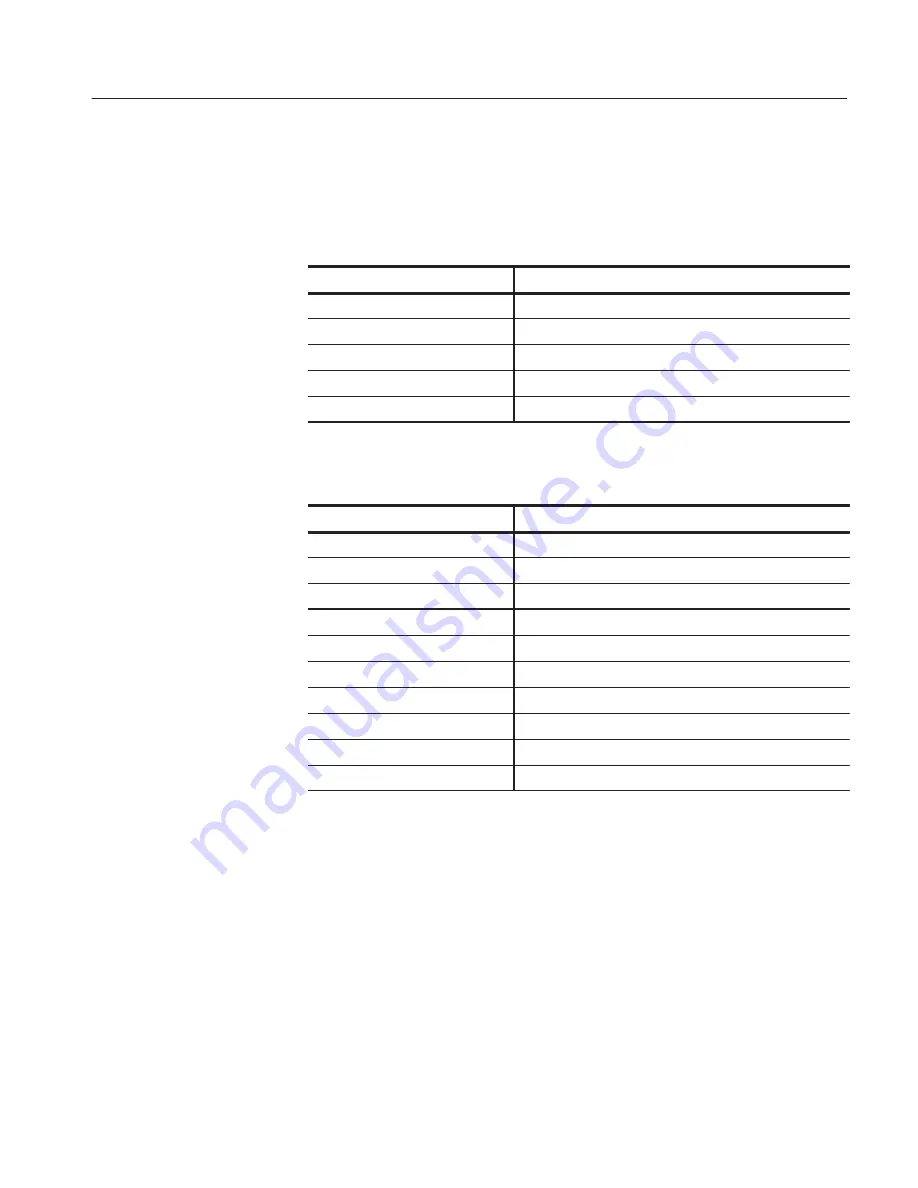
Maintenance
TDS 200 Series Digital Oscilloscope Service Manual
6–45
9. Use the test oscilloscope and set the Attenuation switch to 10X on the P2100
probe to probe the front panel module cable connector at J603 (two channel
oscilloscopes) or J103 (four channel oscilloscopes) on the main board. The
table below describes the signals you should expect to see.
Signal J603
Description
1
FDCLR
Positive Pulses, 100 ns wide (typical), 280
m
s period
2
+5 V
+5 V
3
FPCLR
Negative clock pulses, 100 ns wide (typical), 4.5
m
s period
4
GND
0 V (ground)
5
FPDATA
Negative pulse burst, 300
m
s period (typical)
Signal J103
Description
1
GND (0 V)
2
Negative clk pulse, 80 ns wide, 4.5
m
s period (typical)
3
Positive pulse, 100 ns wide (typical), 280
m
s period
4
Positive pulse, 100 ns wide, 280
m
s period (typical)
5
Negative pulse, 80
m
s wide, 4.5
m
s period (typical)
6
GND (0 V)
7
Negative pulse burst, 300
m
s (typical)
8
+5 V
9
Negative pulse burst, 300
m
s (typical)
10
—14 V (typical)
10. If all of the signals are present, the front panel board is probably defective.
Replace it.
11. If some or all of the signals are missing, continue with step 12.
12. Turn the instrument off and disconnect the front panel module cable from the
main board at connector J603 or J103.
13. Turn on the instrument and check connector J603 or J103 for the same
signals as in step 9.
14. If some or all of the signals are missing, the main board is probably
defective. Replace it.
Summary of Contents for TDS200 Series
Page 4: ......
Page 12: ...Service Safety Summary viii TDS 200 Series Digital Oscilloscope Service Manual ...
Page 22: ...Specifications 1 8 TDS 200 Series Digital Oscilloscope Service Manual ...
Page 32: ...Operating Information 2 10 TDS 200 Series Digital Oscilloscope Service Manual ...
Page 56: ...Adjustment Procedures 5 10 TDS 200 Series Digital Oscilloscope Service Manual ...
Page 106: ...Options 7 2 TDS 200 Series Digital Oscilloscope Service Manual ...
Page 108: ...Electrical Parts List 8 2 TDS 200 Series Digital Oscilloscope Service Manual ...
Page 110: ...Diagrams 9 2 TDS 200 Series Digital Oscilloscope Service Manual ...