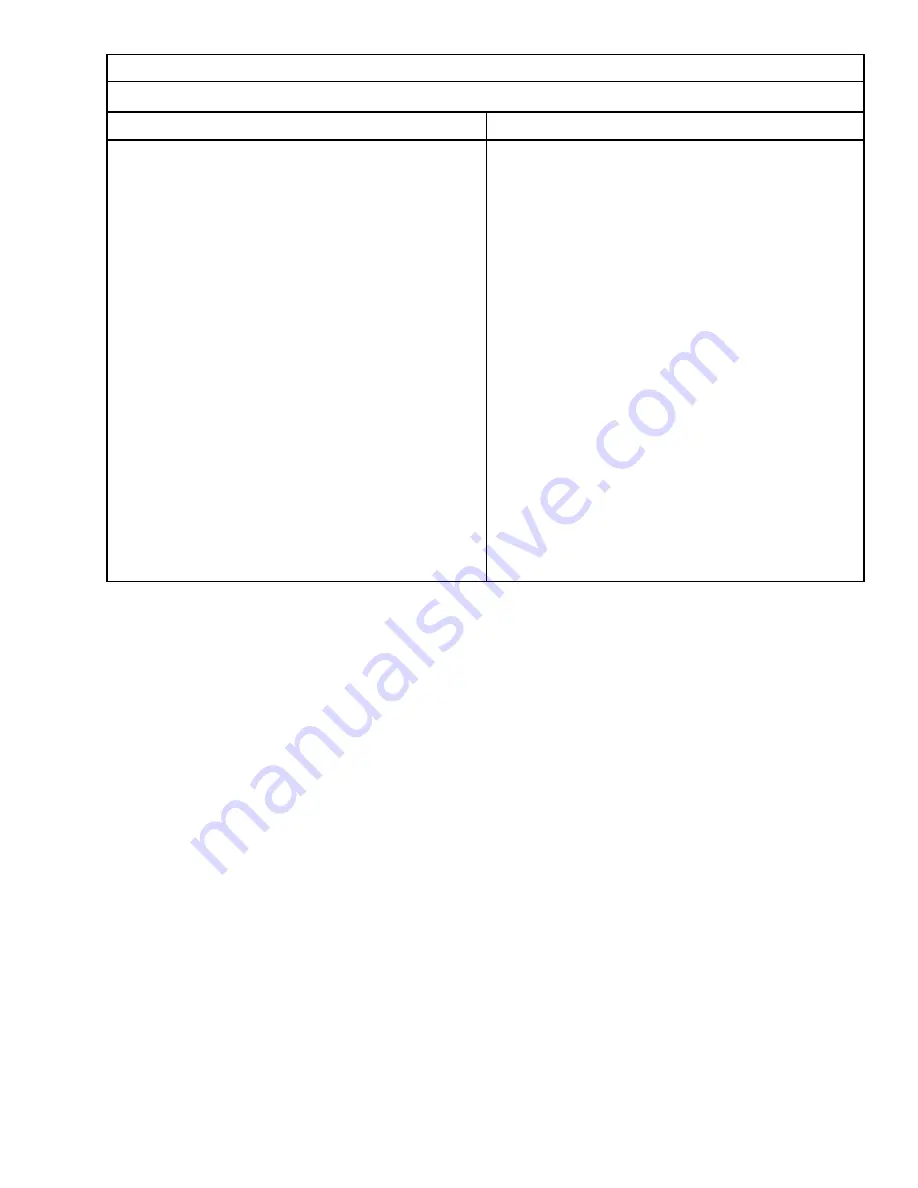
65
K. TROUBLE SHOOTING CARBURETION
POINTS TO CHECK FOR CARBURETOR MALFUNCTION
Trouble
Correction
Carburetor out of adjustment .....................................
4-12-13-14-15-17-22
Engine will not start ....................................................
1-2-3-4-5-6-7-9-12-13
Engine will not accelerate ..........................................
3-4-12-13-14-26
Engine hunts (at idle or high speed) .........................
4-5-9-10-11-12-13-14-22-23-26
Engine will not idle ......................................................
5-9-10-12-14-15-16-22-23-24-26
Engine lacks power at high speed ............................
3-4-7-9-12-13-22-23-26
Carburetor floods ........................................................
5-8-19-23-24
Carburetor leaks .........................................................
7-8-11-20-25-26
Engine overspeeds .....................................................
9-10-12-16-17-20-22
Idle speed is excessive ..............................................
9-10-15-16-17-20-22
Choke does not open fully .........................................
9-10-17
Engine starves for fuel at high speed (leans out) ..
1-2-4-5-7-12-17-19-21-23
Carburetor runs rich with main adjustment needle
8-12-19-20-21-23
shut off
Performance unsatisfactory after being serviced ..
1thru 14 and 17 thru 23
1. Open fuel shut-off valve at fuel tank, fill tank
with fuel.
2. Examine and clean fuel line and filter (where
applicable).
3. Check ignition, spark plug and compression.
4. Clean air cleaner, service as required.
5. Dirt or restriction in fuel system, clean tank and
fuel strainers, check for kinks or sharp bends.
6. Check for stale fuel or water in fuel, fill with fresh
fuel.
7. Examine fuel line and pick-up for sealing at fittings.
8. Check and clean atmospheric vent holes.
9. Examine throttle and choke shafts for binding
or excessive play, remove all dirt or paint, replace
shaft.
10. Examine throttle and choke return springs for
operation.
11. Examine idle and main mixture adjustment screws
and “O” rings for cracks or damage.
12. Adjust main mixture adjustment screw. Check
to see that it is the correct screw.
13. Examine main nozzle and replace with service
nozzle.
14. Adjust idle mixture adjustment screw. Check to
see that it is the correct screw.
15. Adjust idle speed screw.
16. Check position of choke and throttle plates.
17. Adjust control cable or linkage to assure full choke
and carburetor control.
18. Clean carburetor after removing all non-metallic
parts that are serviceable. Trace all passages.
19. Check inlet needle and seat condition and proper
installation.
20. Check sealing of welch plugs, cups, plugs and
gaskets.
21. Check fuel pump operation of pulse pump, clean
the pulse line after removing it from the pump
and engine fittings.
22. Adjust governor linkage.
23. Adjust float setting.
24. Check float shaft for wear and float for leaks or
dents.
25. Check seal for fuel drain or bowl gasket.
26. Is carburetor operating at excessive angle, 31°
or more ?
Summary of Contents for HH100
Page 77: ...75 ...