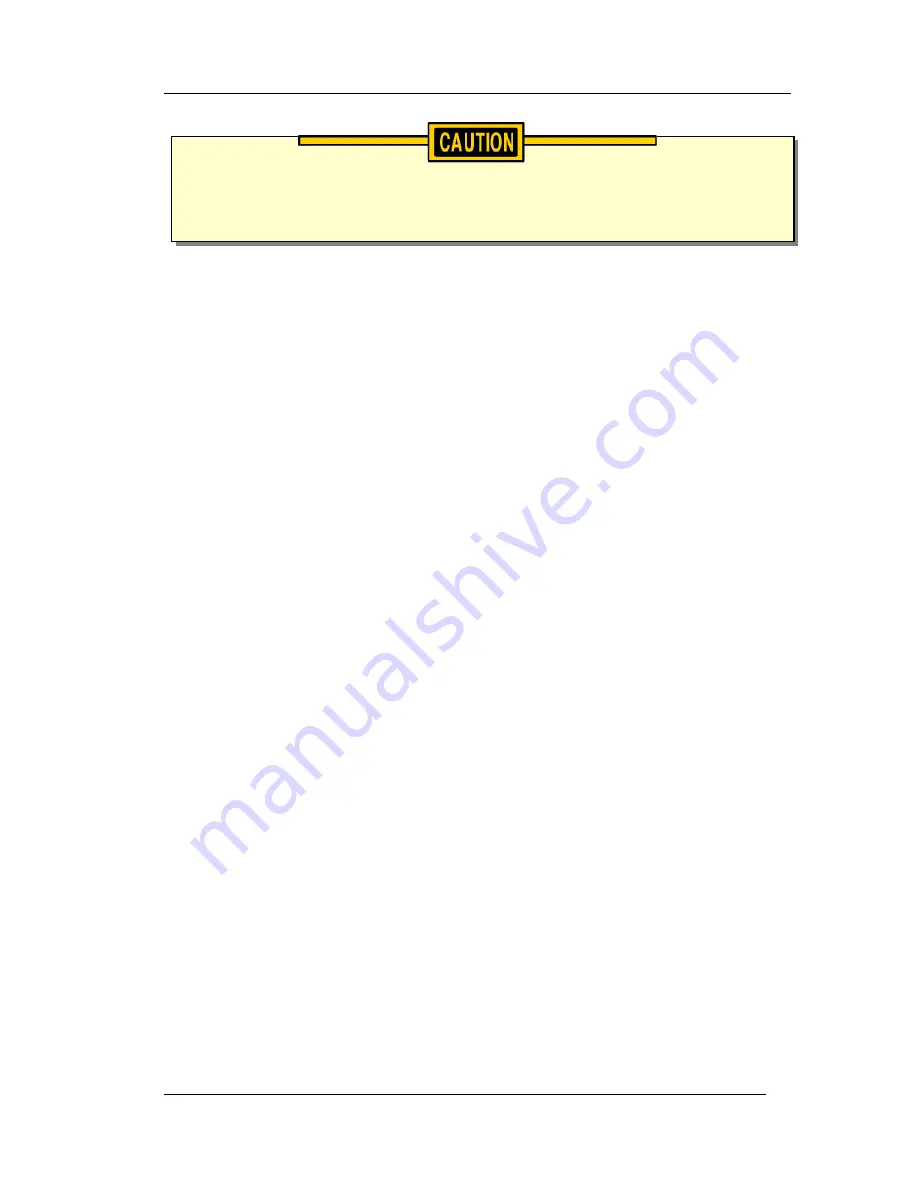
Teco Installation and Maintenance Manual
TEFC Squirrel Cage Induction Motors
Teco Electric and Machinery Company
Manual Number: IOM ~ TEFC Rev.01
31
6.1.6. Checking motor installation and coupling.
a.
Installation:
i.
Is foundation solid?
ii.
Are all bolts and/or nuts tight and in good order?
b.
Coupling:
i.
Is coupling in good order?
ii.
Are fasteners tight and in good order?
6.2.
CLEANING OF COILS, DRYING & VARNISHING TREATMENT.
Age, constant heating and cooling and other factors may cause insulation
deterioration. Also, salt deposits or grease may lower insulation resistance.
Steam cleaning, drying and re-varnishing may be necessary if the motor has
been flooded or showing deterioration from age.
6.2.1. Cleaning:
a.
If the coils are slightly contaminated, compressed air, cloth or a nylon brush
can be used to do the cleaning. However, when contamination is serious,
thorough washing has to be performed. The cleaning methods are as
follows:
b.
Cleaning with water:
i.
This method is applicable to motors having been immersed in water or
insulated with no cotton yarn and paper materials.
ii.
After washing, dry immediately.
iii.
Cleaning with steam.
If the motor has been immersed in sea-water or a chemical solution, clean
with steam after washing thoroughly.
Steam pressure must be kept between 2 – 4 kg/cm
2
. High pressure may
cause insulation damage.
Motors should never be cleaned or disturbed whilst the motor is in
operation.
Isolate motor from supply before cleaning.