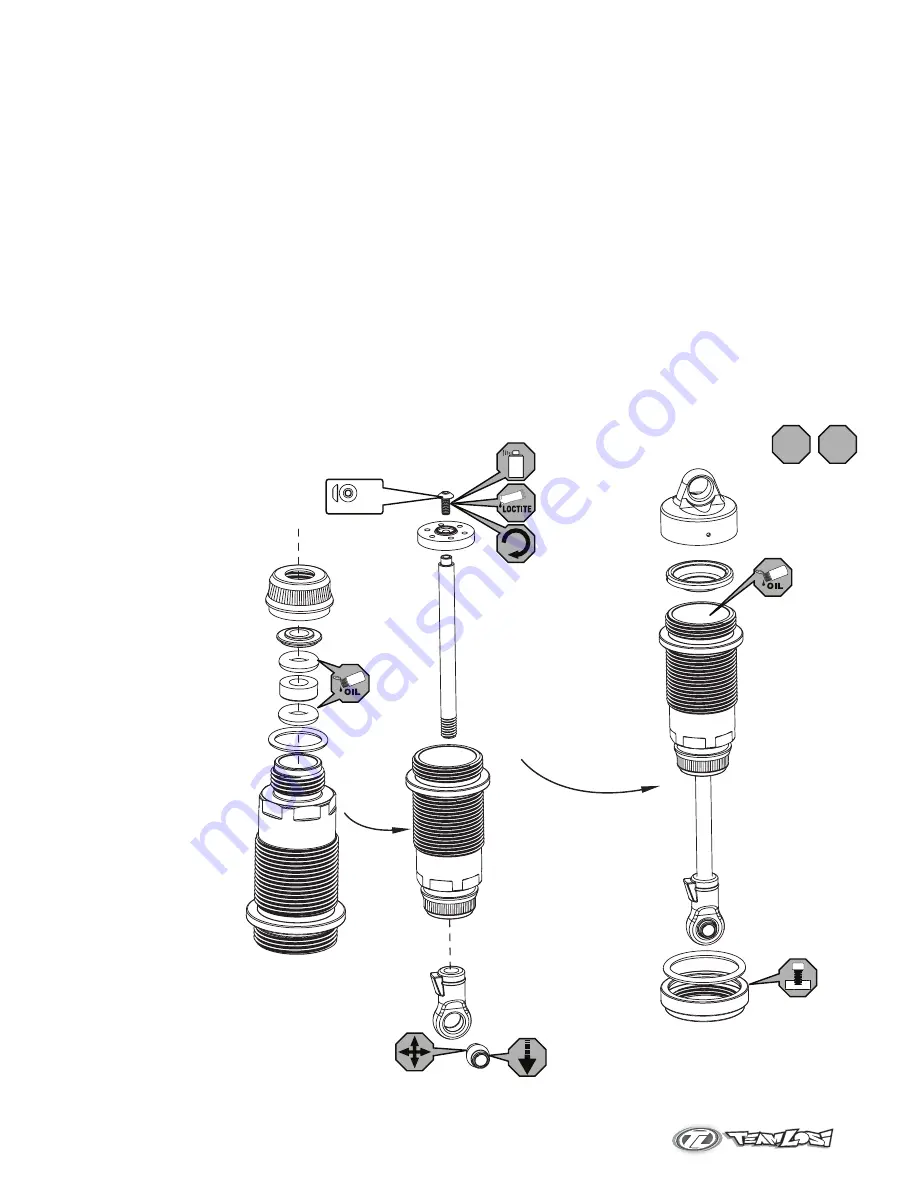
Clean the 2-56 x 1/4” button head screw and apply loctite to the threads.
Install the #55 shock piston using the 2-56 x 1/4” button screw into the shock shaft with a .050” allen wrench.
Place a drop of Shock Oil into the bottom of the Shock Body to lubricate the Shock Seals.
Thread the shock shaft into the shock end using pliers. Use caution when threading the shock shaft ends onto the shafts. Avoid gouging or scratching the shock
shaft while gripping the shock shaft with pliers by placing the edge of a towel over the shaft, then gripping the portion of the shaft covered by the towel. This method
will work very well to protect the shock shafts from damage.
Ensure the shaft is fully extended when filling the shock.
Fill the shock body with 35wt. shock oil until the oil is to the top of the body.
“Work” the shock shaft up and down a few times.
This will release the air bubbles trapped beneath the piston. Place the filled shock, in the upright position, o
ff to the side
for a few minutes until the air bubbles escape from the oil.
Once all the air bubbles are out of the oil, gently place the shock bladder onto the shock as shown. Some oil should “bleed” from the shock.
Screw the shock cap onto the body until some resistance is felt.
Slowly push the shock shaft up. This will bleed excess oil from the shock.
Tighten the cap all the way down using the shock tools included in your kit
.
Move the shock shaft up and down. The shaft should be easy to push up into the body of the shock. If increased pressure is felt towards the top, there is to much oil in
the shock. Loosen the shock cap and “bleed” the shock as done previously.
Make sure each pair (front/rear) shocks have the same rebound and compression. This is checked by holding one shock in each hand horizontally and pushing them
together by the shock end. Watch carefully to ensure that both compress evenly. Now release both shocks and again watch carefully as they should rebound the same.
•
•
•
•
•
•
•
•
•
•
•
•
•
Rebuilding/Refilling the Shocks
Rebuilding/Refilling the Shocks
Page 9
2-56 x 1/4”
x 1
x2 x2
Front
Rear