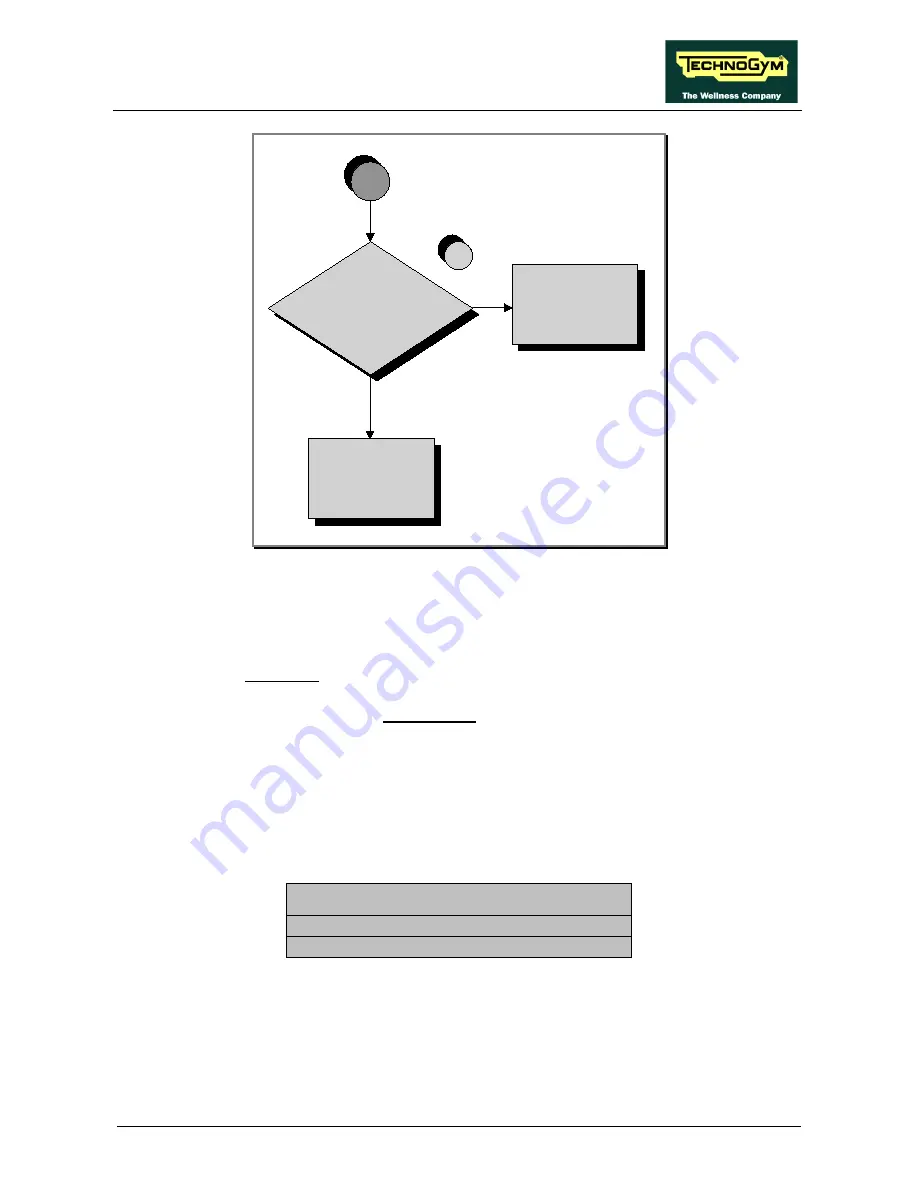
Forma Line BIKE FORMA (DDC5): Technical Assistance manual - rev. 1.1
Page 6.21
Are there sources of
electromagnetic noise near the
receiver?
Receiver Board defective.
Replace it.
NO
4
The problem does not
depend on the equipment
YES
A
Follow the chart step by step in order to make a correct diagnosis. In particular, pay attention to
the checks highlighted in the numbered boxes and listed here below:
(1)
Check on the correct SW version, according to the “EXCITE SW SMART TABLE” table
found in the
TG Direct
.
Carry out the earth check on the
HR Receiver
, by measuring the resistance value between the
following points with a tester:
a.
The faston on the
HR Bboard
and the earth pole on the Power Supply Box;
b.
The earth pole on the Power Supply Box and the wall socket.
The value must be less than 1Ω (Ohm).
Lastly check the earth on the wall socket, making sure there are the following voltages:
P – N
(phase– neutral)
= 220Vac / 110Vac
P – E
(phase– earth)
= 220Vac / 110Vac
N – E
(neutral– earth)
= 0Vac
Continues on the next page...
Summary of Contents for FORMA LINE BIKE FORMA DDC5 Series
Page 1: ...F FO OR RM MA A L LI IN NE E BIKE FORMA DDC5xxx Technical Assistance manual REV 1 1 ...
Page 2: ......
Page 4: ......
Page 8: ...Forma Line BIKE FORMA DDC5 Technical Assistance manual rev 1 1 Page iv Page blank ...
Page 28: ...Forma Line BIKE FORMA DDC5 Technical Assistance manual rev 1 1 Page 3 10 Page blank ...
Page 34: ...Forma Line BIKE FORMA DDC5 Technical Assistance manual rev 1 1 Page 5 4 Page blank ...
Page 58: ...Forma Line BIKE FORMA DDC5 Technical Assistance manual rev 1 1 Page 6 24 Page blank ...
Page 92: ...Forma Line BIKE FORMA DDC5 Technical Assistance manual rev 1 1 Page 7 34 Blank page ...
Page 116: ...Forma Line BIKE FORMA DDC5 Technical Assistance manual rev 1 1 Page 9 18 Page blank ...
Page 118: ......
Page 120: ......
Page 121: ......