated photoelectrons takes place. CCD
sensors transfer the pixels accumulated signal in charge packets in “bucket brigade”
fashion across the sensor to a common output node where charge is converted to a
voltage. The voltage is then sampled using off-chip Analog-to-Digital Converters (ADC)
and transferred to the PC as digital grey values.
While providing excellent quantitative photometry and very high image quality, the
large number of transfers and sequential digitization of pixels results in low frame rates.
This speed penalty increases with the number of pixels to be digitized.
CMOS sensors leverage many of the same analog signal concepts used in CCDs, but
places the output node circuitry inside each pixel. This eliminates the charge transfer
process. To read the signal from a given row, the accumulated charge is converted to a
voltage inside the pixel, then each pixel in the row is connected to the appropriate
column voltage bus, where the on--chip ADCs covert the voltages to an 11-bit or 12- bit
grey value. (Thus far, the on-chip ADCs available on CMOS sensors have limited
dynamic range.)
The parallel digitization of all pixels in a row provides CMOS devices with a tremendous
speed advantage. Imagine a CCD with 1200 x 1200 pixels and each pixel's voltage is
measured in 1
sec. To read a single row, 1200 voltage measurements are performed in
serial fashion taking slightly longer than 2 ms, and when repeated for 1200 rows, the
entire image takes over four seconds to be digitized.
On a CMOS device, the entire 1200 voltage conversions needed to digitize a row
happen in parallel. The sensor in the Kuro sCMOS camera takes parallelism even further
by dividing the sensor into two halves, so that two rows of 1200 pixels can be measured
at the same time. If the time to digitize a pixel remains at 1
s, the time to read the entire
frame is now approximately 1 ms.
In practice, the time saving is split between faster frame rates and slowing the rate of
pixel measurement to reduce electronic noise. For example, if the time to measure a
pixel was increased to 10
sec to lower noise, the image sensor can still be read in
10 ms, for a maximum 100 fps.
Of course, there are many challenges to obtaining the same analog performance from
each of the Kuro's 1.4 million pixels, whereas a CCD has a single, common output node
resulting in a uniform response. The most common problems are pixel-to-pixel
non-uniformity in gain and offset, Random Telegraph Noise (RTN,) and defective pixels
with abnormal noise or dark current characteristics (i.e., hot pixels.)
Often solutions to these challenges are found in the digital domain, where Kuro's
advanced real time signal processing corrects each pixel for gain and offset variation
using calibration at the factory. To address RTN and other pixel defects, real-time digital
filters are used.
Summary of Contents for Kuro
Page 1: ...www princetoninstruments com Kuro sCMOS Camera System Manual 4411 0159 Issue 2 March 28 2019...
Page 6: ...6 Kuro sCMOS Camera System Manual Issue 2 This page is intentionally blank...
Page 18: ...18 Kuro sCMOS Camera System Manual Issue 2 This page is intentionally blank...
Page 24: ...24 Kuro sCMOS Camera System Manual Issue 2 This page is intentionally blank...
Page 34: ...34 Kuro sCMOS Camera System Manual Issue 2 This page is intentionally blank...
Page 42: ...42 Kuro sCMOS Camera System Manual Issue 2 This page is intentionally blank...