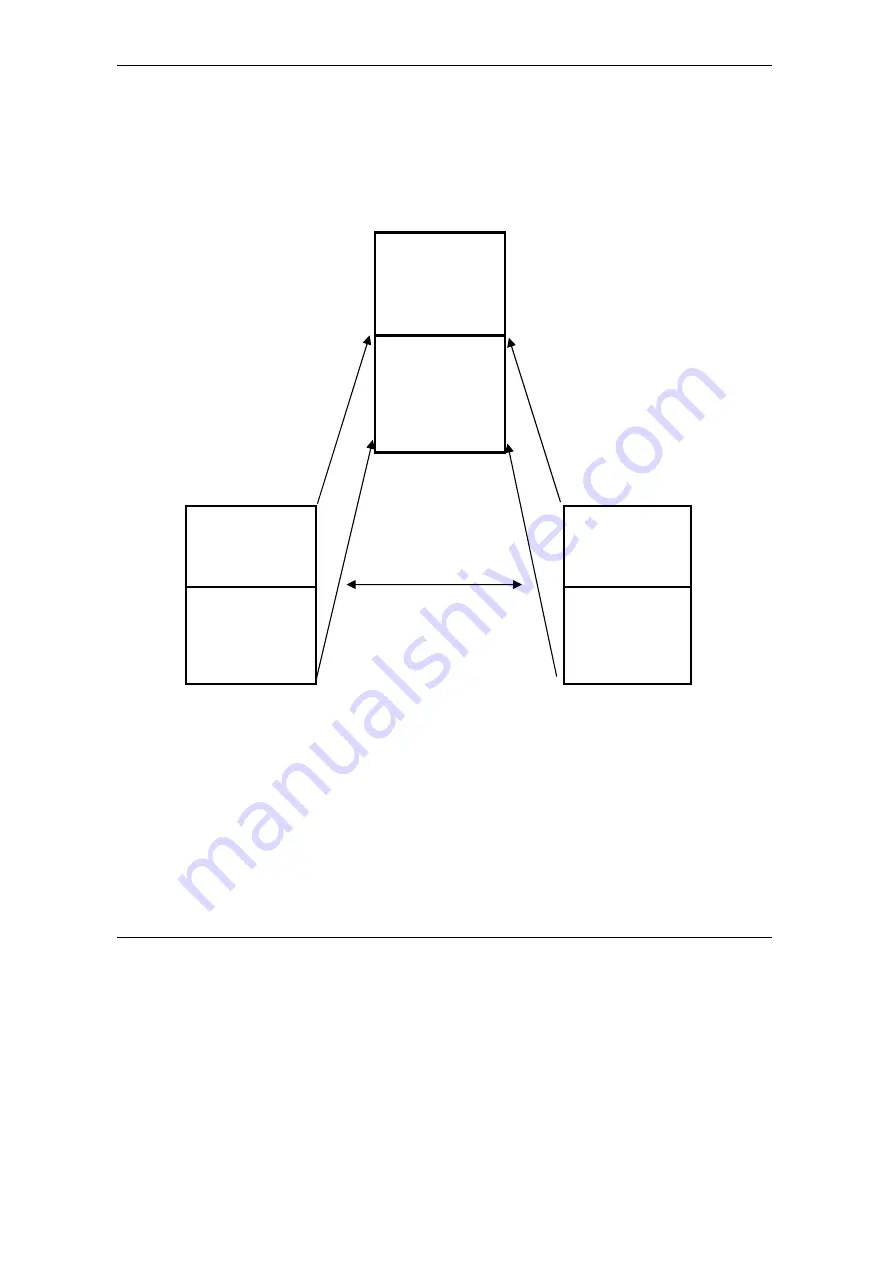
©
Technosoft 2007
68
IPS110 Technical Reference
7. Memory Map
The drive has 2 types of memory: a 1.5K
×
16 SRAM (internal) memory and an 8K
×
16 serial
E
2
ROM (external) memory.
Physical memory
4000h
E
2
ROM (SPI)
Memory
5FBEh
Internal SRAM
Memory
Program Memory
(PM)
Data Memory
(DM)
8270h
Program Memory
for TML programs
0A70h
Not used as
Data Memory
Not used as
Program Memory
87FFh
Data Memory
for data
acquisition
0FFFh
Figure 7.1.
IPS110 Memory Map
The SRAM memory is mapped both in the program space (from 8270h to 87FFh) and in the data
space (from A70h to FFFh). The data memory can be used for real-time data acquisition and to
temporarily save variables during a TML program execution. The program space can be used to
download and execute TML programs. It is the user’s choice to decide how to split the 1.5-K
SRAM into data and program memory.
The E
2
ROM is seen as 8K
×
16 program memory mapped in the address range 4000h to 5FBEh. It
offers the possibility to keep TML programs in a Non-volatile memory. Read and write accesses to
the E
2
ROM locations, as well as TML programs downloading and execution, are done from the
Summary of Contents for IPS110
Page 2: ......
Page 4: ......
Page 6: ......
Page 12: ... Technosoft 2007 VI IPS110 Technical Reference ...
Page 82: ... Technosoft 2007 70 IPS110 Technical Reference This page is empty ...
Page 83: ......
Page 84: ......