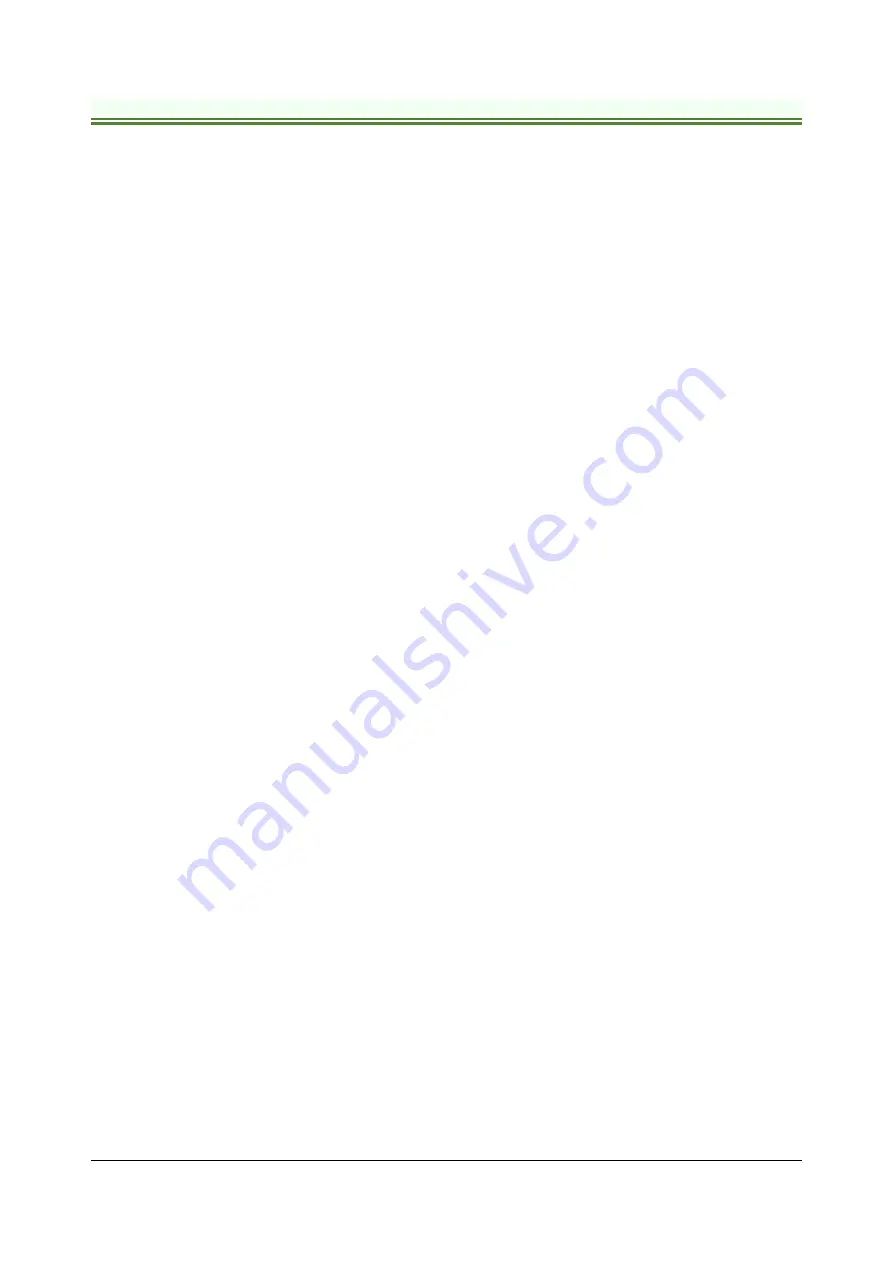
Technosoft 2022
9
iPOS4803-SY Multi Axis System, EtherCAT Technical Reference
2.2 Product Features
•
Fully digital servo multi axis system suitable for the control of rotary or linear brushless and DC brush
•
Very compact design
•
Sinusoidal (FOC) or trapezoidal (Hall-based) control of brushless motors
•
Technosoft Motion Language (TML) instruction set for the definition and execution of motion sequences
•
Standalone operation with stored motion sequences
•
Communication:
•
USB port for each axis
•
RS-232 serial for each axis
•
Dual 100Mbps EtherCAT® interfaces, for use in daisy-chaining topologies;
•
Digital and analog I/Os per axis:
•
3 digital inputs: 5-60V, 2 x limit sw 1 x Enable input, NPN, pull-to-GND to activate
•
3 x individually configurable input/output pins:
•
Digital input, 5-60V, NPN, pull-to-GND to activate, with pull-up on-board to +5V
•
Digital output, 5-60V, NPN (open-collector),I/O0 able to pull 1.5A able to drive inductive loads (such
as mechanical brake), I/O1&4 can pull 0.1A , with +5V on-board pull-ups
•
Feedback devices per axis (dual-loop support)
1
st
feedback devices supported:
•
Incremental A / B (index Z available only for 1 encoder): differential or single-ended
•
Pulse & direction interface (single-ended or differential) for external (master) digital reference
•
BISS / SSI / EnDAT / TAMAGAWA / Panasonic/ Nikon/ Sanyo Denki encoder interface
2
nd
feedback devices supported:
•
Incremental encoder interface (differential)
•
Pulse & direction interface (differential) for external (master) digital reference
•
BISS / SSI / EnDAT / TAMAGAWA / Panasonic/ Nikon/ Sanyo Denki encoder interface
Separate feedback devices supported:
•
Hall sensors interface (digital or linear)
•
1 analogue input:
16bit ±10V or 12-bit 0-5V: Reference, Feedback or general purpose
•
Various motion programming modes:
•
Position profiles with trapezoidal or S-curve speed shape
•
Position, Velocity, Time (PVT) 3
rd
order interpolation
•
Position, Time (PT) 1
st
order interpolation
•
Cyclic Synchronous Position (CSP) for CANopen mode and EtherCAT® drives.
•
Cyclic Synchronous Velocity (CSV) only for EtherCAT® drives.
•
Cyclic Synchronous Torque (CST) only for EtherCAT® drives.
•
Electronic gearing and camming
•
35 Homing modes
•
EtherCAT® supported protocols for CAT drives:
•
FoE
– File over EtherCAT – for setup/TML functions and firmware update
•
EoE
–
Ethernet over EtherCAT – for Easy Motion studio communication over EtherCAT
•
16K
×
16 internal SRAM memory for data acquisition
•
16K
×
16 E
2
ROM to store TML motion programs, cam tables and other user data
•
PWM switching frequency up to 100kHz
•
Motor supply: 7-48V
DC
•
Logic supply: 6-48V
DC
•
Operating ambient temperature: 0-40
°
C (over 40
°
C with derating)
•
Protections:
•
Short-circuit between motor phases
•
Short-circuit from motor phases to ground
•
Over-voltage
•
Under-voltage
•
Over-current
•
Over-temperature
•
Communication error
•
Control error