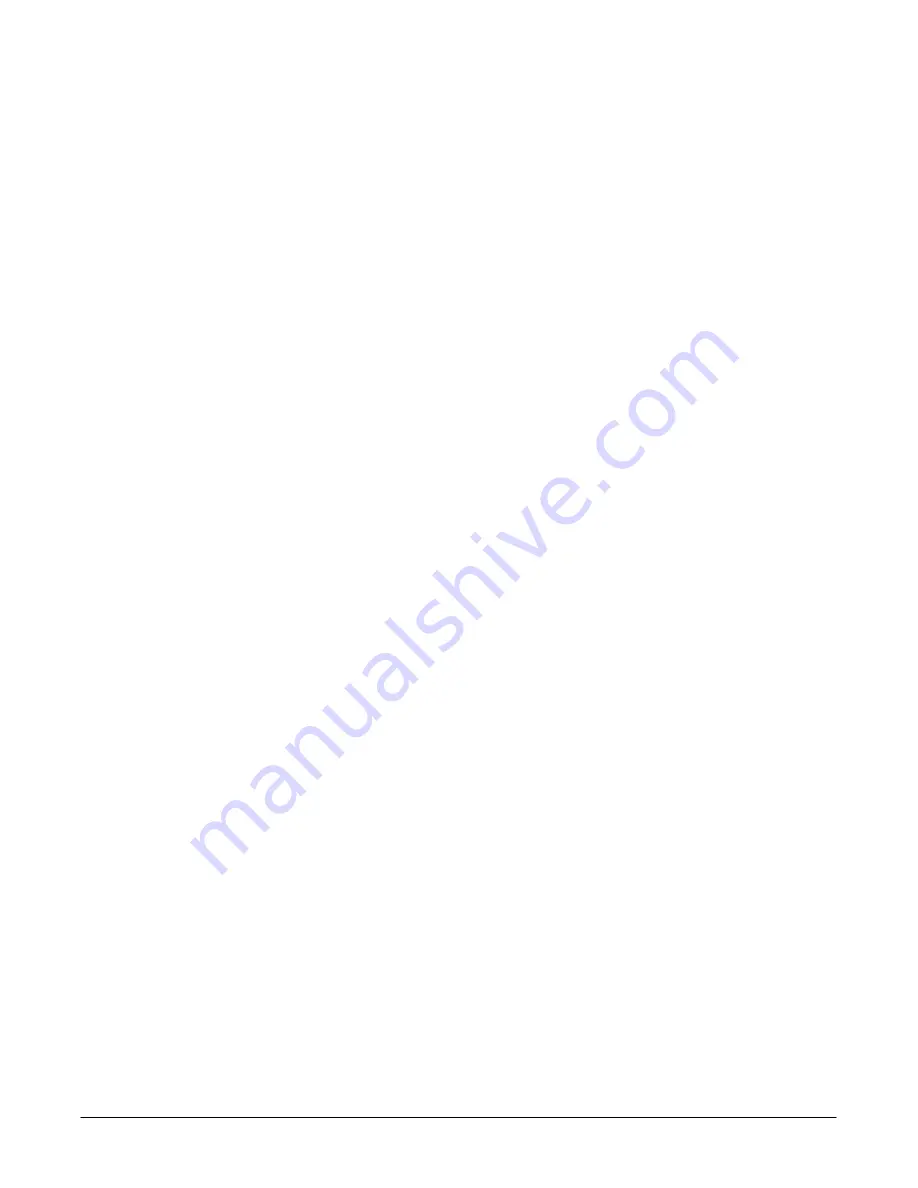
6Ć25
" !
NOTE
This procedure includes removal and reinstallation instructions for
the front panel and front panel buttons. Unless either of those
modules are being serviced, do not do step 4, Further disassemĆ
bly of frontĆpanel assembly."
Assemble equipment and locate modules to be removed:
) ", &%*%)% *' &- . #%+
R
'$ '!& "
#' ' !#( & '# %!#) " ' #'#% %!
External
Modules
(% .
# ' $%#(%
Front Cover, Trim Ring, Menu Buttons, and AttenuĆ
ator Panel,
&'$& !!' , $%" '& $%#(%
Orient the oscilloscope:
' ' #& #&#$ &# '& #''#! & #*" #"
' *#% &(% " '& %#"' & " ,#(
Remove the frontĆpanel assembly:
' ' %#"'.$" &&! , #(' # ' %#"' &($" ("' ,#( "
% ' "'%#""' #""'" ' '# ' $%#&&#%&$ ,
#%
&#""' '' ' # ' $%#&&#%&$ , #% &#".
"' ' +.#% #""'#% ' # ' %#"'.$" &&! ,
+ #% & $%' # ' &$ ,.%! &&! ,
" , ' ' %#"'.$" &&! , #(' # ' %#"' &($" '#
#!$ ' ' %!#)
Summary of Contents for TDS 620A
Page 4: ......
Page 6: ...2 2 1 2 2 2 1 0 1 0 1 0 2 0 1 1 1 2 2 1 2 1 1 0 1 2 1 1 1 2 1 1 2 2 2 1 2 2 1 1 1 1 1 1 2 2 2...
Page 10: ...vi...
Page 14: ...x...
Page 16: ...xii...
Page 17: ...xiii H H H H...
Page 18: ...xiv...
Page 19: ...xv...
Page 20: ...xvi...
Page 21: ......
Page 23: ...1 2 2 2 0 2 1 0 0 0 2 0 1 0 2 0 main 2 0 side 2 2 0 1 0 0 0 selecting 2 2 adjust 0 0 1 1 2 0 0...
Page 29: ...1 8...
Page 38: ...1 17...
Page 39: ...1 18...
Page 43: ...1 22...
Page 44: ......
Page 50: ...2 6...
Page 55: ...2 11 0 0 0...
Page 56: ...2 12...
Page 57: ...2 13 WARNING...
Page 61: ...2 17 9 11 12 14 13 10 0 V...
Page 62: ...2 18 18 17 15 16...
Page 65: ...2 21 H H Adjustment Procedures...
Page 66: ...2 22...
Page 67: ......
Page 71: ...3 4...
Page 72: ......
Page 74: ...4 2 H H H H H Initialize the oscilloscope Initialize the oscilloscope H Pass...
Page 88: ...4 16...
Page 92: ...4 20...
Page 108: ...4 36 Check against limits Disconnect the hookup...
Page 130: ...4 58 Check against limits H H Disconnect the hookup...
Page 141: ...0 2 1 4 69 H H H H 1 H H 1 6 5 1 0 1 4 0 1 0 2 H H 1 0 H H 0 3 0 4 H 01...
Page 146: ...4 74...
Page 147: ......
Page 171: ...5 24...
Page 172: ......
Page 175: ...1 0 6 3 3 5 4 1 0 2 5 0 1 0 2 1 0 1 1 1 3 0 5 3 3...
Page 176: ...6 4...
Page 186: ...6 14 A16 Power Supply Front Subpanel A20 Display Assembly Main Chassis...
Page 187: ...6 15 A16 Power Supply Front Subpanel A30 Display Assembly Main Chassis...
Page 194: ...6 22...
Page 196: ...6 24 Remove the trim ring Remove the attenuator panel Reinstallation...
Page 199: ...6 27 Reinstallation Front Cover Trim Ring Menu Buttons and Attenuator Panel...
Page 207: ...6 35 Remove circuit board assembly R Remove circuit board from assembly...
Page 210: ...6 38...
Page 211: ...6 39...
Page 212: ...6 40...
Page 227: ...6 55 WARNING WARNING WARNING WARNING J305 J170 J570 J350...
Page 228: ...6 56 Remove the display supply board...
Page 237: ...6 65 0 0 0 1 Rear Cover and Cabinet 0 0 0 0 0 0 0 0 1 0 0...
Page 241: ...6 69 1 0 1 0 1...
Page 242: ...6 70 J5 A17 Main LV Power Supply Module 1 39 1 39 J6...
Page 247: ...6 75...
Page 251: ...6 79...
Page 252: ...6 80 Pin 5 Pin 7 Pin 9 Pin 11...
Page 253: ......
Page 259: ...7 6...
Page 260: ......
Page 261: ...8 1 Mechanical Parts List...
Page 262: ...8 2...
Page 263: ......
Page 265: ...9 2...
Page 266: ...9 3...
Page 267: ...9 4...
Page 269: ...9 6 A20 CRT Driver for Monochrome Models only TDS 620A and TDS 640A...
Page 270: ......
Page 275: ...10 5 External Modules...
Page 277: ...10 7...
Page 279: ...10 9...
Page 281: ...10 11...
Page 283: ...10 13...
Page 286: ...10 16...
Page 287: ......
Page 288: ......