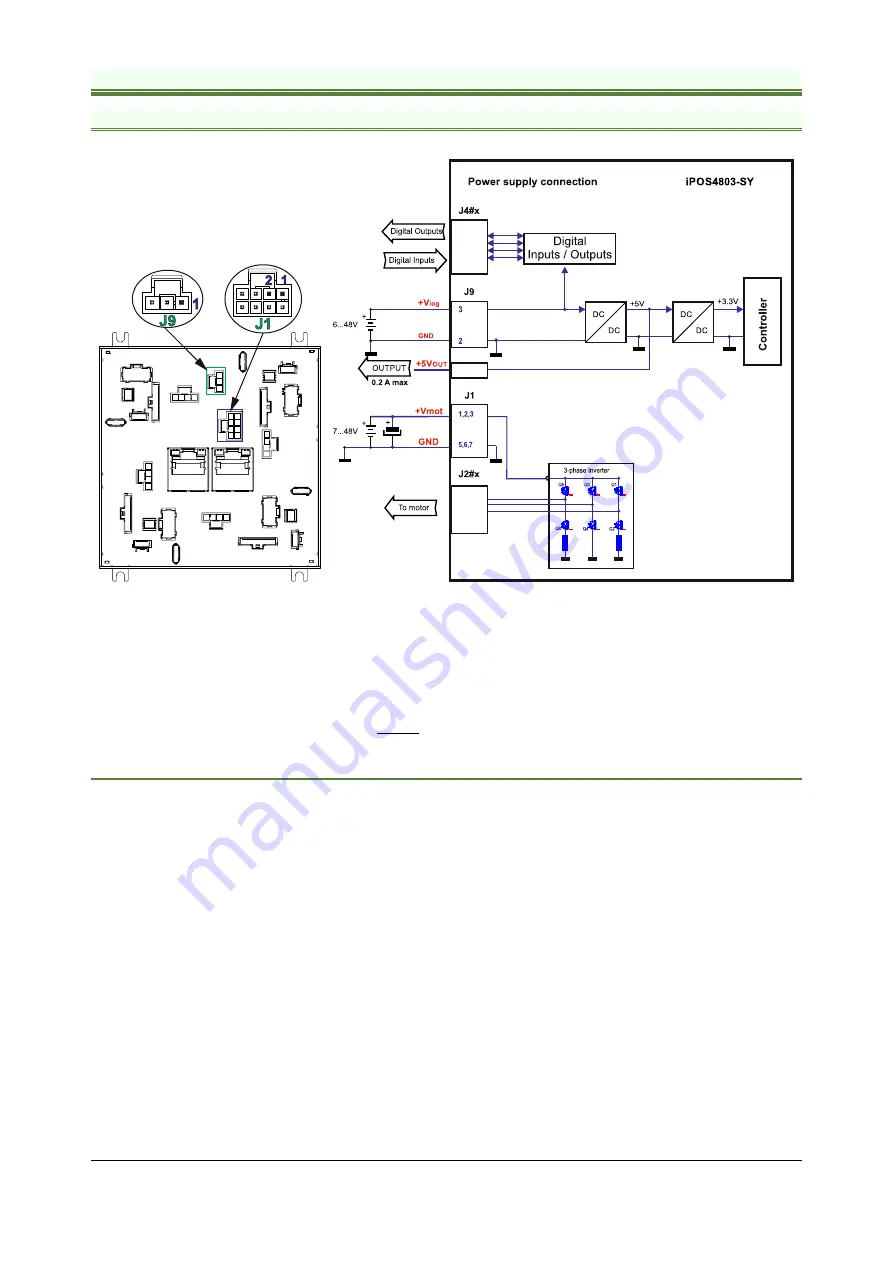
Technosoft 2021
25
iPOS4803-SY Multi Axis System, EtherCAT Technical Reference
3.9 Power Supply Connection
3.9.1 Supply Connection
Figure 17
Supply connection for iPOS4803S
Remarks:
1. The +V
log
inputs can be supplied from the same power source as long as its output voltage is 6 to 48V DC
from a SELV/ PELV power supply.
2. J9 connector is internally connected to all axis +V
log
inputs and GND.
3. An external electrolytic capacitor may be added bV
mot
and GND, to help reduce over-voltage during
load braking/ reversals. See paragraph 3.9.1.1 for details.
3.9.1.1
Recommendations for Supply Wiring
The iPOS4803-SY always requires two supply voltages: +V
log
and +V
mot
.
Use short, thick wires between the iPOS4803-SY and the motor power supply. Connect power supply wires to all the
indicated pins. If the wires are longer than 2 meters, use twisted wires for the supply and ground return. For wires
longer than 20 meters, add a capacitor of at least 1000
μF (rated at an a
ppropriate voltage) right on the terminals of
the iPOS4803-SY.