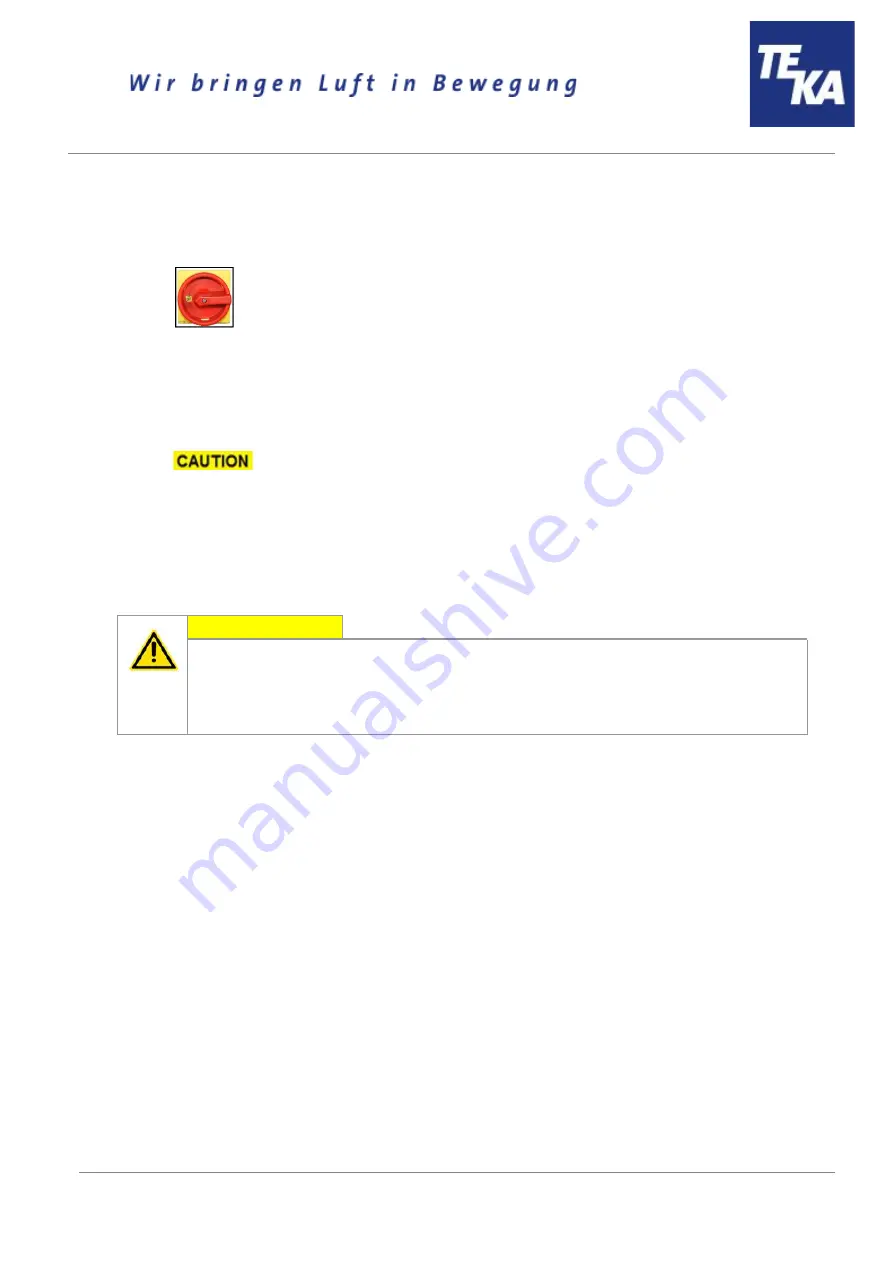
7.1. Reset to maintenance state
●
Switch off the unit. Then disconnect the unit from the power supply by setting the main switch in
the “OFF” position. Secure the unit against unauthorized restarting during maintenance.
●
Disconnect the compressed air hose of the external compressed air supply from the insert
sleeve (see chapter 2.1).
●
Empty the compressed air tank by opening the drain valve (see chapter 2.1) with a suitable
screwdriver. Minor quantities of condensation water can leak out when opening the drain valve.
Close the drain valve when the compressed air tank is entirely empty.
When opening the drain valve a compressed air blast can occur!
●
After completion of all maintenance work the unit can be reconnected to the power supply and
the external compressed air supply.
7.2. Cleaning the filter cartridges
CAUTION
A sudden jet of compressed air and huge amounts of whirled up dust are possible
due to an automatic cleaning with an opened service door.
During the operation of the device, the service door of the filter housing must not be opened.
The same applies to the ready to operate condition (standby) as there is also the possibility
of an automatic cleaning (subsequent cleaning).
The filter cartridges are reusable filters and can be cleaned. The cleaning of the filter cartridges is
automatically carried out.
The degree of pollution of the filter cartridges is electronically monitored. In order to assure the required
extraction capacity of the device, the cleaning of the filter cartridges starts automatically when a preset
differential pressure value is reached. If the preset differential pressure value is not undercut after the
cleaning of the filter cartridges, another cleaning starts. The filter unit remains in operation during the
automatic cleaning. The compressed air blast is produced in opposite direction to the intake. The
cleaned dust falls downwards in the dust collecting tank.
Depending on the setting of the control unit there can be automatic postcleanings of the filter cartridges
even when the unit is switched off.
When the maximal admissible differential pressure value is reached, the device triggers an alarm (see
chapter “description of the control elements”). If despite of the automatic cleaning of the filter cartridge
the alarm value is not undercut anymore, the filter cartridge must be replaced. (see chapter: “Replacing
the filter cartridges”).
The differential pressure values in the control unit that initiate a cleaning or a filter alarm are preset
values adapted to the filter unit. Please find detailed information concerning the functioning in the
enclosed operating instructions of the control unit.
BA_Airtech_P10_IFA_190319_EN
14
19.03.2019