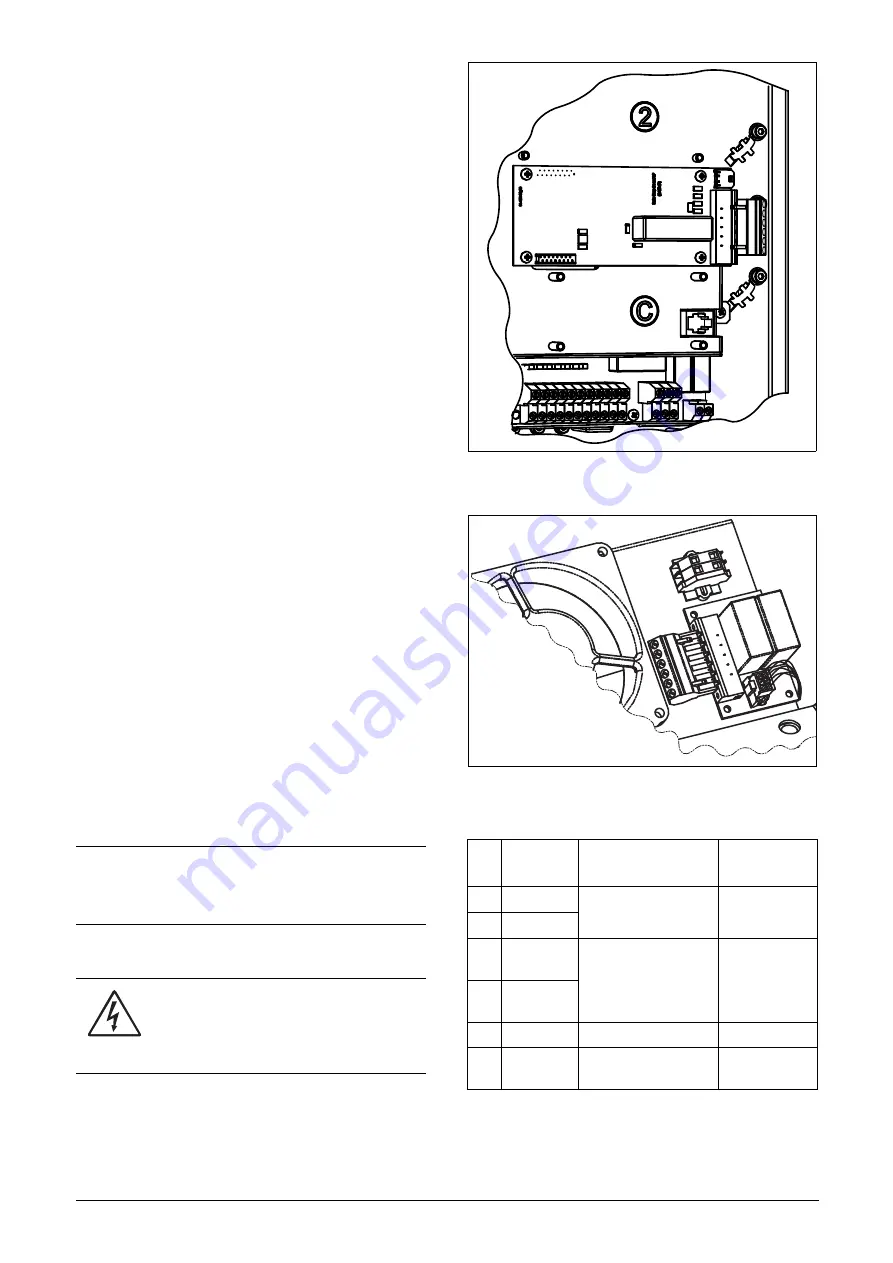
160
Options
When the "Safe Stop" condition is achieved by using
these two different methods, which are independently
controlled, this safety circuit ensures that the motor will
not start running because:
• The 24V
DC
signal is taken away from the "Inhibit"
input, terminals 1 and 2, the safety relay K1 is
switched off.
The supply voltage to the driver circuits of the power
conductors is switched off. This will inhibit the trig-
ger pulses to the power conductors.
• The trigger pulses from the control board are shut
down.
The Enable signal is monitored by the controller cir-
cuit which will forward the information to the PWM
part on the Control board.
To make sure that the safety relay K1 has been
switched off, this should be guarded externally to
ensure that this relay did not refuse to act. The Safe
Stop option board offers a feedback signal for this via a
second forced switched safety relay K2 which is
switched on when a detection circuit has confirmed
that the supply voltage to the driver circuits is shut
down. See Table 37 for the contacts connections.
To monitor the "Enable" function, the selection "RUN"
on a digital output can be used. For setting a digital out-
put, e.g. terminal 20 in the example Fig. 126, please
refer to section 11.5.4, page 128 [540].
When the "Inhibit" input is de-activated, the VSD display
will show a blinking "SST" indication in section D (bot-
tom left corner) and the red Trip LED on the Control
panel will blink.
To resume normal operation, the following steps have
to be taken:
• Release "Inhibit" input; 24V
DC
(High) to terminal 1
and 2.
• Give a STOP signal to the VSD, according to the set
Run/Stop Control in menu [215].
• Give a new Run command, according to the set
Run/Stop Control in menu [215].
Fig. 124 Connection of safe stop option in size B and C.
Fig. 125 Connection of safe stop option in size E and up.
NOTE: The method of generating a STOP command is
dependent on the selections made in Start Signal Level/
Edge [21A] and the use of a separate Stop input via
digital input.
WARNING: The safe stop function can never
be used for electrical maintenance. For
electrical maintenance the VSD should
always be disconnected from the supply
voltage.
Table 37
Specification of Safe Stop option board
X1
pin
Name
Function
Specification
1
Inhibit +
Inhibit driver circuits of
power conductors
DC 24 V
(20–30 V)
2
Inhibit -
3
NO contact
relay K2
Feedback; confirmation
of activated inhibit
48 V
DC
/
30 V
AC
/2 A
4
P contact
relay K2
5
GND
Supply ground
6
+24 VDC
Supply Voltage for oper-
ating Inhibit input only.
+24 V
DC
,
50 mA
1
2
3
4
5
6
1
2
3
4
5
6
Summary of Contents for F33 Series
Page 1: ...TECO F33 Variable Speed Drive Instruction manual English Software version 4 2X...
Page 3: ......
Page 33: ...30 Getting Started...
Page 51: ...48 Main Features...
Page 53: ...50 EMC and Machine Directive...
Page 59: ...56 Operation via the Control Panel...
Page 65: ...62 Serial communication...
Page 159: ...156 Troubleshooting Diagnoses and Maintenance...
Page 165: ...162 Options...
Page 179: ...176 Technical Data...
Page 187: ...184 Menu List...